Here is the next addition of tips from the Facebook page:
Lean Tip #2656 – Avoid Making Quick Assumptions.
One of the biggest inhibitors to quality communication in the workplace is missed signals and quickly formed assumptions. If your employee is lagging in an area in which you expected them to excel, don’t immediately assume that they’re a slacker who doesn’t care.
Instead, provide a non-confrontational setting to dig into where the problems lie. When you ask your employee how things are going, you may find out that they are moving and have had a hard time focusing at work, or that they’re not used to juggling six projects at once and need to de-prioritize something. When your ears are open, so are the lines of communication.
Lean Tip #2657 – Learn Each Other’s Strengths and Weaknesses.
There’s more than one way to do this. It might be through observation throughout the months, finding out what your team members are strong at and need a little help with. For example, my boss and I have figured out that she’s great at getting work done in ordered and segmented blocks, whereas I get my best work done in concentrated bursts.
There’s also the personality type route — Enneagram, Myers Briggs, and Strengths Finder are just a few. All of a sudden, it might make sense that you’re motivated by competition and focus, whereas your other teammate does best with input and ideation. By understanding each other’s strengths and weaknesses, it’s easier to have effective communication in the workplace.
Lean Tip #2658 – Be Present and Engaged in Conversation.
You can show you are present and engaged in the conversation by focusing on your coworkers as they speak and by keeping your phone and other distractions put away. Acknowledge your coworker’s statements and respond accordingly. In a face-to-face conversation, you can respond with a smile, nod of the head or polite gesture that illustrates your feelings regarding their statements.
Lean Tip #2659 – Know When Less is More
In a perfect world, people are able to power down after work hours and stop checking their emails. But the truth is, many of us are so connected to our jobs and our devices that not checking seems unnatural. The line between a healthy work-life balance is blurred even further when working from home when we don’t have that physical separation between the office and our living room. After work hours, however, keep the number of emails you send to employees to a minimum. While your communication is likely important, it can also most probably wait until the following day.
According to data collected during the transition to remote work, 32% of employees don’t feel they have a proper balance between work life and personal life. As a manager, it’s your role to lead by example and help them draw clear boundaries.
Lean Tip #2660 – Good Communication Requires Consistent Effort
Most of us know how to communicate with our friends, family and significant others, but why is it so hard to do the same at work?
Often it boils down to creating an environment where people are comfortable enough to express what they’re really thinking, challenge ideas and ask questions that might come across as stupid. Managers need to set an example for their team by demonstrating what it means to be a good communicator. That means practicing good listening skills, giving team members an opportunity to speak, setting clear expectations and providing regular feedback.
Lean Tip #2661 – Employee Recognition: Be Quick
Ideally, recognition should occur as close to performance as possible. This way, the praise reinforces the behavior the employer wants to encourage. If you wait too long—days or even weeks later—the employee has already put their accomplishment behind them and is no longer in that mindset. Immediacy is vital, as it allows the employee to better tie their performance with the praise they’re receiving.
Lean Tip #2662 – Employee Recognition: Be Specific
“Good job” may sound encouraging, but it isn’t enough to foot the bill when it comes to workplace recognition. You must let the employee know what specific behaviors or actions are being rewarded. When you’re too generic, you leave an employee confused about what exactly they did right. When you praise specific items, however (‘closed X number of sales calls’, finished the project X days before the deadline, etc.), you’re offering the employee a blueprint for repeated successes.
Lean Tip #2663 – Employee Recognition: Be Accurate
Nothing’s more embarrassing than not having your facts straight when it’s time to acknowledge an employee. Ensure you know the person’s name and the specific accomplishment for which you’re acknowledging them. Making a mistake in this manner will only serve to leave a sour taste in the employee’s mouth.
Lean Tip #2664 – Employee Recognition: Be fair
As the old adage goes, ‘it takes a village to raise a child.’ While there will certainly be occasions when a star employee stands out above the rest, for the most part, projects tend to be a team effort. Don’t make the mistake of overlooking contributors. Instead, recognize and celebrate unsung heroes who helped behind the scenes.
Lean Tip #2665 – Employee Recognition: Be Well-Balanced
Make sure that the reward you’re offering matches the degree of achievement. For instance, if you’re celebrating an employee’s five year anniversary, don’t simply hand him or her a pen with the company’s logo. This only sends the message that the milestone is insignificant. Likewise, avoid going overboard with recognition. Small tokens of appreciation such as plaques/trophies, gift certificate, or even food are sometimes perfectly sufficient to make an employee feel valued.
Lean Tip #2666 - Employee Recognition: Highlight the Impact
Employees want to feel connected with their organization’s purpose, and the best way to do this is by highlighting the impact their work has. Whether it’s reflected through business metrics, a delighted client, or supported teammates, showing how someone’s efforts contribute to greater objectives makes them feel like an asset. When you’re delivering recognition, always be sure to state why what they’ve done was important.
Lean Tip #2667 - Center Your team Around Shared Values
When team members are all connected by shared core values, it offers a kind of North Star for everything from communication norms to collaboration practices and prioritizing initiatives. This not only contributes to healthy team dynamics and performance, it also serves as a reference point for recognition. If everyone is aligned on what’s important to the team, they can easily point to these values when recognizing the good work and behavior of other team members.
Lean Tip #2668 - Use Recognition to Encourage Desired Behaviors
This tip can be thought of as a combination of the previously two, but is still so important that it needed a heading of its own! Your employee recognition programs should always encourage desired behaviors, whether directly or indirectly.
How? By rewarding these desired behaviors! If you want your salespeople to make more money, then reward them with good compensation plans. If you want to encourage teamwork, then recognize team achievements and reward them with a fun, creative team activity.
Lean Tip #2669 – Invite Peer-to-Peer Recognition.
Create a culture of appreciation by inviting employees to recognize each other for a job well-done or an over-and-above contribution. Peer recognition programs encourage employees to take note of what their colleagues are doing, and build camaraderie and excitement for individual and company successes.
Lean Tip #2670 - Promote Recognition at the Top.
Every great workplace has several ways that senior leaders or partners can recognize teams or individual employees. While a great people manager has several recognition tools at their disposal, and demonstrates the characteristics outlined above, a great workplace has leaders who get in on the action too, demonstrating that senior leadership knows and understands how teams and individual contributors are driving business success.

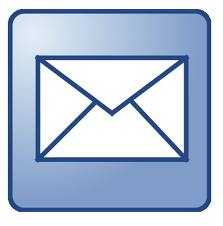




I like tip 2656. Over the summer My boss was so quick to dismiss any solutions to problems he had. He was almost combatting my solutions with reasons why they can't work. He was so quick to assume theat nothing would solve his problem because he "tried everything." what he failed to do was ask the five whys and really diagnose the problem. Together when we went through our data, and laid out a process map, we were able to come up with a strategic plan to reduce time in the warehouse.
ReplyDelete