Here is the next addition of tips from the Facebook page:
Lean Tip #3076 – Identify Bottlenecks, Roadblocks, and Issues.
To produce meaningful results, you need to identify what’s holding your process back. What’s going well or not? How can you improve it? Maybe one person’s task is overly time-consuming or a step is unclear, constantly prompting questions. Maybe the process is too dependent on other processes or people.
When identifying roadblocks, it helps to have data associated with the process for analysis. Tracking data points like time, output, and ROI will help you figure out if the improvements you make are effective. The amount of data you need depends; some processes (like our RFP process) might only require a month or so of data, but embarking on an overhaul of a citywide passport request process, for instance, would benefit from a year’s worth of data.
Lean Tip #3077 – Find Ways to Resolve the Issues.
Technology—in particular, automation tools—can often help solve efficiency problems. Automation may already be embedded in the tools you use regularly, you just might not be taking advantage of it. So look closely at the tools you’re using and see how you can use them better; or, if the situation warrants it, consider making a bigger investment into a software tool that includes automation and would be helpful in eliminating unnecessary manual work for your team.
Lean Tip #3078 – Share & Continue to Refine Your Process.
When your process is formalized, document and share it with the team. But just because you’ve reached the end of these process improvement steps doesn’t mean you should stop looking for ways to improve further! Monitor its ongoing performance and continue to refine as you hear more feedback from team members. Over time, there may also be changes surrounding the process that might affect the overall flow, and require additional fine-tuning.
Lean Tip #3079 – Find the Pain Points in the Process
To discover where improvement is needed, look for signs where the current process is failing. Identify the location of bottlenecks and where multiple steps are required to complete just a portion of a procedure. A clear sign of a process pain point is at the stage where customers or employees are becoming frustrated with the workflow. Find the areas where work needs to be regularly redone, or it’s being repeated by different people. This duplication of effort is a waste of time and resources, so you’ll want to find a way to eliminate it.
Lean Tip #3080 – Obtain Stakeholder Buy-in Buy Explaining the Rationale for Change
People are naturally resistant to change, even if it’s for the better. That’s why you must explain the reasons behind the process improvements to obtain buy-in. Moreover, by detailing how the changes will deliver value, such as a better customer experience, stakeholders become motivated to help you.
Lean Tip #3081 – Document Your Current Processes
A wise mentor of mine once said, “You can’t automate what you haven’t defined.” More broadly we can apply that same piece of wisdom to process improvement. When we look at our breadth of offerings and our own processes, we may know in our heads what we mean, and what the ideal process is, but if we don’t write down or document our as-is processes, we lose our ability to experiment in changing them.
By defining our current processes, we can then start discussions from an informed place. Documentation comes in all shapes and sizes. You can make process maps, knowledge articles, scripts, storyboards, customer journey maps, a service catalog and service definitions, or any combination of these.
Lean Tip #3082 – Troubleshoot in Real Time
One of the most useful concepts that continuous improvement borrows from Kaizen is the encouragement to confront problems head-on in an effort to solve it faster. If an issue becomes apparent fix it immediately instead of searching for the “perfect” solution.
Waiting will inevitably cost time and valuable resources. Instead, on-the-spot troubleshooting allows production to continue while the new, improvised solution can be analyzed using continuous improvement techniques. You might find that what was first a temporary fix could lead to permanent positive changes.
Lean Tip #3083 – Encourage Leadership to be Open Minded
Continuous improvement works especially well when individuals are encouraged by senior leaders. Prepare your leadership team by offering special training to encourage new ideas and removing any blockers that may be in a team member's path as they are trying to improve a workflow.
One of the hardest parts of using the continuous improvement model is the desire to strive toward perfection. This is an impossible feat, and the philosophy behind kaizen is to make small changes to be better than you were the day before. Focusing on perfection can lead your team to make changes that aren’t actually necessary.
Lean Tip #3084 – Foster Discovery and Curiosity
Continuous improvement empowers every team member to take ownership of their processes. When your company culture encourages team members to improve business processes in a way that works best for them, it encourages more discovery and curiosity within the entire company. This enables individuals to experiment without the fear of breaking processes or being judged for failure. If something doesn't work, things can just revert back to what they were previously.
Lean Tip #3085 – Keep on Keepin’ On
The part of continual process improvement that can feel overwhelming is the continuous aspect. With continuous improvement there is no perfection, and there is no end, but one of the first rules of project management is that every good project should have a start and end date. Where process improvement differs is that there is likely to always be more we can do, and things we can change. Don’t get defeated by this, but see it as a chance to break up the monotony, and keep innovating.
One thing that makes this easier is that there will always be new technology, solutions, software, or cultural changes that enable us to rethink how we do things. This can keep things exciting. The biggest difference with process improvement from your typical project is that there will always be something new for us to consider. If we ignore this, we run the risk of stagnating or falling behind.
Lean Tip #3086 - Start Small. If Everything is a Priority, Nothing is a Priority
As you delve into a problem, there are many paths for improvement that will open up to explore. It’s very easy to get distracted from what you set out to accomplish when you start to see all of the potential opportunities for intervention and improvement. It’s imperative to keep your goal front and center and continue to ground yourself in what you are trying to accomplish.
To achieve sustainable, meaningful improvements, rigor (being thorough and accurate) to the process must be maintained. What seems at the surface level to be an “easy fix” requires a thoughtful establishment of the new way of doing things for improvement to truly take hold.
Lean Tip #3087 – Acknowledge Past Achievements
In most businesses, improvement initiatives are not really brand new out of the box thinking, as many people have already been exposed to and worked on improvement concepts for a long time, and with some successes. It’ s important to acknowledge past achievements and recognize the champions who made it happen by assigning them significant roles for the new wave. If however, the approach has been firefighting, you may want to build a different team and approach the initiative more proactively. If past projects were not successful then it’s important to show how the new initiative differs from the previous and why it stands a better chance for success.
Lean Tip #3088 - Involve and Work Through People
Avoid being prescriptive with each step of your approach, rather opting to use a facilitated approach to get support and buy in from the teams involved. Always be open to a team using a different approach though still aligned to the overall objectives. Forcing things down people’s throats doesn’t really work well. Good facilitation should allow for a team to reach a pre-conceived conclusion on their own accord. On the same vein, allow the teams to decide what tasks and actions are to be done and offer to help rather than allocate tasks directly to the different people.
Lean Tip #3089 - What Gets Measured Gets Managed.
Put in place a good monitoring system to track the number of ideas generated over time, the level participation of people at any one time and cumulatively during the process, the rate of implementation and the Return on Investment or benefits. Tracking and showing a direct correlation between efforts and benefits is the best way to sustain improvement. Use agreed targets and KPI’s as your “dipstick” check.
Lean Tip #3090 - Keep Everyone Informed of Progress and Results.
The
success of a good improvement program depends on good feedback and
communication surrounding progress. Reports on progress can take many forms, as
long as relevant and timely information is communicated. It’s also important to
publicly celebrate any success coming out of the program. Lastly, where new
records have been set and old improvement targets “smashed”, set new targets
and make them known.

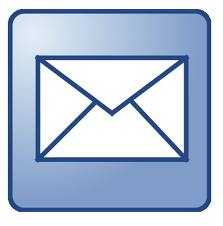




No comments:
Post a Comment