Click this link for A Lean Journey's Facebook Page Notes Feed.
Here is the next addition of tips from the Facebook page:
Lean Tip #2551 – Communicate Openly
Employees often have a hard time dealing with
change in the workplace due to fear regarding its impact on their
responsibilities, pay, benefits, and other important aspects to one’s career.
Open – and proactive – communication can help alleviate this. Remember: Always
tell employees what you know, what you don’t know, and what you’re working on
figuring out. They’ll appreciate the honesty and it’ll help keep the rumor mill
at bay.
Lean Tip #2552 – Listen Carefully
Chances are your employees have several
concerns that have yet to be addressed, and this is true no matter how
thoroughly and how often you communicate with them. Set aside part of your day
to listen to their concerns and questions, and address them as openly and
respectfully as possible. It’s okay if you don’t know the answer yet, let them
know you are working on it and will get back to them.
Lean Tip #2553 – Prioritize People Over
Processes
Having processes in place can help you deal
with change, just as certain mathematical equations can be used to help
mathematicians solve unique problems. But ultimately, an equation can only do
so much. The same is true of business processes. You can have processes in
place to handle unique challenges, but it’s the people behind these processes
that matter most.
When confronted with change, a computer program
or piece of software is only going to do so much for you. You really need to
have strong relationships with people you can trust. Together, you can use your
collective knowledge, experience, and creativity to tackle these new issues.
Prioritize people over processes and you’ll be better off almost every time.
Lean Tip #2554 – Get Over the Pursuit of
Perfection
How many mistakes do you think you make on a
daily basis? Five? Ten? Fifteen? Between little things and big
responsibilities, we’re all making a handful of mistakes on a daily basis.
According to research, the average person will make 773,618 decisions in a
lifetime. Of those decisions, 143,262 – or nearly 20 percent – will be regrets.
In other words, you aren’t going to be perfect – not even for a day.
The sooner you get over the notion that you can
or should be perfect, change will come easier. You’ll put less pressure on
yourself and be more willing to confront the challenges and decisions that
await you.
Lean Tip #2555 – Know Your Limits
You’re human and can’t be perfect. Once you
realize this, you’re free to confront the fact that you have limitations.
Recognizing your limits isn’t a sign of weakness. Instead, it’s a sign of
self-awareness. When you know what you can and can’t do, you’re able to hand
off certain responsibilities and processes to other people who are better
prepared to handle a specific element of change. It can be humbling to do this,
but it’s usually what’s best for the company.
Lean Tip #2556 – Share
More, Not Less.
Even in a small company, silos emerge. A policy
of more sharing will help everyone stay in touch with what others are doing,
and create a collective expectation. Keeping everyone pointed in the same
direction is hard; sharing more about what’s going on, how you’re doing things,
reasoning behind decisions, etc. will help.
Lean Tip #2557 – Don’t Automatically Blame the Tool.
It’s not the hammer’s fault if the person
swinging it uses the wrong end. It just won’t work well. Most tools are decent
enough, they’re just used incorrectly. Rushing to change a tool because things
aren’t working well may be a mistake.
Lean Tip #2558 – Focus on Gradual Small Changes
Instead of Major Shifts
Focus on small gradual changes rather than
large changes. Small changes can be made quickly, on a daily-basis, and are
typically inexpensive. By focusing on small changes, you can remove barriers
from just starting a continuous improvement process. This focus will allow your
team to reap the benefits of their “small wins” right away. As more and more
small changes are applied, your team will see an accumulation of benefits from
them. This will give them more confidence to suggest more ideas.
Lean Tip #2559 – Prioritize Ideas that are Inexpensive
By going after the ideas that do not require a
large amount of investment, you can remove the financial barriers of your
continuous improvement efforts. This process can empower the line worker to
suggest and implement ideas that can improve their working process because they
know that their changes do not need upper management approval. Some ideas such
as reducing waste, eliminating unnecessary steps, and re-organizing in the work
processes fall into this category.
Lean Tip #2560 – Gather Ideas From the People Doing
the Work
In a Lean and continuous improvement
organization employees are your greatest asset and should also be the source of
generating new ideas for improvement. No one knows the work better than the
person who performs it everyday. No one has more “skin in the game” about the
working process than that person. As a result, the best person to suggest ideas
for improvement and to implement them is the line worker.
Lean Tip #2561 – Empower Employees for Improvement
Although employees play a vital part in the
continuous improvement process, it is management’s role to train and empower
them. Most workers are unaware of Lean principles and practices such as 5S, the
8 wastes, value stream mapping, visual management, Kaizen, etc. As a result,
they may not realize that many of the processes that they perform everyday and
the frustration that they feel at work are due to unnecessary waste.
Additionally some workers are modest and reluctant to share ideas. It is
management’s role to educate their staff on Lean tools and techniques that can
be applied to the continuous improvement process and to help their employees
overcome any personal or psychological barrier that prevents them from trying
out new ideas.
Lean Tip #2562 – Educate the Workplace.
Like any other business strategy, ongoing
education of the workplace is critical in establishing awareness, developing
skills, and institutionalizing the needed mindset and behaviors to bring about
effective change. It is no different with Continuous Improvement. Expect and
overcome resistance to change with ongoing training, reinforcement of expected
behaviors, and recognition of those who are learning and doing.
Lean Tip #2563 – Ensure a Penalty-Free Exchange
of Ideas.
In many organizations, expressing one's opinion
on how to do things better may not necessarily be a welcomed activity.
Management can feel threatened or pressured to act resulting in immediate
resistances. And, those expressing ideas may be viewed as complainers or
trouble makers. In such an environment, it doesn't take long for the potential
risks of making a suggestion to stifle enthusiasm and participation in
improvement oriented thinking. Ensuring a penalty-free exchange of ideas is
beneficial to both the giver and the receiver of new ideas and approaches and
will ensure a safe two way exchange of thoughts and ideas.
Lean Tip #2564 – Use a Consistent Approach for Projects.
A consistent and structured approach for
project identification and execution will provide the organization with the
ability to identify, select, and manage continuous improvement projects. The
continuous improvement project process should also provide post-closing process
steps to continually refine the improvement project methodology and to act upon
the lessons learn from the project effort.
Lean Tip #2565 – Establish an Enduring Culture.
For continuous improvement to work, there must
be a relentless focus on and commitment to getting things right. Adaptability
and an action oriented leadership team are inherent components of a continuous
improvement culture. Resistance to change exists in all organizations to a
degree and it must be recognized for what it is, an impediment to improvement.

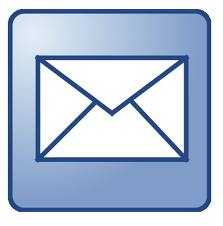




No comments:
Post a Comment