Jidoka is very popular with the product quality inspectors, who check items at the end of the production process. That’s because Jidoka ensures that a defect is identified and corrected immediately and not at the end of the process. This, therefore, reduces the pressure on a process engineers relying on final inspection.
So what happens if you don’t employ Jidoka? Here are four consequences of not doing so:
1) Risk of Overproduction
Take a factory not using the Toyota Production System. The machinery maybe is state-of-the-art, but as the company hasn’t embraced Jidoka, there is a risk that it may produce more parts that is actually needs to.
Why? Well, imagine that a brake crank case assembly line develops a tiny defect. The problem is so small that it doesn’t stop production, but at the same time the machinery can no longer be relied upon to produce quality components. Worse still, because the machinery is not programmed to identify faults, the issue only comes to light after stringent testing at the end of the production process. All the components that have been produced have to be consigned to the bin at considerable cost to the company.
2) Lost Labor
There are other costs to consider too. Not only has the company lost money on its defective stock, it has also had to pay machine operators to carry out the work, which is additional waste.
3) Transportation Time
Imagine all the components that go into manufacturing a brake crank. Now imagine all the different journeys each defective component would have made before finally being scrapped.
4) Re-Processing Time
Without a Jidoka system in place, it could be that the machinery cannot be used for a day or two until the original supplier sends one of its people to the plant to fix the faulty apparatus. Once back on line, there is no guarantee that the machinery won’t break again.
However, if the Jidoka method had been used, the facility project manager would have been able to access a database which would have helped him or her to identify why it malfunctioned in the first place, and when it is most vulnerable to break-down.
The sooner the problem is detected, the easier it is to fix and the smaller the impact. Thus, one of the important parts of Lean is to be able to detect problems, raise them quickly, analyze and fix.
What are some of the other consequences of not using Jidoka to control quality?

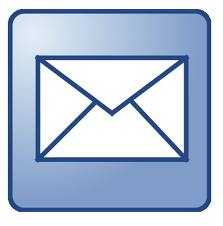





Some people have to learn the hard way. Meaning if you make too many bad parts and add the labor and transportation cost of repair or scrap. Then add the cost of identifying and fixing the root cause problem to get back to a certified part. All this is a learning process where without learning improvement cannot be made or gained. We lean by doing but often by learning and working smarter rather than harder with Jidoka we can often speed up the learning and improvement process or PDCA or DMAIC cycle. Working smarter is always easier and less costly than working harder. Learning to do Lean and Jidoka is all about working smarter by doing more with less can be better with less stress, cost, worry and head ache and arguing. It provides for much smoother work flows with higher quality and productivity yields.
ReplyDelete