Without
respecting, involving, and drawing upon the expertise of employees who perform
the work every day, you overlook the most fertile source of practical and
ready-to-implement suggestions for improvement.
By engaging
people in the process of problem solving, it reduces resistance to the
recommended solutions. Rather, participants want to see their ideas implemented
and be successful because they are their ideas. Lean is inclusive; it is not
done to people; it is done by people who feel empowered to create value.
If you really
want to empower employees, you'll need to create a company culture that
encourages and rewards innovation. You may start by asking individuals to look
for ways to improve efficiency, output, safety, etc. in the tasks they perform
every day.
Allow them to
make mistakes as a form of learning. Show that it is really OK to make
mistakes. Trust that people have the right intentions and will make the right
decisions, even if they are different than your own. Let them know you really
support their decisions.
Many attempts
to implement Lean have been superficial. Unfortunately, the reason is that most
companies focus too heavily on tools such as 5S and just-in-time, without
understanding that Lean is a system that must permeate an organization’s
culture and emphasize respect for people.
Tools and
techniques are not secret weapons for transforming a business. Toyota’s
continued success at implementing these tools stems from a deeper business
philosophy based on its understanding of people and human motivation. Its
success ultimately rests on its ability to cultivate leadership, teams and
culture; to devise strategy; to build supplier relationships; and to establish
and maintain a learning organization.
Whether you
work at a small or large company, consider how you can create a Lean thinking
culture. You may have made some hard decisions about whether or not you have
the right people in the right roles to foster this. Having the right talent
with the right attitude goes the distance. You can never teach drive and
passion. You can always teach skills.
Ask yourself if
you are fostering a culture of Lean thinking where you respect your employees
and the expertise, they provide each day. Can you leverage this to create
lasting value in your company and drive out waste?
In the end Lean
is all about people. The power behind
Lean is a management's commitment to continuously invest in its people and
promote a culture of continuous improvement.
Establishing good working conditions to promote teamwork is a key
component of respect for people.

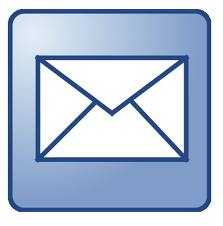





No comments:
Post a Comment