Workplace safety is vital. From medical workers to construction sites, manufacturing jobs to retail, anywhere workers are moving, lifting, walking, or even sitting requires certain safety measures. While organizations like OSHA have specific recommendations for health and safety practices you should be aware of, here are additional ways to help increase workplace safety.
To increase workplace safety, don’t just hand your employees a manual or require they take a one-hour class at the start of their employment. Create a training program with real-world, hands-on examples of the types of situations they’re likely to encounter.
Some general topics to include are eye, respiratory, and face protection, as well as the required personal protective equipment (PPE); safe waste disposal; the proper operation of machinery and equipment; and identifying potential safety risks. Make your training specific to your industry, and make it thorough.
In addition to preventive training, include emergency training. Your employees need to know how to effectively handle crises when they arise. Drill these emergency situations frequently so, when something happens, employees immediately know what to do and are less likely to panic.
Do Make Documentation Available
A handbook is a good start. Collect all safety protocols and requirements in a handbook and ensure your employees know exactly where it is. Also make sure it’s easy to read and organized.
If you’re able, it’s even more convenient to have this information in an online portal or database. That way, employees can access it wherever they are and search for the pertinent information with specific keywords. Having the documentation easily accessible demonstrates to your employees that you value a culture of safety.
Do Reward Safe Behavior
Provide your employees with small incentives when they follow safety procedures. Regularly change the rewards so employees don’t get bored, and make sure the reward process is fair. When employees see their coworkers getting special attention for following the rules, or even going above and beyond them, they’re motivated to join in the practice.
Do Lead by Example
Part of increasing workplace safety is cultivating a culture that values it. It’s not enough to train and reward; you have to lead by example.
As a leader, be confident in your abilities and consistent in following safety procedures. Your employees will see your efforts and mirror you. Regularly challenge the status quo and innovate new ideas to increase safety and to ensure procedures are followed.
Don’ts
Don’t Wait for an Inspection
Don’t wait for an inspection from OSHA to implement required safety protocols. Not only will you be putting your workers in unnecessary danger, but your business may even receive citations or penalties that probably come with fines or other punishments.
Instead, conduct mock inspections throughout the year to ensure your safety practices don’t get flagged. This will help catch small potential problems or habits before they become big ones, saving you time, money, and hassle.
Don’t Punish Feedback
Workers on your front lines are often the first to spot safety issues. However, if they fear retaliation from their coworkers or managers, they may not speak up. Foster an environment where feedback is appreciated and, if necessary, implemented.
Take this a step further by asking employees for their opinions on possible solutions. They feel their feedback is heard and appreciated, and they’ll feel like their input is valued. This increases employee engagement and the likelihood that the behavior will continue.
Don’t Let Mess Accumulate
A messy work environment is a dangerous one. Make sure aisles, especially emergency exits, are clear from all storage and debris. Clean spills immediately, and if chemicals are involved, use the proper waste disposal process. Watch out for tangled cords or other electrical hazards.
Additionally, don’t let clutter cover required safety signage. Whether that’s the OSHA posters, emergency lighting, hazard signs, or exit signs, don’t allow boxes or shelves to block these essential notifications and reminders.
Don’t Ignore Equipment
If your business requires your employees to wear PPE, don’t let glasses, hard hats, gloves, masks, or clothing get worn out or broken. Regularly inspect equipment and replace it at the required intervals, or if it stops functioning correctly.
Also ensure you have enough gear in the correct sizes for your employees. What will fit a five-foot-four-inch tall person isn’t going to work for someone over six feet. Don’t forget to take body sizes and shapes into account as well.
Keep a plentiful supply of your necessary equipment. If your employees work without their PPE, they risk injury, which also puts the business at risk for lost profits or a complaint or lawsuit.
The Cliché is True
Safety first—it’s a cliché but it’s true. When you make safety a priority in your workplace, your employees are happier, more productive, and, of course, safer. You, in turn, have less stress and a better business.
Author Bio: Jordan McDowell is a writer and content strategist with a passion for business and leadership. He specializes in technically-oriented content for a number of industrial manufacturing companies.

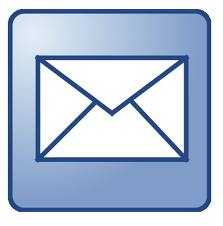





No comments:
Post a Comment