Lean
manufacturing is all about continuously
improving work processes by identifying and eliminating waste, and the PDCA
cycle is one of the most valuable tools in the Lean toolbox. The PDCA cycle,
also commonly referred to as the Deming circle, is a
four-step system with the same principles as all Lean methodologies: improve
work processes and eliminate waste for maximum efficiency. If you’re
considering implementing Lean
principles or logistics to your facility, this cycle is a great introduction
to it.
PDCA
is an acronym of the four separate stages: Plan,
Do, Check, and Act.
Plan: In the first step, you
will assess the current state of the process, and look for any possible
improvements. Observe the workflow and talk to employees for insight. If a
problem is identified, examine it carefully and develop potential solutions. it
is important to gather as much information as you can in this step to help you
make informed decisions about how to proceed.
Do: It’s time to try out
the solutions you brainstormed in the first step. Make sure everyone involved
understands the changes. These changes are usually small, a
Implement
Check: Follow up with the
changes implemented and record relevant data. Analyze the new state of the
process and compare it to how things were before. Charting or graphing this
information could make it easier to identify trends for the next step.
Act: If you found the
changes to be effective, make them the standard! If the changes show no
improvement, the process will remain the same. Either way, this is important
information to be utilized in future PDCA cycles.
The
PDCA cycle
is such a valuable system because although it is a specific set of steps,
there is still a good deal of flexibility. The cycle can be practiced by
virtually anyone in the company, at any level of an organization, and can
address a number of problems or changes. Additionally, the PDCA cycle can be
tailored to fit the needs of your facility. Your company should establish
specific “sub-steps” that will help your unique situation. The more you outline
the that need to happen during each part of the cycle, the better things will
go.
The
specific phases balanced with a great deal of flexibility can understandably
lead to some confusion. The following are some FAQs about the PCDA:
Who should be trained
on the cycle?
Anyone
working within the company should understand what the PCDA cycle is and how it
works. Managers, team leaders, and workers on the floor should all have at
least a basic understanding of the cycle and be prepared to hit the ground
running no matter the step of the process. It will make the implementation of
changes smoother and more efficient.
What changes should go
through the PDCA cycle?
Making
the PDCA cycle mandatory for all changes that occur within the company could be
very beneficial for your facility. Workers will have more opportunities to
participate in different stages of the cycle and will set a standard and
formalized process for future changes made.
When should I use the
cycle?
Although
you can use the PDCA cycle in nearly any instance of change or improvement,
there are specific areas where the cycle is most beneficial. Some key instances
include:
· The beginning of a new
project
· The automation a
repetitive process
· Organizing
· Eliminating specific
wastes
How many times should I
use the cycle?
PDCA
is continuous with no real end in sight. Once a cycle is completed, you can
start looking for further solutions to implement in the future. Continue using
it on a specific area until the change has been fully implemented and
optimized.
How will I know the
effectiveness of the changes?
It’s
all about data and accurately measuring results. By documenting results with
each change, company leadership and management can clearly see the benefits of
this methodology and will help give you the data needed to ensure this process
continues long into the future.
About the
Author:
Jesse Allred is a blog writer for Creative Safety Supply leaders
in visual safety and Lean manufacturing resources. She enjoys sharing
information and advice for facilities to achieve efficiency while keeping
employees safe.

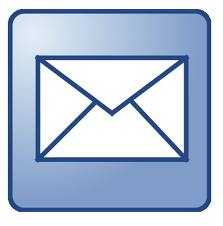





No comments:
Post a Comment