As you’ve seen
I have been revisiting a previous series I started in 2012 called the Meet-up.
One of the
things I am so found of in the Lean community is the general wiliness to share
with each other. I have learned some much from my very experienced
colleagues since I have been an active contributor. Every month I roundup
the best Lean related posts and articles I found particularly valuable from
these fellow bloggers and contributors. Each one has their own story and
opinions to share.
The goal of
Meet-up is provide you an opportunity to meet some influential voices in the
Lean community. I will ask these authors a series of questions to learn
about them, their lessons, and get their perspective on trends in industry.
Today I thought it would be fun to share my responses and thoughts.
1. Who
are you, what organization are you with, and what are your current
lean-oriented activities?
I'm the founder and principal contributor of A
Lean Journey Blog, a
site dedicated to sharing lessons and experiences regarding Lean thinking,
improvement practices, and leadership.
I'm the
Senior Manager of Strategy & Operational Excellence for Mirion’s
Technologies North America Group. Currently, I am leading the continuous
improvement initiatives to proliferate a “Lean” culture at Mirion’s
Technologies Group, offering radiation measurement, personnel protection,
advanced safety and search, and decontamination and decommissioning solutions
for a variety of worldwide applications. I have a passion for teaching problem
solving skills, Lean philosophy, and quality improvement methods by actively
learning, thinking and engaging people.
For over 25
years, I have been implementing lean within operations management, continuous
improvement, and quality disciplines for innovative high tech manufacturing
companies such as Lucent Technologies, JDSU, Legrand Wiremold, and Mirion. I've held a number of leadership positions within operations management, Lean,
and quality disciplines of innovative high tech manufacturing companies.
2.
How, when, and why did you get introduced to lean and what fueled and fuels the
passion?
My introduction
to lean manufacturing is probably somewhat typical. After coming from a research and development
role to an operations role I discovered Lean.
In 1999 I started learning what Lean manufacturing was all about and I
have been learning about it ever since.
In the beginning Lean was a way for me to meet operational objectives.
Now I know it is a profound way of thinking that encompasses all I do. Lean is
the best business performance system I have seen.
Looking back
now I was so fortunate to have a number of great coaches or sensei as we call
them. One of my early teachers was David Stec. He was the co-author of “Better
Thinking, Better Results” with Bob Emiliani, who is a great Lean
practitioner/teacher in his own right (plus he is a local guy to me) David
taught me Lean basic.
I was also
fortunate to have had Toyota Production System Sensei named Motoo Usui-san who
taught new TPS correctly. He worked in the same office as Taiichi Ohno.
Usui-san never gave you an answer only a question. I had to solve the problem
myself.
I had the
pleasure to work and lead lean efforts and Wiremold a Shingo Prize winning
facility. There are a number of books and a great many practitioners who cut
their teeth in that factory who went on to greatness. It was a great sandbox of
learning and development.
I have sought out
many opportunities to learn along the way.
I hold a Lean Certification and a Six Sigma Black Belt from Central
Connecticut State University, Lean Bronze Certification from Society of
Manufacturing Engineers, a Master Lean Six Sigma Black Belt from the Management
and Strategy Institute, and is a Shingo Institute Alumni.
By drawing on my
experience in Lean, Six Sigma, and Quality Management Systems I co-authored
ASQ's Lean Handbook, an educational reference guide to support Lean
Certification. I have also published 12 articles. I’ve had the pleasure of
presenting at 6 conferences, doing 2 radio shows, and hosting more than a dozen
webinars.
My passion is
fueled by those wonderful "a-ha" moments. Those times when I see the light turn on for
someone, a new lean thinker, a new problem solver, someone that can see wastes
and opportunities all around them. I
also enjoy the opportunities I get to meet some great people on similar journeys
of their own. Everyone you meet is
another opportunity to learn more.
3. In
your opinion what is the most powerful aspect of lean?
I think my
answer to this question has probably changed over last 15 years. While there
are a number of powerful aspects of Lean if done well, I am going to focus on
two: 1) Use daily management to engage employees in the Gemba and 2) Empower
improvement with Kaizen.
Lean organizations make use of Daily Management systems, a structured process to focus
employee’s actions to continuously improve their day-to-day work. Daily Management empowers employees to identify
potential process concerns, recommend potential solutions, and learn by
implementing process changes. Daily Management, if done right, can be a critical tool
in any organization’s toolbox to engage frontline staff in problem-solving and
to deliver customer value.
Lean Daily
Management includes three components: (1) alignment of goals and effort; (2)
visual data management, daily huddles, and problem-solving; and (3) leader
standard work.
Kaizen events are a powerful improvement tool because people are
empowered to come up with new ideas to help the business. Employees are
isolated from their day-to-day responsibilities and allowed to concentrate all
their creativity and time on problem-solving and improvement.
The purpose of kaizen is to involve everyone, everywhere, every day in making
simple improvements. These small improvements add up overtime and result in an
extraordinary and never-ending transformation of processes. Companies which use
Kaizens have found they generate energy among those who work in the area being
improved and produce immediate gains in productivity and quality.
4. In
your opinion what is the most misunderstood or unrecognized aspect of lean?
Too many think
Lean is just about apply tools. Most fail to fully understand the people aspect
of a Lean organization. This is a myth perpetuated by less than knowledgeable
leaders. Most companies miss the point that 90% of Lean is about people and
culture change and only 10% is about the tools. They expect Lean to be the
“silver bullet”, which, even if it does not solve all their problems, will at
least aid in short-term gains. There are thousands of Lean tools, because each
problem requires its own unique tool to help solve it. People are needed to
solve problems. Tools don’t apply themselves. Basically, leaders have to learn
to think differently and see their customers and business differently, that’s
people development, not tools development.
Lean which is
commonly referred as TPS (from it's originators) is the "Thinking People
System" for me. It is about learning to see waste and solve problems
through the development of people. This is a frequently missed and even
understated purpose in lean. Lean is truly about people because tools don't
solve problems, people solve problems.
As in the
namesake of my blog "A Lean Journey - The Quest for True North" Lean
is not about the destination but the direction or path you take toward this
idealistic place. Lean is not something you check off your "To Do
List". It is about the constant,
persistent, even relentless pursuit of improving your current situation. And
this improvement brings you to the next current state and so on. Usually, it
means doing something you haven’t done before because your old habits will not
work in your new system. Lean is not technique you apply to your business
system but rather a methodology that replaces your business system.
In my opinion
leaning out the waste is not necessarily the difficult part but rather the
identification of the wastes. Waste is
all around us, yet many cannot recognize it.
I like to say that "activity does not equal
productivity". The real challenge
is to break status quo, get out of your comfort zone, and learn to "see".
This means observing the actual condition at the actual place at the actual
time.
If you can
educate and engage your workforce to relentlessly identify and eliminate waste
by solving problems, you will be well on your way to embracing the full power
of Lean.
5. In
your opinion what is the biggest opportunity for lean in today's world?
How can that be accomplished?
Every industry
can benefit from Lean process improvement, but I would have to say that the
biggest opportunity for Lean is in our service industries. Lean has a proven track record in many
manufacturing operations. I think we all
see things every day in our lives as we interact with businesses that bug
us. These are things that cause poor
service, higher costs, less value and more waiting. It would be nice to live in place where
continuous improvement is commonplace.
Maybe that sounds utopian, but this is happening in many service
industries already.
Government - Government agencies have found that
when Lean is implemented, they see an improved understanding of how their own
processes work, that it facilitates the quick identification and implementation
of improvements and that it builds a culture of continuous improvement. Lean for government focuses on governing
and serving citizens with respect and continuously improving service delivery
by cutting out "waste" and "inefficiency" in processes;
this in turn will result in better services overall, engaged civil servants as
well as more value for tax-supported programs and services.
Education - The demand for schools to operate
more efficiently and direct more resource to the classroom means Lean
methodologies are becoming more and more recognized in education. They can be
used to reduce variance and streamline administrative processes, such as
admissions and enrollment, certification, grant administration and repair and
maintenance practices.
Healthcare - Instilling a Lean culture and
implementing Lean processes vastly improves service delivery. In the healthcare
industry specifically, the application of Lean can reduce the amount of time
nurses spend looking for wheelchairs, patient records or medicines, and
increase the amount of time they spend taking of patients.
Retail - The retail and hospitality industry
is reliant on excellent customer service, timely delivery of products, and
accurate inventory counts. Lean provides a useful strategy for improving these
important elements.
Insurance
& Financial Services
- As another process-driven service industry, companies in financial and legal
services are ideally positioned to leverage the benefits of Lean. An
application for a bank loan, a request for an insurance quote, or conveyancing
for example, may go through many systems and hands before the process is
completed. Removing non-value adding tasks and eliminating errors can greatly
increase the ability to meet customer requirements faster and more accurately.
Office - Lean can easily be applied to office
environments where lots of non-value adding tasks are being carried out.
Insufficient equipment, over-ordering of stationery, duplicating processes,
having to wait for multiple signatures and underutilized personnel are all
examples of waste. The result of removing this waste and streamlining processes
is greater productivity, a happier workforce, and a better service for
customers.
In fact, any
administrative function of a business can benefit from Lean, such as
Accounting, Operations, Sales, Marketing, HR and IT. Delivery in all these
areas involves processes which can be improved with Lean principles.
There are many
more opportunities for Lean to be successful.
Lean focuses on processes; has a measurable impact on time, capacity and
customer satisfaction; and involves all employees. This formula will help many organizations to
be more successful.

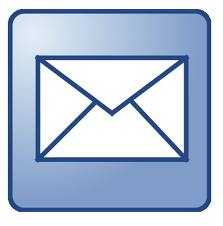





No comments:
Post a Comment