Kaizen is a
Lean manufacturing tool that improves quality, productivity, safety, and
workplace culture. Kaizen focuses on applying small, daily changes that result
in major improvements over time. Although improvements under Kaizen are small
and incremental, the process brings about dramatic results over time.
Beyond the
obvious benefit of improving processes, holding a Kaizen event can foster
problem-solving, collaboration, and communication skills and allow employees to
demonstrate leadership. Engaging team members to identify problems and suggest
improvements in their work areas encourages a sense of ownership over their work,
which can improve overall motivation, morale, and productivity. Finally,
holding a Kaizen event is one way to reinforce a robust culture of continuous
improvement within your organization, after all, the best way to sustain the
principles that you want to guide your company is to put them into practice.
If you are
considering implementing Kaizen methodologies, you are undoubtedly curious
about what the Kaizen benefits may be. The following are some of the most
significant benefits that you will see using Kaizen in your facility:
Kaizen
simplifies the job. By having employees, management, and other important
stakeholders constantly suggesting improvements, it simplifies everyone’s jobs
– improvements should streamline all processes.
Kaizen changes
things up. Do you like doing the same old same old every day? If not, Kaizen is
a great way to keep you on your toes and remove the boring tasks from the
radar.
Kaizen keeps
things from being a total pain in your rear. If something’s not working, why
continue to do it? Instead, it is far better to suggest improvements to solve
problems before costly defects occur. Kaizen keeps your work from becoming a
huge burden.
Kaizen improves
job safety records. By constantly improving processes, you will be abreast of
important new safety standards, the latest in advances in equipment and
technology, and the safest way to do things.
Kaizen improves
everyone’s productivity. If you eliminate wasteful tasks, then you save time.
For example, is it necessary to create a report of reports every month? Are
there less wasteful ways to do things? Is everyone making the best use of their
time? Look into the answers to these questions to meet this Kaizen process
goal.
Kaizen improves
the quality of your products. By following the Kaizen process steps, you can
improve product quality. It is important to have quality products because this
will increase your customer base, and ultimately, it will increase your bottom
line.
Kaizen saves
you money and it saves you valuable time. By having high quality products, few
accidents, few burdons, and highly productive employees, you will save time.
When you save time, you save money. It’s a win-win situation, all around.
As you can see,
there are many great Kaizen benefits that you will enjoy when implementing
Kaizen in your facility. One of the biggest perks of Kaizen, however, is that
the benefits never really end. Kaizen by its very nature is an ongoing strategy
that is always looking for ways to improve your facility.
The initial
benefits that are implemented will lead to further improvement opportunities
down the road. When done properly, Kaizen just keeps going through the cycle of
identifying improvement opportunities, coming up with solutions to those
opportunities, implementing the solutions and finally testing them. If the
solutions are positive, the cycle starts over with new improvement
opportunities. This will continue forever, leading to an optimized facility
that is never satisfied with the status quo.

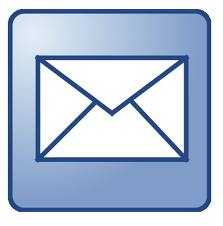





No comments:
Post a Comment