5S is a process and method for creating and maintaining an organized, clean, and high performance workplace. It enables anyone to distinguish between normal and abnormal conditions at a glance. 5S can be the foundation for continuous improvement, zero defects, cost reductions and a more productive work space. The 5S methodology is a systematic way to improve the workplace, processes and products through employee involvement.
When first getting started with 5S, it is important to foster employee engagement, monitor improvements, and create goals that are measurable. Doing the following things will help you get started and make your 5S program last.
1. Show that 5S works
One of the first things you can do to show how 5S can be applied in your workplace is to have your managers apply 5S to their offices. This will encourage your workers by showing them how 5S can improve efficiency on a small scale.
2. Train
The whole team should be trained in the vision and objectives of the company and given a clear understanding of what the company is trying to achieve through them and their 5S program implementation. They need to have a clear understanding of the seven wastes of lean and an overview of basic lean principles. With this knowledge they will be ready to undertake their 5S implementation.
3. Start small
It would be unwise to try to implement 5S throughout your entire organization in one go (unless you have a small company), better to select one area in which to concentrate your efforts and provide a show piece for the rest of the organization. In my mind it would be best to select the worst area in the company so as to show what can be achieved and the differences it can make. Showing success in one area gains the confidence of others and a reason to buy-in.
4. Leadership buy-In and commitment
Your management should understand and practice the ideas of 5S themselves so as to provide an example to your other employees, it would be hard to motivate your employees to keep a tidy workspace if every time they walked past their managers desk they saw piles of untidy clutter. Management needs to be ready to explain and help fix any situations that arise.
5. Don’t make it stand alone
Doing 5S is liberating. We have all experienced that feeling after cleaning the basement or garage after a year of accumulating stuff. But 5S is just one tool that enables stability that enables flow. Well organized and sparkling clean waste is still waste. Getting bogged down in 5S can be an avoidance pattern - avoiding the hard work of thinking about how to create flow and solve the real root cause problems inhibiting flow.
6. Positively promote it
Whether it’s before-and-after pictures or testimonials from users who have already completed a 5S project, there’s plenty of compelling evidence about how effective this discipline can be. At first you may have to draw these examples from the Internet or companies whose programs you’re emulating. But as your own 5S gains traction, they could just as easily come from the early adopters within your company. Either way, use your company’s internal communications tools to “sell” 5S often—and in varied ways.
7. Monitor, review, and improve
Once the team has completed the first activities they’ll need to focus on sustaining. The team should create standard audits to assess and score their area so that they can be monitored on an ongoing basis. In addition, the team should meet to review how things are working and what additional improvements they could make. Photographs should be taken of the improved work area and a 5S story board put up to show the improvements gained. I would also suggest that the team be allowed to make a presentation to the management and the rest of the organization to show off their achievements.
The 5S system is a good starting point for all improvement efforts aiming to drive out waste from the manufacturing process, and ultimately improve a company’s bottom line by improving products and services, and lowering costs. Many companies are seeking to make operations more efficient, and the concept is especially attractive to older manufacturing facilities looking to improve the bottom line by reducing their costs.

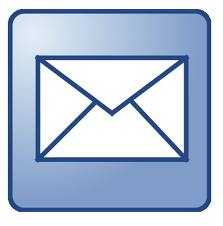





No comments:
Post a Comment