The goals of
continuous improvement are simple: 1) make things easier 2) better 3) faster
and 4) cheaper. Kaizen is the ongoing, systematic, incremental improvement in
the way things are done. It is a relentless attempt to eliminate the
unnecessary activities, delay, waste, and variation of business processes that
add cost without adding value.
Kaizen is a
mindset and practice that encourage reflection, teamwork, standardization,
mastery of the process, experimentation to find better ways, comparison to
baseline accomplishments, incremental and ever-evolving change, and the ongoing
improvement of results. It asks the simple question, “How can I do this
better?”
If you’re in a
leadership position, here are some tips I’ve used and found success with over
the years that can make your kaizens more effective:
1. Empower Your
Employees
Employees who
are closest to the problems on your shop floor are the best-equipped to solve
them. They are your greatest assets in your kaizen efforts, so give them the
support they need to implement improvements. Developing your team’s abilities
through training and support should be as much a part of your continuous
improvement program as making improvements to manufacturing processes.
Additionally,
engaging team members to identify problems and suggest improvements in their
work areas encourages a sense of ownership over their work, which can improve
overall motivation, morale, and productivity.
2. Make Changes
Happen
Kaizen is not “brainstorming”
but it is “trystorming”. Changes have to be implemented. People get used to
ways they perform work. It is necessary to convince them that new methods will
be better. Increase their motivation, involve them into process of changes,
allow "trystorming" (enable workers to try new ways without
consequences).
Remember to use
your wits, instead of reaching for your wallet – and try to think outside the
box! Often, a bit of innovative thinking can go a long way and doesn’t require
additional investments.
3. Focus on Small
Changes
Approach change
in small, incremental steps; if you improve by just 1% every day for a year,
you’ll be 37 times better than when you started. Test and implement small
changes. This increases the speed to improvement and reduces the pressures and
risks of implementing a major change.
To this end,
focus your improvements on solving the root causes of issues. This allows
employees to catch and contain small issues before they become larger and
costlier to eliminate, and it prevents the same problems from reoccurring.
4. Document Your
Process and Performance Before and After Improvements Have Been Implemented.
In kaizen, it’s
important to “speak with data and manage with facts.” In order to evaluate
improvements objectively, existing procedures must be standardized and
documented. Mapping the process’s initial state can help you identify wastes
and areas for improvement and provide a benchmark for improvement.
Measuring
performance against existing benchmarks allows you to demonstrate gains from
your kaizen efforts and keep the company aligned around improvement. It also
allows you to identify areas where your efforts are working–or not–so you can
make strategic decisions about future improvements.
In order to
measure performance objectively, you should identify metrics that quantify
improvements. These may include metrics revolving around quality, cost,
resource utilization, customer satisfaction, space utilization, staff
efficiency, and other KPIs.
5. Enforce Improvements
It’s easy for
employees to regress to their old ways. Enforcing the changes you’ve made to
your processes is important for the improvements you’ve made to last, and it’s
key to sustaining continuous improvement in the long term.
In order for
improvements to last, they must be standardized and repeatable. Standardizing
work is crucial to kaizen because it creates a baseline for improvement. When
you make improvements to a process, it’s essential to document the new standard
work in order to sustain the improvements and create a new baseline. Standard
work also reduces variability in processes and promotes discipline, which is
essential for continuous improvement efforts to take root.
Successful
kaizen efforts can result in benefits such as increased productivity, improved
quality, better safety, lower costs, and improved customer satisfaction. Kaizen
can also lead to benefits in a company’s culture, including improved
communication among employees, improved morale and employee satisfaction, and
an increased sense of ownership in the company among employees.

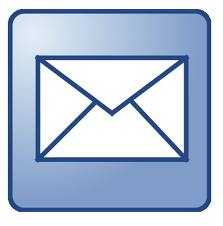





No comments:
Post a Comment