Lean thinking
is fundamentally transforming the way organizations operate. The Lean
principles of continuous improvement, respect for people, and a relentless
focus on delivering customer value are making teams and organizations rethink
the practices that might have guided them for decades. A new, transformative
approach to working requires a transformation in leadership, as well. For Lean
to be truly effective, it needs effective Lean management — to champion Lean
principles, offer guidance, and ensure that Lean is being used to optimize the
entire organizational system for value delivery.
In a lean
organization changes occur in all processes at all the areas of the
institution. Therefore, lean leadership is required at all levels to ensure
overall success. From the CEO to plant managers to supervisors and unit
leaders, every leader has an essential role to play in sustaining the lean
program. Ultimately, they have find ways to drive continuous change and
maintain momentum from year to year. There is really no sure-fire approach to
achieve this, but there are specific actions and behaviors which leaders at all
levels can take, to sustain a lean initiative and ensure the program continues
delivering long-term results and benefits to the organization.
Because lean
demands continuous innovation and new processes, leadership in a lean
organization is constantly faced with unique problems as they strive to sustain
continuous-improvement. Therefore, to improve their effectiveness and hence
meet some of these challenges, lean leaders incorporate the following
principles in their personal leadership style.
1.
Self-Knowledge
True
self-knowledge leads to humility. The mark of a good lean leader is the ability
to reflect and acknowledge their own weaknesses, seek improvement, learn
constantly; and to give and receive challenges.
Before a leader
can effectively lead a team and seize control of an institution, he or she
needs to ‘know' themselves first. Far too many people lack a true understanding
of their own capabilities - most underestimate their weaknesses, while
overestimating their talents. As a result, they often make bad decisions about
what they can handle on their own and where they should seek assistance from
others. The trappings of power, titles and privilege can also fool one into
pride, or the false belief that one is more qualified, smarter, or more
experienced than those they are leading.
To effectively
improve their leadership, lean leaders use some method to gain insight into
their performance other than personal perception. This may involve completing a
proficiency test in their field, taking an IQ test, or requesting their team to
fill out an anonymous survey about themselves. The idea is to get a wholesome
and objective feedback about oneself, and though it's an uncomfortable process,
it's always well worth the effort.
2. Be Open to Change
To efficiently
and effectively drive change in a lean organization, a lean leader must be open
to change. This basically means being open to new ideas including those which
they do not like, support, or claim ownership to. They should also constantly
challenge assumptions and ideas, especially their own; and need be open to
being wrong as well as willing to mend their ways.
3. Lead by
Example
A lean leader
sets the example for others to follow. He or she must be an excellent role
model by following what they teach and ask of others. For instance, if a leader expects team
members to complete standard work and show proof of this, then he or she should
also complete their leader standard work and provide proof of it for all to
see.
To lead by
example, a leader needs to act with highest integrity and be genuine. Also,
their actions and decisions must at all times be aligned with and supportive of
the organization's principles and mission. As a leader your actions should echo
your words whenever possible – so practice what you preach.
4. Be
Respectful
Every single
person in the organization deserves to be treated with respect and dignity.
Lean leaders treat all people - especially their direct reports - as human
beings who know how to think, come up with creative solutions, and solve
problems. When employees and other stakeholders are treated with respect, only
then can they be enabled to learn, think, and improve.
Leadership is
about being a servant to the people who report to you, and supplying them with
the resources they require to serve customers and abide by the company's
principles. It's all about trusting, teaching, and allowing failures which
impart important lessons.
5. Go to the
Gemba
A lean leader
must go to the gemba as often as possible. They must be present on the job site
on a regular basis, actively engaging with the people closest to the customer-
rather than spending most of their time in the office or conference rooms.
This, as a result, ensures that they are able to truly understand the real
situation, allowing them to take effective actions to improve performance.
A true lean
leader frequents the workplace both when things are going well, and when
problem arise - otherwise, employees are less likely to communicate the real
situation if their boss only shows up when problems occur.
6. Develop a
Culture of Continuous Improvement
True lean
leadership fosters continuous improvement even when the ideas for improvement
do not measure up to expectations. A lean leader empowers their workers to take
on the responsibility for resolving their own problems, by making it acceptable
to attempt something even if it does not work out. It's essential to
demonstrate that participating in improvement activities, challenging existing
practices, and observing processes, are all part of a complete problem solving
approach that will advance the organization.
Leaders play an
integral role in motivating and influencing employees to adopt a continuous
improvement mindset. If the leader does not demonstrate the behaviors and
mindset required for successful lean implementation then they cannot expect
their employees to.
When leaders
are true role models for Lean behavior, this inspires everyone within an
organization to deepen their understanding of Lean, fully engage with a
transformational program, and close the gap between Lean tools and Lean
thinking to fully realize the value of Lean.

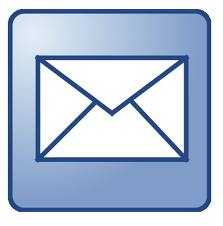





No comments:
Post a Comment