An essential
element in Lean thinking is Kaizen.
Kaizen is the Japanese word for continuous improvement or change for the
better. It’s a tool to make work easier, safer, and more productive by studying
a process, identifying waste, and applying small incremental improvements that
ensure the highest quality. As no process can ever be declared perfect, there
is always room for improvement. Kaizen
involves building on gains by continuing experimentation and innovation.
1. Find Problem.
First look at your business and find an opportunity for improvement. Start by
analyzing the productivity of each department within the company. Look for
departments that struggle with missed deadlines, inferior quality or production
bottlenecks. Once you decide on a department, try to find specific processes
where small improvements can add the most value. Start out with something small
that can be changed easily.
2. Find a
Sponsor. Executive leaders aren’t always directly involved in the Kaizen event,
but they should be enthusiastic supporters who understand the process and
objectives. Their support is important because it makes it more likely that
employees will fully engage. Leaders are often involved in removing roadblocks
and providing necessary resources for the event.
3. Pick a
Leader. Appoint a team
leader to manage the Kaizen event. You
should ensure that your team leader is positive about creating change and is
fully aware of the business case for making improvements, a team leader that is
unconvinced or feels threatened can restrict the improvements being made.
4. Select Your
Team. Typically, team members should comprise of people that work within the
area in which the event takes place plus various people from other support
areas such as maintenance, administration, sales, etc. It may also be worth
adding a few people from the next area in which a kaizen event is planned so
that they have some experience for the next event.
5. Create a Charter.
Clearly define goals and expectations of the Kaizen event. The main focus of
the event should be an area or process in which it has been determined that an
inefficiency is reducing value to the customer. The focus can be narrowed by
analyzing KPIs, root causes, and other Lean metrics. Keep in mind that the end
goal is to promote continuous improvement and reduce waste.
6. Perform
Training. If your team has had lots of practice with Kaizen events, pre-event
training might not be necessary. Otherwise, it is essential to take the time to
provide guidance on what to expect during a Kaizen event and which improvement
tools will be used. The team should be training on your improvement management
technology and know how it will be used before, during, and after the event to
support the effort and capture the knowledge generated. Everyone should be
clear about their role and know how their performance will be measured.
7. Understand
the Situation. Start by analyzing the productivity of each department within
the company. Look for departments that struggle with missed deadlines, inferior
quality or production bottlenecks. Once you decide on a department, try to find
specific processes where small improvements can add the most value.
8. Implement
Solutions. Now that you have figured out the problem it is time to analyze it.
Try to figure out what different options you have available to solve this
problem. Once you have figured out what solutions are available, decide which
one is going to be the best for your particular situation. Then start putting
your solution into action.
9. Check Your
Improvement. Once the event is complete and the desired improvements are in
place, it is essential to make a follow-up plan to measure results and ensure
the improvement is sustained. Make sure that you monitor the progress of the
improvements being implemented and review whether the implementations are truly
improvements. You may find
that additional adjustments to new processes are necessary or that some of the
changes have not been fully applied
10. Repeat. Kaizen
doesn’t stop when you’ve successfully completed your Kaizen event. You should
see this Kaizen event as just in an ongoing series of efforts and improvements.
The true spirit of Kaizen is in “continuous improvement” and “slow and gradual
change”.
Kaizen keeps
you reaching, stretching to outdo yesterday. The continuous improvements may
come bit by bit. But, enough of these small, incremental gains will eventually
add up to a significant, valuable competitive advantage. Also, if every
employee constantly keeps an eye out for improvements, major innovations are
likely to occur. Higher levels sometimes lose perception of what’s going on in
the “trenches” because they aren’t in them every day. Good companies realize
that and encourage feedback from staff. The spirit of Kaizen can trigger
dramatic breakthroughs, whether it be redesigning a simple form or developing
new company protocols.

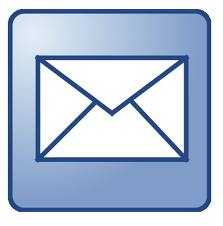





No comments:
Post a Comment