Here is the next addition of tips from the Facebook page:
Lean Tip #3406 – Gather the Right People for Kaizen
Carefully selecting the team members is crucial. The meeting should encompass diversity in terms of their areas of expertise. With analytical and creative skills, they can contribute innovative ideas that enhance the processes.
Including personnel who are not directly related to the current goals, but have not yet experienced Kaizen, provides an opportunity to train more staff on these dynamics.
The invited team should consist of representatives from all areas relevant to the goals, including supervisors and managers. If necessary, external experts, customers, or suppliers can be added, considering their potential interest in the process.
Lean Tip #3407 – Assign Roles and Responsibilities on the Kaizen
Assigning specific roles and responsibilities in organizing the meeting is fundamental. Designate a team leader to guide the meeting, an individual responsible for documenting progress, and someone to present ideas. This allocation helps maintain order during the meeting.
It is also important to involve managerial personnel who can approve improvement proposals since Kaizen aims for small but rapid changes. This way, the presented ideas can be transformed into tangible actions to improve company processes.
Lean Tip #3408 – Create a Distraction-Free Environment
Properly preparing the work environment is crucial since achieving results necessitates substantial planning. Ensure it is a space conducive to comfortable gatherings and provides access to the necessary tools and materials for the event.
The work environment must be pleasant and devoid of distractions, allowing participants to focus on the discussions at hand. It is common to temporarily suspend all deadlines and projects, enabling attendees to maintain their concentration on the designated task.
Lean Tip #3409 – Train the Staff for the Kaizen Event
Another aspect to consider is providing training for the employees. The team should receive instruction on improvement management tools and their application before, during, and after the event. This training reinforces the comprehension of the topics discussed during the meeting.
Take the time to provide guidance on what to expect during the event and which improvement tools will be used. It is also crucial to communicate the expectations for the event.
Lean Tip
#3410 – Celebrate Progress and Improvement
Recognizing and celebrating the team’s small accomplishments is essential. It is worth noting that no one within the company possesses a better understanding of its operations than the teams and responsible individuals. In order to encourage outstanding suggestions, incentives must be provided, as employees may exhibit disinterest in change without them.
It is vital to acknowledge and reward team members who have contributed to the meeting, particularly when employees may be hesitant to alter their working methods. In summary, celebrating achievements plays a pivotal role in the sustainable growth of any company.
Lean Tip #3411 – Keep Your Shop Floor Clean and Organized
Process
quality is critical to increasing the quality of products and other outputs,
but the way your team manages its workspace is also important. Quality control
in manufacturing isn’t complete without quality control inspections that
consider the organization and cleanliness of the shop floor.
Inspections
should:
- Look for overall cleanliness. A
clean shop floor keeps workers safer by ensuring spills are cleaned up
right away and other items that might cause trips and falls are put away.
A clean working environment allows people to take pride in what they do,
and that transfers to the quality of the work.
- Checking for proper use of tools and
equipment. Quality inspections should ensure people
are using resources correctly and that employees are well-trained on the
equipment they use.
- Ensure specific safety rules are followed. Quality audits might note whether employees were wearing the proper safety gear, for example, or that machines and tools were being used in the safest way.
Lean Tip #3412 – Set Standards for Manufacturing Quality
Find out what external stakeholders, including customers, vendors, or business partners, expect and whether there are contracts and service level agreements defining those requirements. Your quality control standards must at least meet these requirements.
You can, however, aim for quality that exceeds external requirements. Consider business needs, costs and what might be a challenging but possible goal for your manufacturing teams. You may also want to consider building room in your manufacturing quality standards for failure that doesn’t impact customers.
Lean Tip #3413 – Utilize Manufacturing Quality Metrics to Grow and Improve Your Operations
Once you’ve defined your quality control process, including standards you can use to identify success, continue to gather metrics on quality. Consistently looking at your quality metrics helps you understand whether your quality control processes are working. They also help you identify continued areas for improvement.
Continuous process improvement initiatives — such as Six Sigma — note that perfection isn’t achievable. However, manufacturing organizations can use quality metrics to drive continuous process improvement initiatives to move ever closer to perfect.
Lean Tip #3414 – Ensure Proper Quality Control Training and Resources
The best outcomes from quality programs come when you have the right resources. That includes using quality control software for manufacturing and ensuring everyone who uses that software (and other resources) is appropriately trained. Visual Planning helps you achieve those goals with ongoing support and consulting, ensuring you and your employees are trained to use our software to improve quality and scheduling in your organization.
Lean Tip #3415 – Utilize Technology To Enhance Quality Control
The right technology simplifies complex processes so you can meet production needs without getting bogged down in the details. Visual management supports everyone from ops managers to shift leaders on the shop floor. Leverage your expertise in manufacturing to create tools that let you see process data in real-time and make on-the-fly changes to keep up with demand while supporting quality.
Lean Tip #3416 – Show Empathy in the Workplace: Approach Challenges From a Different Perspective
Imagine the problem or situation from your team member's perspective. This can help you better understand their propositions and point of view. Even if you reach a different conclusion from them, you may have a better understanding of their thought process, which can inform future discussions.
Lean Tip #3417 – Show Empathy in the Workplace: Ask Questions to Understand
Ask what experiences have led to a particular conclusion. Consider the potential underlying factors that caused the person to feel the way they feel. For example, if you're speaking with a buyer who's unhappy with a product, you can ask about their expectations of the product and the specifics of their experience. If you don't understand the situation, keep asking questions until you do. Empathy comes with a deeper understanding of what has happened.
Lean Tip #3418 – Show Empathy in the Workplace: Offer to Help
Ask colleagues if they need help with projects and offer assistance when possible. This can help team members feel like you support them and empathize with their challenges at work. It may sometimes be challenging to determine when a coworker is struggling, so part of empathy is observing your environment and taking the initiative to offer help before someone asks.
Lean Tip #3419 – Show Empathy in the Workplace: Avoid Assuming You Know What Others are Thinking or Feeling.
Another way to practice empathy is by avoiding assuming that you know what others think or feel. This can be a difficult habit to break, but it's important to remember that we can never really know what's going on in someone else's mind. Instead of making assumptions, try to ask questions and listen openly to what the other person has to say. This will help you gain a better understanding of others' perspectives.
Lean Tip #3420 – Show Empathy in the Workplace: Be Aware of Your Own Biases
When
trying to be empathetic towards others, be aware of your own biases and
preconceptions. Everyone has unique experiences and perspectives shaping how we
see the world and its people. Think about how your own biases might affect how
you view someone else's situation and then try to set those feelings aside to
see or feel things from their perspective.

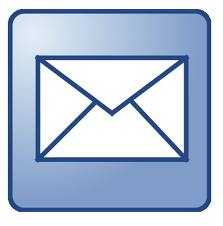




No comments:
Post a Comment