It has been
said that the farther removed a leader becomes from the place where the work
gets done, the less effective he/she will be in supporting those who do the
work. And while that statement may be largely accurate, it’s also true that all
operational leaders, but particularly department leaders and above, are pulled
in many different directions during a given day, week, or month and may not
feel that they have time to spend out in the operation where the products are
made or the services rendered.
Additionally,
some leaders, particularly those that didn’t start out working in operational
roles, may not know how to productively spend time in the operation. Where
should they go? What should they observe? Who should they talk to?
A “Gemba” Walk
is a structured approach to getting leaders out of their offices and into the
places where the critical work of the healthcare facility takes place to engage
with the operation in a meaningful way and to look for signs of waste and
inefficiency or other opportunities to improve. “Gemba” is a Japanese term that
means “the real place”, “the actual place”, or “the place where value is
created.”
Perhaps the
best way to understand Gemba walks is to clarify what they are not. A Gemba
walk is not a random, unplanned visit to “check up” on the workforce or catch
employees being unproductive. It is also not the equivalent of a department meeting
whereby leadership pull staff together to deliver a series of messages.
Instead, a Gemba walk is a pre-planned and structured visit to a particular
area or areas to better understand some aspect of the operation, dialogue with
staff, and/or learn something that the leader can take back to his/her job.
Along the way, the leader should be role modeling the behaviors that he/she
expects from the broader workforce by identifying potential patient or employee
safety hazards and other signs of waste or inefficiency to be addressed (e.g.,
disorganized work area, inefficient business processes, etc.).
The most
effective Gemba walks are planned in advance and entered into with a particular
objective in mind (e.g., teach something, learn something, role model a
behavior, build a relationship, etc.). Contrary to popular opinion, the
workforce will come to appreciate the presence of leadership in their place of
work because it sends the signal that leaders want to understand the challenges
they face every day and opens up opportunities for a constructive dialogue.
Nothing
sustains itself, certainly not Lean manufacturing or Lean management. So,
establish and stick to a routine including regular visits to the Gemba, check
the status of visual controls, follow-up on daily accountability assignments,
and ask the three simple questions everywhere. Gemba walks are really the check
in our PDCA methodology of continuous improvement.

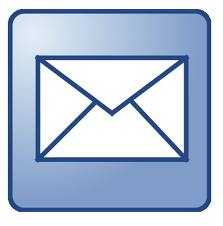





No comments:
Post a Comment