Here is the next addition of tips from the Facebook page:
Lean Tip #2716 –Communication is the Key for Any Project
To run a project smoothly, consistent effective communication needs to take place between the stakeholders and clients and new changes should be communicated to the team members to avoid ‘surprise attacks’. Being a project manager, the best thing you can do is to ensure that the communication lines between you and the team members are always open so that anyone can walk up to you without any second thoughts.
Ineffective communication often leads to the failure of the projects. So, make sure everyone has the required information to make decisions and proceed with the project. Project status reports are a good way to keep everyone on the same page by keeping them updated about new developments in a project.
Lean Tip #2717 – Tap Into Team Members Strengths and Weaknesses
The success of a project largely depends on skills of the team members. An effective manager will always make an effort to get to know about his team members inherent strengths and weaknesses so that he can allocate work accordingly. As someone’s strength is someone else’s weakness thus an effective manager will make sure the work is given to the team member who is inherently competent and faster at completing it.
Tapping into the strengths of team members will definitely ensure faster task completion and better time management. With everyone in a team putting their best foot forward and making the most of their strengths, the project will be nothing less than a success.
Lean Tip #2718 – Manage Potential Risks
Risk management being one of the imperative project management practices today is essential for project success. Risks are the potential threats that can creep anytime and can jeopardize the whole progress in a project. To make sure your project is successful, potential risks need to be identified beforehand so that effective measures can be taken if they arise in the need of the hour.
With considerable experience and expertise with similar projects, you will be able to foresee when the risk is imminent and when corrective measures need to be taken. After realizing the importance of risk management, many organizations are now paying special attention to it so that it doesn’t come in the way of the success of a project.
Lean Tip #2719 – Evaluate the Project Afterward
Each project can be a learning tool. An effective manager will always review the project as a whole, as well as analyze various project components. By doing so, he can note down the successes in a project, what went wrong in the project, and what can be improved for future projects.
Evaluating every aspect and the nitty-gritties in a project can be resourceful to ensure success for future projects as well.
Lean Tip #2720 – Stay Ahead of Problems.
A wise project manager once told me, "If 'everything's fine,' keep digging." When people report no problems, you can follow up with, "That's great to hear, but, really, there are no issues at all?" Team members may be hesitant to share problems, especially when they're small and still solvable. A project manager's job is to uncover small problems to help solve them or accommodate them instead of letting them grow into bigger problems.
Lean Tip #2721 – Understand the Right Problem
“If I had an hour to solve a problem I’d spend 55 minutes thinking about the problem and 5 minutes thinking about solutions.” – Albert Einstein
I know it sounds very simple and philosophical but believe me; many problems remain unsolved because there has not been a focused effort to really understand the problem itself. I still remember solving math problems when I was young and every time I couldn’t solve a problem I would ask my Dad for help. He would never provide me a solution straight away, but instead ask me to go and read the question again at least three times. I used to feel frustrated, but invariably, half of the time, reading the question properly would lead me to the conclusion that I had actually been trying to solve the wrong problem. The minute you identify the correct intent of the problem, the right solution will follow. So ask yourself the fundamental questions about the problem and spend some time understanding the real problem with your team in order to solve it.
Lean Tip #2722 – Get Out of the “I Know Everything” Mentality
Try and understand the fundamentals of the process pertaining to the problem area. Confirm how it works or exists in its very basic and current form. Get out of the mind-set that you know everything, because if you did, you would know the problem area, cause and its solution as well. Understand the nuances of the techniques which exist in the process. Ask all the basic questions to really understand the problem and note significant points of the process which would then bring immense clarity to the part of the problem you are attempting to solve.
Lean Tip #2723 – Visualize the Problem
Try and document a picture of the process depending on the problem. This may or may not be relevant, but we all know pictorial representations often help. Draw a simple diagram without worrying about technical conventions, specific constraints etc. A simple picture diagram can help visualize the most complex of problems in any area. Use any simple tool like PowerPoint, white boards, sheets, and papers and never shy away from starting to draw these on the fly if understanding a problem is becoming a challenge.
Lean Tip #2724 – Be Simple But Creative in Your
Solution
Building a simple solution does not mean trivializing the problem which you are looking to solve. The majority of the time, complex solutions are devised for a problem if the above points i.e. understanding the right problem, understanding the fundamentals of the problem, articulating the problem and focusing on the root cause, are not considered.
Be creative in your problem solving. This has got nothing to do with how much creative ability you have, it’s basically about thinking of solutions from a different perspective rather than a perspective with which the problem you are looking to solve was built or on how the problem came into existence.
Lean Tip #2725 – Find the Opportunity And/or Lesson Within the Problem.
I have found that there is almost always a positive side to a problem.
Perhaps it alerts us of a great way to improve our business or relationships. Or teaches us how our lives perhaps aren’t as bad as we thought.
Finding this more positive part of the problem reduces its negative emotional impact. You may even start to see the situation as a great opportunity for you.
When you are faced with a problem ask yourself:
- What is the good thing about this?
- What can I learn from this?
- What hidden opportunity can I find within this problem?
Lean Tip #2726 – Make it Clear Collaboration is Expected
It may seem like a no brainer in today’s workplace, but some team members might need a gentle reminder that collaborating is the default setting for the company. Some people may work faster and do their best work alone, and that’s great for when actual work needs to be done. But there are other parts of work where working together is crucial. Set that expectation and people will get behind it.
Lean Tip #2727 – Don’t Use Meetings for Status Updates
A collaborative manager avoids using meetings for status updates. They use meetings to address issues that apply to all attendees, so no one’s time is wasted. Use strict agendas to keep the conversation on point and the pace quick. Again, structured, time-compressed meetings are the most effective.
Lean Tip #2728 – Over-Communicate
Collaboration, at its core, is effective work communication. To clarify, this doesn’t mean we should interrupt each other whenever we have a thought about something. We should still use communication etiquette and boundaries.
But, as we work, team members and managers can rarely trust that information is shared in an effective and timely manner among team members. This issue is so widespread among enterprises that, according to one survey, 57% of project managers cited poor communication as the leading cause of project failure. The solution is better, frequent communication.
Lean Tip #2729 – Don’t Automate Bad Processes
Not everything should be automated. Examine current manual processes to make sure you’re doing it the right way to begin with. Automating a poorly designed process with a work management platform won’t make it easier to work with others, it will only make it worse. The right kind of automation facilitates collaboration by freeing up time to align and brainstorm about critical work.
Lean Tip #2730 – Measure What Matters
The only way to know if what you’re working on
together is working is to focus on the metrics that matter to the efforts
you’re all putting in. Avoid focusing on vanity or busy-work metrics. Focus
instead on milestones or engagement for example.

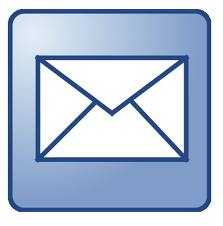




No comments:
Post a Comment