![]() |
Production team members discovering opportunities and trying solutions during a Kaizen. Image Source: Tim McMahon |
An essential
element in Lean thinking is Kaizen.
Kaizen is the Japanese word for a “good change” (Kai = change, Zen =
good) or change for the better. It’s a
continuous improvement tool to make work easier, safer, and more productive by
studying a process, identifying waste, and applying small incremental
improvements that ensure the highest quality.
Kaizen thinking
is based on making little changes on a regular basis: always improving
productivity, safety and effectiveness while reducing waste. Western philosophy is often summarized as,
"if it ain't broke, don't fix it." However, the Kaizen philosophy is
to "do it better, make it better, improve it even if it isn't broken,
because if we don't, we can't compete with those who do."
Many business
leaders envision Lean initiatives as massive endeavors that require long
training sessions, big meetings, and complete overhauls. Yet the reality is
that some of the most successful Lean initiatives begin with a commitment to
creating a culture that’s focused on small, continuous improvements. It’s the
only way to achieve long-term success.
Kaizen involves
every employee - from upper management to operators. Everyone is encouraged to
come up with improvement suggestions on a regular basis. This is not a once a
month or once a year activity. Once we make this way of thinking normal the
lack of any sort of event goes away. The ultimate goal is a culture of
continuously looking at processes with an eye for improvement.
In my recent
article published in Quality Magazine I share the benefits of Kaizen, the
reasons why many organizations fail when implementing Kaizen, and 10 steps for
executing a successful Kaizen. Click here to continue reading.

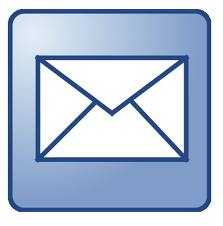





No comments:
Post a Comment