An essential
element in Lean thinking is Kaizen. Kaizen is the Japanese name for continuous
improvement. While Kaizen is really about improvement involving everyone
everyday it is often associated with a structured event. It is the technique
that improves quality, productivity, safety, and workplace culture. Kaizen
focuses on applying small, daily changes that result in major improvements over
time. They are essential to get cross-functional and multi-level teams involved
in a Lean transformation. In that respect,
kaizen events have a dual role – to make improvements but also to teach and
communicate.
Based on my
experiences, here are ten principles for optimizing processes and implementing kaizen
to maximize productivity within your continuous improvement efforts:
Principle 1.
Improve Everything Continuously
This is the
core tenet of the Kaizen method. With their commitment to improving everything
continuously, adopters of the Kaizen method question the best practices of
their organization to uncover areas for potential improvement. The improvement
never ends. After improving one element, others can become not compatible or
induce defects. Create a list of elements that require improvement and improve
them one by one.
Principle 2.
Say No to Status Quo
Old managers
teach: if something works, don't touch it. In Kaizen we assume that everything
can work better. There is no place for methods that cannot be changed. Every
aspect of every process can be a subject of improving actions.
Principle 3.
Aim for Small Improvements Rather Than Perfection
As the saying
goes Rome was not built in a day, neither is performance excellence. By
improving the way small tasks are regularly performed, you will yield greater
results rather than attempting to perfect the workings of a whole department at
once. Aim for small, continuous changes, and results will come slowly, but
steadily.
Principle 4.
Empower Every Team Member to Provide Solutions to Problems
Not only does
giving everyone a say provide them with a sense of belongingness, but it also
provides the organization with fresh ideas and innovative concepts by which
certain issues may be avoided altogether.
Principle 5.
Use Creativity Before Capital
Save money
through small improvements and spend the saved money on further improvements.
In western culture changes have to be substantial in order to be visible. In
eastern culture changes sometimes are substantial. But in most cases, those are
small improvements that lead to small savings. But after many small
improvements you'll earn a considerable sum of money.
Principle 6.
Tacit Learning, Learn by Taking Action
Kaizen promotes
the philosophy of action, learning through experience and reduces
procrastination. In Japan, professionals associate another term with Kaizen:
'genchi genbutsu'. This literally means 'real location, real thing'. This
common saying encompasses the same core meaning: taking action, experiencing
the real thing and not just the theory, is what leads to development.
Principle 7.
If Something is Wrong, Fix It
Mistakes are
human. It is natural and acceptable to make them. What is unacceptable is to
attempt to finish a task without rectifying the error. Own up to the mistake if
you are held accountable, correct it, and attempt to find a solution to avoid
the same mistake later on.
Principle 8.
Use Data Over Opinions
Using data to
influence your decision-making process is a powerful way to reduce errors and
constantly improve. Data provides us with information that is backed with
proof, while opinions reflect a person’s or group’s beliefs. Establishing
metrics before you action any changes enables you to define success and failure
and to act accordingly. Using data can help to eliminate the risk of human bias
and assumptions, creating an efficient and goal-oriented decision-making
process. Companies that invest in, gather, collate and interpret data prior to
decision-making will have an edge over others who are solely experience or opinion-driven.
Principle 9.
Ask Why to Get to Root Cause
Due to the lack
of time and the pressure to meet deadlines, we often overlook the root cause of
errors, which leads to the repetition of the same mistakes. Always encourage
your staff to get to the root cause of problems. Use a 5-Whys Analysis and keep
asking “why” until you get to the root cause of the problem. Share the possible
solutions so that everyone in the team can benefit from the findings.
Principle
10. Improvement has No limits. Never Stop Trying to Improve.
Never say to
your employees: ok, we've done it, now we can do it another ten years without
any changes. There is entropy in each process. Customers’ needs change
constantly. New technologies are being implemented. Your competitors still try
to make better product. The improvement program is a never-ending story.
The initial
benefits that are implemented will lead to further improvement opportunities
down the road. When done properly, Kaizen just keeps going through the cycle of
identifying improvement opportunities, coming up with solutions to those
opportunities, implementing the solutions and finally testing them. If the
solutions are positive, the cycle starts over with new improvement
opportunities. This will continue forever, leading to an optimized facility
that is never satisfied with the status quo.

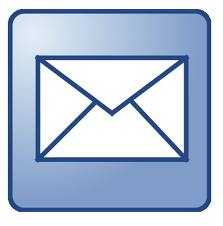





No comments:
Post a Comment