If you currently hold a management position or oversee multiple divisions of employees within a company, you may find yourself constantly looking for new ways to be more efficient in order to optimize your time and efforts. As “Lean” manufacturing describes, companies should always be engaged in a relentless pursuit to improve current operational and production processes. Finding new ways within the office, as well as external implementations that can improve output and employee morale can go a long way. Regardless of the industry you work in, the size of the business, or the current organizational structure of the company, workforce optimization can be reached.
Whether it is something as simple as
productivity or operational day-to-day changes, or the adaptation of a new
technology that can make processes less complex, there are answers to your
current output challenges. Here are some great options you can use to not only
make management easier but align the entirety of the business more closely with
the Lean system.
Uncover Any and All Inefficiencies
Although some lag and waste are expected in any business, large or
small, there are several places within the operations process that a manager
can find ways to cut back or save time. It may be as simple as a lack of
optimal communications and knowledge transfer between departments. However,
more complicated problems could consist of machine error, inconsistencies in
supply chain management, or misallocation of company resources. No matter how
big or small, these issues fall back on to the executive and managerial teams.
Find and record all inefficiencies that could be fixed before making any
decisions that could improve workflow.
Save Money On Hardware
One way companies are saving money is by
eliminating the need to buy certain hardware such as laptops and company mobile
phones by adopting “Bring Your Own Device” or BYOD policies. Having employees
supply their own devices while only having to incur the expense of the wireless
network connectivity would save thousands of dollars each year. These funds can
be allocated elsewhere to fix production issues, buy new software, or upgrade
other equipment for a more efficient process. All of these examples can make
Lean manufacturing possible within almost all business models.
Improve Communication Within and Between Departments
Trying to improve the cross-departmental
insufficiencies of a business can be a difficult challenge. But taking the time
to re-evaluate and rearrange the way interactions occur within departments, as
well as the business as a whole, can seriously impact the bottom line. Poor
communication can prevent progress in operations and productivity, while at the
same time cause a hostile and adversarial environment which hinders
collaboration. Picking the right employees to lead each focus area of the
business is crucial, along with aligning experienced individuals to work
beneath them to ensure that all communication can flow down the
chain-of-command effectively. Employee development will surely become a
higher focal point if they are coached correctly and inspired to do their best
work. Team cohesion can mean the difference between minimal and significant
lag. Without it, the concept of Lean manufacturing is rendered useless.
Consider Automating Certain Practices
Adopting automation software to certain aspects
of the business can save time, money and hassle for management. This automated
programming has the ability to do a variety of things, from assisting in
inventory management to simplifying order processing. This can also help cut
back on waste by expediting several different product development and product
assembly tasks. Robotic process automation has become a
standard for large, diverse companies with a variety of different departments
and an array of processes to make back-end tasks simple. Consider the
advantages of automating your business can have both financially and
strategically.
Implement Employee Recognition Programs
Exploring options like employee recognition
programs may be extremely beneficial for not only company morale, but overall
productivity as well. Although it’s difficult to measure the ROI on these
programs, showing gratitude toward your staff for their good deeds and
accomplishments will keep their work ethic at a consistently high rate while
simultaneously incorporating friendly competition into the workspace. If your
employees know what they are working toward in terms of personal
accomplishment, they will feel a sense of urgency and pride in their work.
While at the same time, the business will benefit in the long-run through
sustained teamwork among divisions and consistency in
meeting company-wide quarterly, and annual goals. Cash bonuses, additional
vacation time, and employee of the month awards are all great ways to keep your
business in the black.
About the Author: Chandler Coleman is a contributing author focused on the tech sector and discusses topics such as business-related software and automation processes.

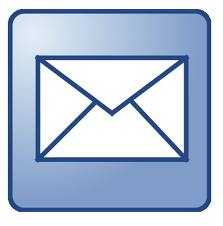





No comments:
Post a Comment