Scrap and rework costs are a manufacturing reality impacting organizations across all industries and product lines. Scrap and rework costs are caused by many things—when the wrong parts are ordered, when engineering changes aren’t effectively communicated or when designs aren’t properly executed on the manufacturing line. No matter why scrap and rework occurs, its impact on an organization is always the same—wasted time and money. And while no one, especially an operations manager, wants to admit it, these expenses add up quickly and negatively impact the bottom line.
Here are 7 ways you can cut scrap and reworking costs and
associated expenses that will protect your bottom line, and improve efficiency
and quality across the supply chain.
1. Improving Communication
Too often, the information needed on the production floor
never quite makes it to the people doing the work. Change orders might be made,
specs might change, or processes might evolve, yet the employees who need to
know somehow don’t.
It’s easy for papers to get missed or misplaced. A plan to
reduce scrap and rework should include an end-to-end solution that tracks every
step of the process and is available for view by everyone involved in the
process.
2. Organizing the System for Documentation
Manufacturers can decrease scrap and rework in their
factories or companies by optimizing the way they document product and process
data throughout their supply chain. Your documentation should have a way to
store every spec, blueprint, work order, and change order for every piece being
manufactured. It should be in real time so there’s no old information in the
system that can lead to errors in the manufacturing process. Documentation is a
key part of change management, particularly in terms of information sharing and
version control.
3. Improving Change Management
Many errors can be traced back to a poorly executed change
management process. When something changes, it should immediately be
communicated to everyone. The right quality management system (QMS) will keep
everything up to date in real time.
4. Optimizing the Manufacturing Processes
Optimizing the manufacturing process means putting in place
a process that recognizes problems so you can take corrective action. It should
track machine maintenance to keep things running smoothly, as well as
compliance and training requirements, and manage conflicts in equipment or
personnel.
Perhaps the most important part of the process in terms of
its potential to generate scrap is the design phase. Good communication and
collaboration between engineers, production team members, and materials
suppliers are key.
A scrap materials plan should be instituted to reuse,
repurpose, or recycle as much scrap as possible.
5. Minimizing Human Error
Damage to parts can occur during transit or whenever manual
handling occurs, so it's a good idea to use automation to limit physical
contact with parts as much as possible - particularly delicate parts that will
be damaged if dropped.
If you can set up a machine to handle a given task in a way
that doesn’t risk damage to the parts you manufacture, then automating that
process is often the best option. Not only will you save money on reprocessing
your parts, you’ll improve your time to market by getting parts right the first
time.
6. Being Proactive
Preempt quality control issues by taking a proactive rather
than a reactive position. Make regular factory inspections to identify problems
and to look for ways to improve processes. You want to find the root cause of
the issue and resolve it as early and as simply as possible. Could the problem
be solved by:
·
Acquiring new equipment and fixtures
·
Improved employee training
·
Software upgrades or additions
·
Greater attention during design phase
·
More emphasis on pre-production processes
·
Additional packaging/handling procedures
7. Implementing End-to-End Quality Assurance
For manufacturers, the best way to reduce scrap and rework
and adhere to the tenants of Total Quality Management (TQM) is to employ Lean.
Using a well-developed and tightly monitored quality control
procedure is essential to minimizing costs associated with rework. Adopting a
TQM philosophy and implementing the PDCA Cycle or another closed loop,
continuous improvement system is a great start. Six Sigma quality and Lean manufacturing
practices will help you eliminate waste and improve quality.
To maintain a competitive edge, manufacturers must
constantly find ways to cut costs and improve efficiency. One way companies can
save time and money is by preventing scrap and rework. Documenting product
data, reviewing manufacturing processes, and clearly communicating changes
throughout the supply chain all prevent scrap and rework from cutting into a
company’s bottom line.

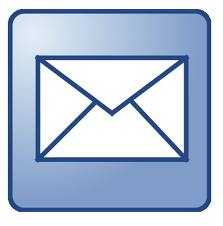





No comments:
Post a Comment