![]() |
Learn more about NE Lean Conference below |
In today’s
active world we are hearing more about getting employees within the
organization engaged at work. This is not only for the leadership team, but
also for the hourly workforce.
For the sake of
this discussion let’s define engaged employees as those that work with passion
and feel a profound connection with their company. These individuals drive
innovation, continuous improvement, and move the organization forward each and
every day.
Why is having
an engaged workforce so important? Gallup reported in their 2013 “State of the
American Workforce Survey” the following key statistics:
Organizations
with an average of 9.3 engaged workers for every actively disengaged employee
in 2010-2011 experienced 147% higher earnings per share (EPS) compared with
their competition in 2011-2012.
In contrast,
those with an average of 2.6 engaged employees for every actively disengaged
employee experienced 2% lower EPS compared with their competition during that
same period.
Gallup
estimates that active disengagement costs the U.S. $450 billion to $550 billion
per year.
Work units in
the top 25% of Gallup’s database have significantly higher productivity,
profitability, and customer ratings, less turnover and absenteeism, and fewer
safety incidents than those in the bottom 25%.
While there are
many things that affect employee engagement, getting leadership to the place
where work is done (the “GEMBA”) and actively engaging with the workforce,
seeing with their own eyes the problems that occur, listening to associates and
giving advice and direction (coaching) to the team is a critical factor in
increasing overall engagement.
Lean
organizations make use of Daily Management systems, a structured process to
focus employee’s actions to continuously improve their day-to-day work. Daily
Management empowers employees to identify potential process concerns, recommend
potential solutions, and learn by implementing process changes. Daily
Management, if done right, can be a critical tool in any organization’s toolbox
to engage frontline staff in problem-solving and to deliver customer value.
Lean Daily
Management includes three components: (1) alignment of goals and effort; (2)
visual data management, daily huddles, and problem-solving; and (3) leader
standard work.
Alignment of
Goals and Efforts
When we
launched our Daily Management program, we noticed that frontline staff often
were not aware of the goals and targets set by senior leaders. Therefore, we
emphasized the cascading nature of system goals and the importance of alignment
between system and hospital goals during training.
Our goals fall
under the pillars of Safety, Quality, Delivery, Cost, and People/Culture, Each
department utilizing Daily Management set its own goals and targets in each of
these pillars in alignment with system and facility goals. We found this
exercise of aligned goal-setting to be incredibly valuable in that it not only
improved awareness of goals among frontline staff, but it also helped them to
see how their work contributes to the success of the system.
Visual Data
Management, Daily Huddles, and Problem-Solving
Visual data
management: Each department utilizes a visual board to display its goals,
targets, and performance metrics. The look and feel of the visual board is
standard across our system, with each board including the standard pillars
mentioned above as well as a designated space for discussion and prioritization
of improvement ideas. The visual board in each department is located in an
accessible area in the Gemba so that the data and metrics stay in front of
everyone.
Daily huddles:
Daily huddles take place at the department level and last for about 10 to 15
minutes. Huddles are led by the staff and are attended by all members of the department
Huddles take place directly in front of the visual board so that the metrics
that are displayed on the board can be discussed and updated as needed.
Problem-solving:
A unique aspect of our problem-solving process is the systematic feedback loop
from senior leaders back to the department. We recognize that staff cannot
implement all solutions or process improvement ideas alone and that process
changes often involve other departments or functions. For this reason, part of
the daily huddle is dedicated to problem-solving. This portion of the huddle
includes a review of improvement ideas submitted by staff, a progress update on
ideas that have been selected for implementation, and feedback received from senior
leaders on ideas that have been submitted to senior levels for implementation
and/or resourcing. Accountability is achieved through review of progress on
implemented ideas with use of a simple WWW (What, Who, and When) form. This
process of problem-solving (idea generation), reviewing progress, and providing
feedback is key to sustaining team engagement.
Leader Standard
Work
The third
component of our program relates to the role of leadership. For the Daily
Management program to be successful, it is critical for leaders at all levels
of the organization to be committed to
the program and visibly present at huddles. The role of these leaders at
huddles is to encourage teamwork and collaboration, help remove barriers,
mentor and coach frontline staff (who often do not have enough exposure to the
big picture), and foster systems thinking (that is, an understanding of the
interactions between the work and processes from one team to another).
Lean Daily
Management is a powerful and peerless method for engagement. The technical
approach is simple enough to understand. But it is not a “plug and play”
technique. To make it work requires a level of leadership understanding and
commitment that is often missing. If you approach daily management as a
stand-alone installation for the workers, it will fail. Daily Management, if
done right, can be a critical tool in any organization’s toolbox to engage
frontline staff in problem-solving and in bringing value for customers,
employees, and the organization.
Note: If you would like to learn more consider attending the Northeast Lean Conference October 22-23, 2019 in Hartford, CT where I will be presenting about this topic.

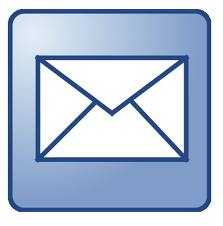





No comments:
Post a Comment