In recent
years, several training simulation games have been developed by academic and
industry experts to support the teaching and learning activities of Lean
philosophy. Using simulation games to teach Lean philosophy is an effective
tool to convey the concepts.
Games use
multiple communication means and create engagement. More importantly, they help
people to memorize concepts and allow for a more practical experience of lean
than traditional teaching methods do. They give participants a chance to
practice lean in a risk-free and fun environment, and work in all cultures and
at all management levels.
Teaching lean
thinking this way is a commonly recognized approach in our community. There are
numerous lean games out there – free or requiring payment, physical or online.
(Martin Boersema provides a 50-strong list of lean games and simulations here.)
Here are five lean
games that every company can benefit from.
Numbers Game –
5S, Place for Everything and Everything in it’s Place
5S is a Lean Methodology using a 5 step approach to achieve and maintain a high level of workplace organization. The 5S Numbers Game is designed to illustrate how valuable 5S can be to your business. This is a no cost exercise that can be done in any setting for any level within your organization. In this exercise you will experience how a disorganized work place can negatively affect productivity and quality.
5S is a Lean Methodology using a 5 step approach to achieve and maintain a high level of workplace organization. The 5S Numbers Game is designed to illustrate how valuable 5S can be to your business. This is a no cost exercise that can be done in any setting for any level within your organization. In this exercise you will experience how a disorganized work place can negatively affect productivity and quality.
If you type the
5S numbers game into any search engine on the internet you will likely come up
with a number of good hits. The folks at SuperTeams, a Lean Six Sigma
training firm have put the 5S numbers
game on their web site. They have included a simple facilitators
guide to make it easy for anyone to start teach this exercise right
away.
Standard Work
is a foundation of Lean. This fun exercise was originally created by the
Minnesota Office of Continuous Improvement as a great way to illustrate the
value of Standard Work. Each participant is given a grid and written
instructions, or the instructions can be read out to the group. The goal is for
everyone to come up with the same drawing at the end based on the instructions.
And it's a pig!!
This activity
is simple, no cost, and great for everyone. I often use this activity as a
teambuilding exercise to kick-off teaching elements of standard work. Paul Levy, former President
and CEO of Beth Israel Deaconess Medical Center in Boston put a
simple explanation of this exercise on his blog. Round 1 starts
with the audience drawing the side profile of a pig. In round 2 you
give standard work instructions to the audience to draw the pig. The final round has
the audience draws the pig with standard work instructions with visual template
for comparison. Everyone will find it easier to draw the pig in the final
round. You’ll also find that all the pigs in the audience look that same at the
end.
This is a simple exercise but it teaches a powerful Lean lesson of team work, direct involvement, and continuous improvement. It involves passing tennis balls within a group where the goal is to perform this action as quickly as possible.
Ralph Bernstein
at the Lean Insider posted
on the
tennis ball exercise with several photos from an event.
Robert Forder
loaded a detailed explanation of the exercise
in power point on the lean
in education forum at LEI.
The Tennis Ball
Exercise is a simple, low cost exercise that can be used to teach any one no
matter education, language, or culture. It will break the ice, help teams form,
and get people involved while teaching the “we can” attitude that so necessary
in continuous improvement.
Reducing the
batch size in manufacturing is a desirable goal: it improves the speed of
response to the customer, while improving the ratio of value-added to non
value-added work.
In the
book Lean
Thinking, James Womack and Daniel Jones recount a story of stuffing
newsletters into envelopes with the assistance of one of the author’s two young
children. Every envelope had to be addressed, stamped, filled with a letter,
and sealed. The daughters, age six and nine, knew how they should go about
completing the project: “Daddy, first you should fold all of the newsletters.
Then you should attach the seal. Then you should put on the stamps.” Their
father wanted to do it the counter-intuitive way: complete
each envelope one at a time. They told him “that wouldn’t be efficient!”
So he and his daughters each took half the envelopes and competed to see who
would finish first.
The father won the race, and not just because he is an adult.
The father won the race, and not just because he is an adult.
Red Bead
Game
In 1982, Dr. Deming created a teaching tool that he used in his seminars around the world to teach his famous 14 Obligations of Management. Dr. Deming called this training tool, The RED BEAD Experiment or Red bead Game.
When you play
the game, each player uses a special metal paddle to draw small red and white
colored beads from a large bowl. Each draw of the paddle gets 50 beads. Some
are white and some are red. The white beads symbolize the good things that we
experience each day as we do our work and the red beads symbolize the problems
or bad things that we experience. As each player draws their paddle full of 50
beads each player receives a different mix of red and white beads.
The red bead
experiment is deceptively simple because it provides a powerful message that is
difficult for many to grasp. In summary, the misconception that workers can be
meaningfully ranked is based on two faulty assumptions. The first assumption is
that each worker can control his or her performance. Deming estimated that 94
percent of the variation in any system is attributable to the system, not to
the people working in the system. The second assumption is that any system
variation will be equally distributed across workers. Deming taught that there
is no basis for this assumption in real life experiences. The source of the
confusion comes from statistical (probability) theory where random numbers are
used to obtain samples from a known population. When random numbers are used in
an experiment, there is only one source of variation, so the randomness tends
to be equally distributed. However, in real life experiences, there are many
identifiable causes of variation, as well as a great many others that are
unknown.
Mark Graban uses this game to illustrate
process variation and learning what the data tells you in his book Measures of Success and
associated workshops.
There are several
resources online where you can purchase a Red Bead Kit.
Indeed, as lean
coaches, we must always look for new ways to improve the learning experience,
and I have personally found that using games and simulations works quite well.
Note: Ron Pereira at the Gemba Academy has put together a number of videos with these exercises.
5S NUMBERS GAME | |5S Workplace Productivity
Watch This One Piece Flow vs. Mass Production Envelope Stuffing Lean Thinking Simulation
Lean Tennis Ball Simulation with Practical Problem Solving & Quick Changeover
5S NUMBERS GAME | |5S Workplace Productivity
Watch This One Piece Flow vs. Mass Production Envelope Stuffing Lean Thinking Simulation
Lean Tennis Ball Simulation with Practical Problem Solving & Quick Changeover

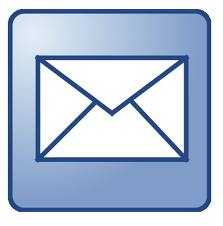





No comments:
Post a Comment