In May 2024 A
Lean Journey Blog turned 15 and as I look back on how I got started and who
influenced my journey I wanted to revisit a previous series I started in 2012
called the Meet-up. One of the things I am so fond of in the Lean community is the general wiliness to share with each other. I have learned so much from my very experienced colleagues since I have been an active contributor. Every month I roundup the best Lean related posts and articles I found particularly valuable from these fellow bloggers and contributors. Each one has their own story and opinions to share.
The goal of
Meet-up is provide you an opportunity to meet some influential voices in the
Lean community. I will ask these authors a series of questions to learn
about them, their lessons, and get their perspective on trends in industry.
In today's edition, we are going to meet-up with Paul Critchley. I met Paul through the Northeast Region of the Association of Manufacturing Excellence (AME). I used to serve on the BOD for many years. Any way AME offers great networking opportunities for Lean practitioners. Over the years Paul and I've kept in touch and even collaborated a couple of projects together.
Here are his
answers so you can learn more:
1. Who are
you, what organization are you with, and what are your current lean-oriented
activities?
I'm Paul
Critchley, and I'm currently the President of New England Lean Consulting.
After 20 years in industry (mostly as an ME Manager or Ops Manager, I started
NELC in 2012 with the goal of helping small-to-medium sized companies embrace
Lean principles. I figured that there were plenty of places that wanted &
needed Lean, but couldn't figure out where to start, nor could they afford to
hire someone full time to do it.
2. How,
when, and why did you get introduced to lean and what fueled and fuels the
passion?
I got
introduced to Lean in 1999 when I took a Project Engineer role in South
Carolina when my employer had won some work from Toyota. It's safe to say that
we got a "crash course" in TPS back then, and I was hooked
immediately. It was so far removed from what I'd learned in college, and from
how we had been operating, that it really caught my attention. Been practicing
Lean ever since!
3. In your
opinion what is the most powerful aspect of lean?
In my opinion,
it's Respect for People. Gallup polls routinely show that 67% of workers are
not engaged with their work/employer. It's awfully hard, if not impossible, to
get folks excited about changing things when they've already decided that they
don't like the place or their manager(s). We have to make caring for our
associates’ job #1. When we do that right, the rest will come.
4. In your
opinion what is the most misunderstood or unrecognized aspect of lean?
For those who
follow me, they'll know that my biggest pet peeve is this misnomer that Lean
fails at extraordinarily high rates. I've read articles that state 70% all the
way up to 99%, and it's all B-O-L-O-G-N-A. Those numbers are misquoted often
from a survey that's almost 20 years old now, and included about 400 anonymous
respondents, so right out of the gate I'd say that the data is 1. old and 2.
not statistically significant. Likewise, the question that was asked was (and
I'm paraphrasing) was: "Did you get everything out of your Lean
event/transformation that you'd wanted?" We rarely get everything that we
want, and respondents agree, but that doesn't then equate to
"failure". I'd say it more aptly implies that "we're not done
yet" or "we're still learning". As a Lean community, we need to
stop proliferating this misnomer. If people who are new to Lean hear this
enough, it may cause them to not attempt Lean in the first place, and that's
far more dangerous than trying and failing.
5. In your
opinion what is the biggest opportunity for lean in today's world? How can that
be accomplished?
In my opinion,
the biggest advantage Lean provides is that it focuses us on long(er) term
goals. I've seen first-hand the damage short-term thinking has on an
organization, and it's detrimental. As long as we continue to reward that
behavior, then I don't believe that we'll be successful. We'll continue to have
turnover, continue to struggle with adaptation and growth, and we won't see the
successes we desperately wish for.
If we focus on
those internal things (caring for one another, helping each other, learning,
growing, challenging), the external things (Cost, Quality, OTD, etc.) will
come. We've shifted our focus from managing causes to managing effects, and
it's not going to yield what we want it to in the long term.
Through their
answers to these questions hopefully you will get a sense of the thinking
behind those who are shaping the Lean landscape. I continue to keep
learning and thankfully with the willingness of these practitioners to share I
am positive you will, too.

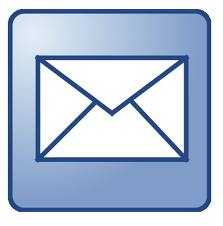





No comments:
Post a Comment