This month A
Lean Journey Blog turns 15 and as I look back on how I got started and who
influenced my journey I wanted to revisit a previous series I started in 2012
called the Meet-up.
One of the
things I am so found of in the Lean community is the general wiliness to share
with each other. I have learned some
much from my very experienced colleagues since I have been an active
contributor. Every month I roundup the
best Lean related posts and articles I found particularly valuable from these
fellow bloggers and contributors. Each one has their own story and opinions to
share.
The goal of Meet-up is provide you an
opportunity to meet some influential voices in the Lean community. I will ask these authors a series of
questions to learn about them, their lessons, and get their perspective on
trends in industry.
My name is
Kevin Meyer, and I retired on January 1st, 2024 after 14 years as co-founder
and CFO of Gemba Academy. I continue to
stay involved with the company on various strategic projects. Prior to Gemba Academy I worked in various
engineering, operations, and executive positions at primarily medical device
manufacturers, ending with being president of a mid-market medical device
company for eight years. I am currently
a member of a couple angel investment groups where in addition to investment I
mentor and advise startups on the opportunity of leveraging lean methods.
2. How, when, and why did you get introduced
to lean and what fueled and fuels the passion?
Back around
1997 I was working for Abbott Laboratories and transferred to their Salt Lake
City facility to be operations manager of their largest molding operation,
producing parts critical for other factories around the world. The operation was 24/7/365, running at 100%
capacity, but was nearly 3 months behind schedule, creating crazy visibility
and “help” from corporate.
While
researching how to address the capacity issues while waiting for new presses to
arrive in 3-6 months, I came across AME.
Doc Hall, Dave Hogg, and Dan McDonnell from AME taught me about quick
changeover, and by the time the new presses arrived we had caught up and even
had extra capacity. I was sold and
became a lean evangelist from that point on.
We used it to quickly quintuple production at a subsequent facility I
became responsible for, and in my last position we reduced our costs so much
that we could out-compete so-called “low cost” Asian competitors from the
so-called “high cost” state of California.
Along with Ron Pereira and Jon Miller, we started Gemba Academy to give
back and help train others on the concepts that had made us so successful.
3. In your opinion what is the most powerful
aspect of lean?
Respect for
people, hands down. Recognizing that
traditional financial reports place a value on the “cost” of the pair of hands
that is assembling product (or support activities), but there is no offset for
the “value” of the brains that hold the creativity, experience, and
collaborative multiplier - unlike with capital equipment - therefore poor and
damaging decisions are made to chase “low cost labor.” Find ways to tap into the power of those
brains, while providing financial and psychological safety to encourage the
risk that creates learning, even from failure.
4. In your opinion what is the most
misunderstood or unrecognized aspect of lean?
That lean is
only for manufacturers. An interesting
data point is that over the past 14 years, subscribers to Gemba Academy’s
training material changed from being predominantly manufacturers to being
predominantly non-manufacturers. There
has been strong interest, and great results, in healthcare, government,
services, and even education.
5. In your opinion what is the biggest
opportunity for lean in today's world? How can that be accomplished?
Lean principles
and methods can be applied anywhere, even outside of work. However, many of them (such as the power of
one piece flow) are counterintuitive and need to be demonstrated to be
believed. We need more people
experienced with lean to help spread the good news into more and different
industries and situations. There are
many lean consultants and many lean training companies, but value is really
demonstrated when the concepts are successfully implemented and returns are
experienced. This takes passionate,
inquisitive, and creative people driving lean change - both from the top in
executive positions but also from within organizations. Lean is being taught in some universities -
such as what Eric Olsen is doing at CalPoly, but a deeper understanding of lean
should be taught as part of core curriculums.
Through their answers to these questions
hopefully you will get a sense of the thinking behind those who are shaping the
Lean landscape. I continue to keep
learning and thankfully with the willingness of these practitioners to share I
am positive you will, too.

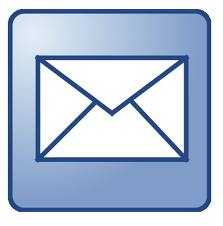





No comments:
Post a Comment