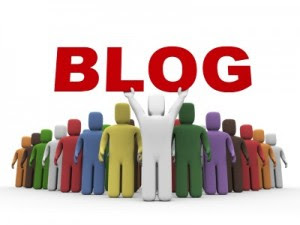
A
selection of highlighted blog posts from Lean bloggers from the month of December,
2018. You can also view the previous
monthly Lean Roundups here.
THE AGILE WAY
TO USE KANBAN IN SOFTWARE DEVELOPMENT – Shanie
Weissman discusses the use of Kanban approach in software development.
Respect
for “Respect for Human Nature” – Jon Miller explains three main
perspectives on the lean thinking pillar of respect for people.
Is
Five Why Analysis Too Simplistic for Complex Problems? – Pascal
Dennis explains why 5 why can get to the root cause of complex design, supply
chain and organizational problems.
How
Does the Teacher Learn? – Mark Rosenthal says the teacher
learns by sharing and swapping experiences with others.
Dismantling
Classical Management – Bob Emiliani talks about how
change happens in an organization.
Kaizen
and Improvements That Last – Michel Baudin discusses how to get
good results from kaizen ways to make them stick.
Customer
Satisfaction is Not Enough – John Hunter says to succeed over
the long term organizations must seek not to satisfy customers but to delight
customers.
What We See... – Bill
Bellows discussed his experience with Toyota and interpretation of Lean and why
it differs from the view of the Machine That Changed The World.
A
Day in the Life of a Gemba-focused Executive VP – Jon
Miller shares a great lesson on leading from the gemba with real example for
Toyota executive.
GM
Shrinking, Laying Off People, Shutting Down Factories, and Cutting Costs Isn’t
“Lean and Agile” – Mark Graban discusses how Lean can
be an alternative to slash-and-burn layoffs.
Ask Art: How Do
I Get the Senior Management Team On Board with Lean? – Art Byrne
explains that becoming a lean enterprise requires having a lean management
team.
Standardized
Work or Kaizen? Yes – John Shook explains why you want
both, and you can’t have much of one without a roughly equal dose of the other.
Soliciting
Suggestions in Ways That Don't Backfire – Cheryl
Jekiel shares specific ways to prevent mishandling ideas from your people.

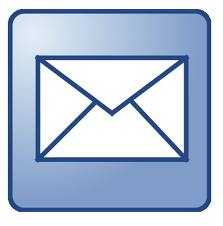




