Admit it or
not, all companies face challenges. In today's competitive market, Lean is
turning out to be "the solution" to manufacturing industries across
the spectrum for survival and success.
Lean
manufacturing helps organizations to achieve targeted productivity and more by
introduction of easy-to-apply and maintainable techniques and tools. Its focus
on waste reduction and elimination enables it to be engrained into organization
culture and turns every process into a profit center.
In a nutshell,
lean manufacturing is all about driving toward achieving profitability and
productivity through continuous improvement and resource waste elimination.
With all of the day-to-day tasks
folks need to take care of, it is common that productivity improvement takes a
backseat despite great intentions. To avoid that, consider some of these
methods to spotlight Lean productivity improvement.
Goal alignment:
Perhaps the most powerful aspect of goal setting is its potential use in
building an aligned workforce, equipped, empowered, and motivated at all levels
to work together to achieve its vision for the future. Setting goals can
provide purpose and challenge to energize people to apply their efforts in a
specific, planned direction. Well-set and monitored goals that are aligned
holistically can put your organization on track for increased employee
engagement, productivity, and progress toward achieving its vision.
Visual data
management: Use visual boards to display its goals, targets, and performance
metrics. The look and feel of the visual board should be standard across your
system, with each board including the standard metrics as a designated space
for discussion and prioritization of improvement ideas. The visual board in
each department should be located in an accessible area in the Gemba so that
the data and metrics stay in front of everyone.
Daily huddles:
Daily huddles take place at the department level and last for about 10 to 15
minutes. Huddles are led by the staff and are attended by all members of the
department Huddles take place directly in front of the visual board so that the
metrics that are displayed on the board can be discussed and updated as needed.
Problem-solving:
It is recognized that staff cannot implement all solutions or process
improvement ideas alone and that process changes often involve other
departments or functions. For this reason, part of the daily huddles should be
dedicated to problem-solving. This portion of the huddle includes a review of
improvement ideas submitted by staff, a progress update on ideas that have been
selected for implementation, and feedback received from senior leaders on ideas
that have been submitted to senior levels for implementation and/or resourcing.
Accountability is achieved through review of progress on implemented ideas with
use of a simple WWW (What, Who, and When) form. This process of problem-solving
(idea generation), reviewing progress, and providing feedback is key to
sustaining team engagement.
Employee
recognition: The impact of recognizing employees who engage in Lean
productivity improvement can't be understated. It is essential for the
individual employee and helps cement a culture that values improvement and
signals to the entire organization that leaders care deeply about efforts to
implement positive change.
Each
organization is different and so are the productivity challenges for your
company. You’ll find, however, that even the most basic tools can really hone
in your organization’s ability to eliminate waste and focus on continuous
improvement.

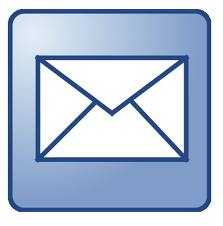





No comments:
Post a Comment