There is often
a missing link in many Lean organizations - which is, the set of leadership
structures and behaviors that constitute a lean management system. People
frequently equate ‘Lean' with the tools used to standardize processes and
generate efficiencies; and organizations tend to focus more on the
implementation of these tools. However, implementing tools only accounts for,
at most, 20% of the effort needed in lean transformations. The remaining 80%
should be spent on changing leaders' behaviors and practices; and eventually
their mindsets.
Lean leadership
bridges a crucial divide: the gap between lean thinking and lean tools. Lean
leaders have an essential role to play in lean transformations.
What’s Lean
Leadership?
Lean leadership
is all about commitment; commitment to your employees, commitment to the system
and commitment to making changes towards improvement. Leaders in a lean
environment need good communication skills to understand the problems their
people face.
Lean leaders
can give their teams the tools to succeed and encourage them to make wise
decisions that lead to long-term, competitive growth. It typically involves
helping individuals achieve professional and personal progress and
acknowledging their contributions to the workplace. This type of leadership can
foster a culture of continuous improvement through employee engagement,
decision-making and communication.
Here are some
roles and responsibilities of lean leaders:
Coach and
develop others
As a leader, it
may be your responsibility to help others improve. Coaching can enable
continuous improvement and personal growth. When your teammates reach their
full potential, this can ultimately make your task as a leader easier. Coaching
can also enable you to take an interest in your team's development and show
that you care about their success, possibly making them more loyal to the
company. Giving your team the tools to succeed and encouraging them to make
wise decisions can lead to long-term, competitive growth. Mentoring employees
can also make them more valuable to the company.
Challenges
The lean leader
should serve their team by providing support, guidance, and development
opportunities while challenging them to improve performance. Lean leaders must
challenge their teams to go beyond their comfort zones and aim to achieve
excellence. This can involve setting ambitious goals, providing feedback, and
encouraging team members to take risks and learn from their mistakes.
Facilitate
Teamwork
Teamwork is a
key component because lean leadership requires employees from different
departments to collaborate to improve processes. Encouraging teamwork can help
streamline communication channels and ultimately improve communication.
Teamwork can also contribute to developing a positive culture, which can boost
employee satisfaction by motivating them while at work.
Go to Gemba
(Walk the Floor)
As a lean
leader, you can use Gemba, a method that encourages you to visit the
workstation and engage with employees face-to-face. Instead of depending
primarily on reports, executive summaries and other edited forms of
information, you can go to the source to listen to employees and learn about
the processes that guide the organization’s success. To create an effective
environment for improvement, it can be helpful to develop faith in your team's
abilities, expertise and experience.
Drive
Continuous Improvement Mindset
A lean leader
empowers their workers to take on the responsibility for resolving their own problems,
by making it acceptable to attempt something even if it does not work out. It's
essential to demonstrate that participating in improvement activities,
challenging existing practices, and observing processes, are all part of a
complete problem solving approach that will advance the organization.
When leaders
are true role models for Lean behavior, this inspires everyone within an
organization to deepen their understanding of Lean, fully engage with a
transformational program, and close the gap between Lean tools and Lean
thinking to fully realize the value of Lean.

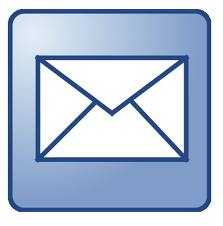





No comments:
Post a Comment