The business
climate is becoming increasingly more competitive. With multiple options for
consumers companies must stay competitive to survive. Many organizations
consider improving quality as the best way to enhance customer satisfaction, to
reduce manufacturing costs and to increase productivity. For this, the cost of
quality (COQ) must be reduced.
The costs
associated with making sure that your product is of good quality are called
quality costs. It includes preventing, detecting, and fixing any issues with
the product. It's crucial to ensure that your product meets the customer's
expectations, which is not just a matter of making it look nicer.
As defined by Philip B. Crosby in his book Quality Is Free, the cost of quality has two main components: the cost of good quality (or the cost of conformance) and the cost of poor quality (or the cost of non-conformance).
Cost of Poor QualityExternal
failure costs are
associated with deficiencies that are found after the customer receives the
product. Also included are lost opportunities for sales revenue.
- Sales returns and allowances
- Replacing defective products
- Service level agreement penalties
- Complaint handling
- Field service labor and parts costs
incurred due to warranty obligations
- Product recalls / Legal claims
- Lost customers and opportunities
- Downgrading
- Processing of customer complaints
Internal
failure costs are
the cost of deficiencies discovered before delivery that are associated with
the failure to meet explicit requirements or implicit needs of customers. Also
included are avoidable processes losses and inefficiencies that occur even when
requirements and needs are met. Internal failure costs consist of: (1) the cost
of failure to meet customer requirements and needs and (2) the cost of
inefficient processes.
- In-process scrap and rework
- Troubleshooting and repairing
- Design changes
- Inventory required to support poor
process yields and rejected lots
- Re-inspection / retest of reworked
items
Cost of Good
Quality
Appraisal
costs are
incurred to determine the degree of conformance to quality requirements.
- Test and inspection (receiving,
in-process and final)
- Supplier acceptance sampling
- Product Audits
- Calibration
Prevention
costs are incurred
to keep failure and appraisal costs to a minimum.
- Quality planning
- Education and training
- Conducting design reviews
- Supplier reviews and selection
- Quality system audits
- Process planning and control
- Product modifications
- Equipment upgrades
The Total
Quality Cost can be summarized as all investments in the prevention of defects,
the testing of product to assure Quality, or the failure of a product to meet a
customer requirement.
Many of the
costs of quality are hidden and difficult to identify by formal measurement
systems.
The iceberg
model is very often used to illustrate this matter: Only a minority of the
costs of poor and good quality are obvious – appear above the surface of the
water. But there is a huge potential for reducing costs under the water.
Identifying and improving these costs will significantly reduce the costs of
doing business.
It is important
for companies to understand what they need to do to reduce their overall cost
of quality. This will help them improve their business processes and
operations, which ultimately lead to better profitability.
The worst type
of cost out of these four categories of the cost of poor quality is the
external failure costs. Organizations should make their best effort to reduce
the external failure cost.
Spending more
on prevention and appraisal costs usually leads to a reduction in internal and
external failure costs.

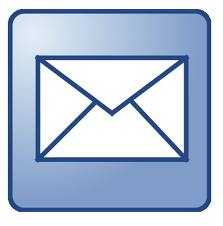





No comments:
Post a Comment