In May 2024
A Lean Journey Blog turned 15 and as I look back on how I got started and who
influenced my journey I wanted to revisit a previous series I started in 2012
called the Meet-up. One of the things I am so fond of in the Lean community is
the general wiliness to share with each other.
I have learned so much from my very experienced colleagues since I have
been an active contributor. Every month
I roundup the best Lean related posts and articles I found particularly
valuable from these fellow bloggers and contributors. Each one has their own
story and opinions to share.
The goal of Meet-up is provide you an opportunity to meet some influential voices in the Lean community. I will ask these authors a series of questions to learn about them, their lessons, and get their perspective on trends in industry.
Today, we Meet-up
with Bruce Hamilton who I met many years ago when I started my lean journey professionally. His company GBMP was a partner and has been at several companies I've gone to over the last 25 years. I've been fortunate to join and share at the annual Northeast Lean Conference that GBMP organizes which is great opportunity for the lean community to learn from each other. Bruce's experience has been invaluable to me over my career so I think you'll like to hear what he has to say.
Here are his answers so you can learn more:
1. Who are
you, what organization are you with, and what are your current lean-oriented
activities?
- My name is Bruce Hamilton. I’m the President of the GBMP Consulting Group (recently rebranded from GBMP to emphasize the consulting part side of our organization.)
- I created a Blog, “oldleandude.org” in 2009 and post to it once a month about topics that I think might be interesting for managers who are trying to get traction with Lean concepts and culture.
- I also give a monthly webinar, “Teatime with the Toast Dude,” started in 2012, with the same objective as the blog.
- Collaboration is very important to me and GBMP. We work with many other non-profits such as TSSC, LEI, MEP, Shingo Institute, AME to develop our Lean community. Recently, for example, GBMP collaborated with six other non-profit organizations to develop the “Future of People at Work Symposium,” a bit of breakthrough its alignment of organization that had previously operated unilaterally.
- On a daily basis, I still work with clients, teach an occasional Shingo Institute workshop, and provide leadership to our organization.
2. How,
when, and why did you get introduced to lean and what fueled and fuels the
passion?
Here
is an abbreviated history. In 1985, I
was working as the IT manager at a small manufacturer. When the MRP implementation failed, the
materials manager was fire, and I was offered the job. I had no experience with manufacturing, so
began reading. An early book, The
Goal, caused me to question many of the practices I saw, both technical and
social. This book was followed by Zero
Inventories, which contained a footnote leading to Shigeo Shingo’s Toyota
Production System from an Industrial Engineering Point of View. After that there were many other books and
individual who provide more learning and inspiration. Today, I do less reading, but continued to be
inspired by other students of continuous improvement.
3. In your
opinion what is the most powerful aspect of lean?
It requires and fosters human development, and provides a professional challenge for every job – the basis of GBMP’s slogan, “everybody everyday”.
4. In your
opinion what is the most misunderstood or unrecognized aspect of lean?
Lean
is seen by most organizations solely as a technical challenge. The technique (e.g., 5S, SMED, pull,
mistake-proofing, etc.) is necessary, but far from sufficient. There are two other challenges: 1) Especially
for managers and engineers, understanding of the conceptual basis behind the
techniques is critical to implanting.
Without that understanding, ideas like pull and one-by-one make no
sense. 2) Creating a favorable
environment for improvement, what Toyota calls “TPS Managerial”, known more
generally as culture.
5. In your
opinion what is the biggest opportunity for lean in today's world? How can that
be accomplished?
Lean’s
biggest opportunity then and now is at single location, privately-held small
and medium-sized organizations that are less vulnerable to short-term policy
and financial decisions, and where management can physically witness the
problems and the improvements. While
any organization may get some benefit from Lean, larger ones suffer from too
much physical distance and policy/organizational
inertia, and are unable to address the adaptive changes needed to get the full
benefits of Lean. Best thing to do is
find the pockets of opportunity within the bigger organization is focus on
pocket of opportunity and promote at the highest lever available.
Through
their answers to these questions hopefully you will get a sense of the thinking
behind those who are shaping the Lean landscape. I continue to keep
learning and thankfully with the willingness of these practitioners to share I
am positive you will, too.

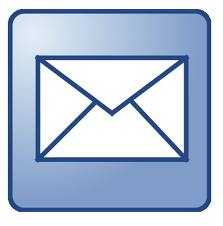





No comments:
Post a Comment