Though there is
no single definition of Lean thinking, these concepts will help any
organization get started with Lean thinking. Lean thinking offers the agility
to continuously deliver value in an ever-changing business environment.
Implementing Lean thinking will guide your organization toward a stronger, more
sustainable future.
3
Foundations of Lean Thinking
1) Purpose
Since the goal
of Lean management is to deliver value to the customer, everyone needs a clear
understanding of what that value is and how it is measured.
Once a value is
defined, everyone can begin working together with the purpose of delivering
that value as efficiently as possible. Uniting teams with a shared and clearly
defined purpose is integral to leading a Lean organization.
2) Process
Lean methods
focus tirelessly on process improvement to remove waste and create value.
Lean leaders
believe that flawed processes reduce value and detract from their purpose, so
they empower everyone to identify and work to correct problems and improve
processes.
3) People
Lean
organizations are not led from the top down. Leaders strive to create the
conditions for employees to be their most successful and efficient, and
actively observe, ask questions, and elicit input toward that goal.
They foster
engagement and mentor employees toward continuous improvement. Lean companies
are holistic, and success is the result of goals, attitudes, behaviors, and
processes that are enacted by everyone, every day.
The
Guiding Principles of Lean Leadership
The five Lean
principles provide a framework for creating an efficient and effective
organization. Lean allows managers to discover inefficiencies in their
organization and deliver better value to customers. The principles encourage
creating better flow in work processes and developing a continuous improvement
culture. By practicing all 5 principles, an organization can remain
competitive, increase the value delivered to the customers, decrease the cost
of doing business, and increase their profitability.
The 5
principles of a Lean system guide the daily activities of every Lean leader.
Those principles are:
1) Identify
value
Value is
defined by what the customer needs from a product and informed by their desires
and expectations.
In an internal
system, the “customer” can be another team or department that determines their
requirements for value.
2) Map the
value stream
Determine all
the processes involved in delivering value to the customer from beginning to
end.
At a
high-level, mapping the value stream can be detailing the path of materials as
they move through the design and are delivered in a product, identifying
departments and processes.
Another way to
look at the value stream is to map the flow of information through a department
or organization. Mapping gives greater insight and understanding of business
operations and is the first step in identifying waste.
3) Create flow
Work to move
products, processes, or information through the value stream with no interruptions,
delays, or bottlenecks.
Flow makes
everything move in a tight sequence with high efficiency and little waste.
4) Establish
pull
With a smooth
flow, products can be delivered to the customer as needed. Using a “just in
time” delivery model reduces excess inventory, over- or under-production, or
unmet demand.
The benefit of
pull is that everything is produced highly efficiently, exactly when needed, in
the exact quantities required.
5) Seek
perfection
Even with a
very good process, further evaluation of the value stream always reveals waste
or excess that could be eliminated, and flow can always be refined.
Lean systems
are engaged in continuous process improvement, iterating these 5 principles
over and over in the pursuit of perfection.
Four Lean
Rules-in-Use
Rules create
structure in our systems. Without rules there would be in chaos. Lean rules
provide the guidance needed to implement improvement, explaining the “why”
behind lean tools and the Six Sigma methodology. Lean rules also help develop
new solutions to problems. For everyone in an organization, these rules help
structure activities, connect customers and suppliers, specify and simplify
flow paths, and bring improvement through experimentation at the right level.
The Principles
of the Toyota Production System can be summarized into four basic rules.
Rule 1: “All
work shall be highly specified as to content, sequence, timing, and outcome.
Thanks to
specification in terms of sequence of steps, timing, outcome and content,
people are able to address any deviations. This rule is a necessary step for
people to know implicitly how to do their work.
Rule 2: Every
customer-supplier connection must be direct, and there must be an unambiguous
yes-or-no way to send requests and receive responses.
The path of
communication must be described, shared, known and applied. Each collaborator
so knows implicitly how to connect with each other.
Rule 3: The
pathway for every product and service must be simple and direct.
Services don’t
flow to the next available person—but to a “specific” person
Rule 4: Any
improvement must be made in accordance with the scientific method, under the
guidance of a teacher, at the lowest level in the organization.
Frontline
workers make improvements to their own jobs and their supervisors provide
direction and assistance. The purpose of the supervisor is to act on the
process to continuously improve the performance of the process.
The impact of
those rules on the System is important – “By making people capable of and
responsible for doing and improving their own work, by standardizing
connections between individual customers and suppliers, and by pushing the
resolution of connection and flow problems to the lowest possible level, the
rules create an organization with a nested modular structure”.
Toyota
developed this set of Principles, Rules-in-Use, as the building blocks of a
production system. They allow organizations to gain maximum efficiency so
everyone can contribute at or near his or her potential. When the parts
(activities, connections, and pathways) come together the whole is much, much
greater than the sum of the parts.

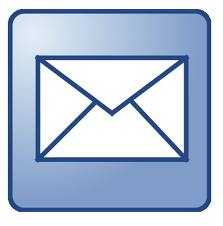





No comments:
Post a Comment