Since March
2020, every person on the planet has had their life shaken by the COVID-19
pandemic in some way. Every aspect of life has been impacted. Our everyday
routines were brought to a stop, and any sense of normalcy was lost.
The COVID-19
pandemic has shined a light on supply chains. The spectacle of empty
supermarket shelves during the early part of the pandemic served as a stark
reminder of what can happen when inventory and service levels are out of sync.
It seems like
every time there is an inventory problem, lean manufacturing or lean principles
get the blame. Lean has gotten a bad rap during this pandemic. Let’s face it,
the current COVID-19 pandemic is a pretty rare occurrence! If anything, crises
like this one illuminate the continued lack of understanding of what Lean is. This
is unfortunate.
Even though
Lean has become foundational to supply chain management, it is still subject to
misinterpretation. A common misconception is that this management philosophy is
essentially about taking people out of business operations. While this can be
an outcome, it is far from the primary purpose of Lean.
In essence,
Lean maximizes value to the customer by eliminating waste from processes. Another
interpretation is that the model strives to meet customer needs with as much
precision — and hence as little inventory — as possible.
Excess
inventory is a form of business waste that ties up capital and consumes
organizational resources that are better deployed elsewhere. Over recent
decades, companies have made considerable strides in reducing inventory volumes
while maintaining high service levels.
However,
COVID-19 delivered a shock to the system that gave companies pause about their
ability to unerringly fulfill customer demand during surges when product
stockpiles had been cut to the bone. The crisis has sparked much discussion
about the need to revisit approaches to inventory management.
While these
last 15 months have not been what most companies had hoped or planned for, it
provided manufacturers with an opportunity to utilize lean manufacturing to
address the shortages and problems caused by the pandemic. COVID-19 has
drastically shifted the regularity of demand—with forecasts changing daily,
sudden influxes of work, and order cancellations—which has emphasized the need
for manufacturers to be flexible. Lean manufacturing encompasses many different
aspects, and the pandemic has given manufacturers who embrace Lean an
opportunity to analyze weaknesses and address them head-on.
This pandemic
showed manufacturers perhaps more than ever before that Lean manufacturing is
about being flexible. Flexibility in your machine capabilities, capacity to
adjust production schedules, availability for quick changeover of techniques, and
cross-training of employees will all help ensure your ability to be responsive
and adapt when it becomes necessary to do so. A highly-responsive manufacturing
operation will in turn allow you to create an agile customer service platform
that will stand out to both your current and prospective customers.
Disruptive,
stressful experiences (like COVID-19) are often opportunities for growth.
Research has shown that crises can change the “if it ain’t broke, don’t fix it”
mantra that pervades many organizations, creating new opportunities for people
to voice their ideas on how to do things better.
There are two
main mindsets that shape our lives (impacting not only our attitudes but learning
as well) especially true in a challenging situation: fixed and growth.
• A fixed
mindset – Learning is a waste of effort – even if it was useful there is no
time or nothing to learn that would help right now; learning is impossible –
even if there was, learning is too hard and asking too much; the only way to
succeed is to play your cards right, always look smart, never look dumb.
• A growth
mindset – Learning is useful – what we learn will make things better; learning
is possible; we can learn what we don’t currently know; setbacks are learning
experiences and obstacles will be overcome.
Adopting a
growth mindset isn’t only important at an individual level. It is also vital
for businesses at an organizational level. A growth mindset leads consistently
to better results.
Practicing Lean
Thinking means reinforcing our belief in better outcomes where achieving
apparently impossible things we learn by doing. As we make things better we
unlock solutions to problems that were never apparent first off (although they
seem obvious in hindsight). It’s precisely when things feel hopeless that warm
hearts and cool minds make a difference – and Lean Thinking is most relevant.
In varying
ways, the COVID-19 pandemic has impacted every single business across the
globe. It’s ample time for all manufacturers to reevaluate their strategies and
make improvements. Companies that already suffered from low productivity,
waste, and inefficiency before the pandemic will likely continue to struggle
the most. More than anything, COVID-19 has shown how important it is to
practice innovation and resilience. To ensure long-term survival, many
businesses are focusing on their productivity and performance, reducing errors,
and utilizing available resources as much as possible.
Even during
times of crisis, efficiency is important. To survive, many businesses are
pivoting the way they offer their products and services to adapt. Using Lean
manufacturing techniques, you can identify what your customers need the most
right now and consider new ways to efficiently match those needs. Whether your
business is reopening or your employees continue to telework, the pandemic
requires us all to innovate and adapt.
It is clear
that Lean Manufacturing is more essential now than at any other time, giving
companies a system for navigating a global landscape that has been forever
altered by the COVID-19 pandemic. Utilizing Lean can help businesses iterate,
solve problems and adapt to keep up with the unprecedented pace of change. Use
Lean to ensure long-term success.

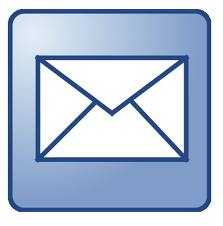





No comments:
Post a Comment