In May 2024
A Lean Journey Blog turned 15 and as I look back on how I got started and who
influenced my journey I wanted to revisit a previous series I started in 2012
called the Meet-up. One of the things I am so fond of in the Lean community is
the general wiliness to share with each other.
I have learned so much from my very experienced colleagues since I have
been an active contributor. Every month
I roundup the best Lean related posts and articles I found particularly
valuable from these fellow bloggers and contributors. Each one has their own
story and opinions to share.
The goal of Meet-up is provide you an opportunity to meet some influential voices in the Lean community. I will ask these authors a series of questions to learn about them, their lessons, and get their perspective on trends in industry.
Today, we Meet-up with John Hunter who I first met when I started blogging. The idea for the round-up series started with John. He used to do a management carnival series highlighting posts from other bloggers on management that I really enjoyed. It included several of my posts. I turned that idea into the monthly round-up you see today. Beyond John's management expertise his knowledge in Quality and the people aspect of Lean is profound. I'm sure you'll find John's answers to these questions will offer insights that will help you on your journey.
Here are his answers so you can learn more:
1. Who are
you, what organization are you with, and what are your current lean-oriented
activities?
John Hunter
I have authored the Curious Cat Management Improvement blog https://management.curiouscatblog.net/
for 20 years. See more on my professional history https://johnhunter.com/professional_life
I recently created the Curious Cat Management Improvement Institute https://ccmii.org/ to help those that want to improve the practice of management. This is where I am focusing my lean related activities now. If you have suggestions, ideas or questions please let me know.
2. How,
when, and why did you get introduced to lean and what fueled and fuels the
passion?
My father introduced me to these ideas when I was a kid. I learned about data, variation and how to seek evidence supporting beliefs as a young child. I remember lessons my father taught me when I was in grade school, including my father presenting at my 2nd grade class on data and variation (with a bit of on the fly process improvement and child psychology) https://engineering.curiouscatblog.net/2007/12/05/playing-dice-and-childrens-numeracy/
Lean ideas were used to examine what was and wasn’t working in relation to, for example, how we did our chores. We would collect data on what worked and didn’t as we tried to improve. It seemed like a natural way to do things, though I could see that others didn’t operate this way. You can read more on my experiences growing up http://management.curiouscatblog.net/2015/01/22/who-inspires-your-management-thinking-and-action/
I attended a management seminar, during the summer, that my father gave to the City of Madison when I was a high school student (related: Doing More with Less in the Public Sector
https://williamghunter.net/articles/doing_more_with_less_in_the_public_sector ). And a few years later I started to use the ideas at work, where I learned how challenging it was to help people to: use data effectively, think systemically, focus on continual improvement and work on improvement of the management system.
3. In your
opinion what is the most powerful aspect of lean?
Most misunderstood is that the way lean is done most often (very poorly) is accepted as what “lean” is. In some sense this is right, as most efforts are not very well done and really focus on cutting costs without understanding most of what lean is about.
But in another sense that situation creates the belief that lean doesn’t have respect for people at the core, which of course it does if you listen to any of the lean people I think you should listen to.
4. In your
opinion what is the most misunderstood or unrecognized aspect of lean?
The biggest
problem is trying to solve everything at once. The whole emphasis of process
improvement is to sift through all the noise of the symptoms and causes to get
to the root cause – that Red Thread, which if you pull will make a major impact
on your process. Instead, we brainstorm and diagram our way to a list of causes
and fail to narrow them down to a singular focus – fix one thing at a time. The
inherent basis of Lean is to standardize, measure, and then take a single step
up, improving one thing. Then, we standardize and measure again. This is what
continuous improvement is all about.
The problem
with trying to chase all the symptoms and causes at once is that process
improvement efforts take way too long! Business owners, expecting immediate and
measurable returns do not see results. The effort is seen as a waste, and the
entire effort is killed before it’s finished.
5. In your
opinion what is the biggest opportunity for lean in today's world? How can that
be accomplished?
The same that it has been for decades: to improve the working lives of millions of people and to improve products and services used by billions of people. The biggest opportunity is the widespread adoption of these ideas that will lead to better results for everyone: employees, customers, investors…
> How can that be accomplished?
It is really hard to transform your organization to think systemically, focus on continual improvement and actually build management systems using respect for people principles. I think it can be accomplished by people learning more deeply about lean thinking so they can keep making improvements that will increase the ability of the organization to keep moving in the right direction.
Related: How to Lead From Any Level In the Organization
https://management.curiouscatblog.net/2021/06/22/how-to-lead-from-any-level-in-the-organization/
How to Get a New Management Strategy, Tool or Concept Adopted
Through
their answers to these questions hopefully you will get a sense of the thinking
behind those who are shaping the Lean landscape. I continue to keep
learning and thankfully with the willingness of these practitioners to share I
am positive you will, too.

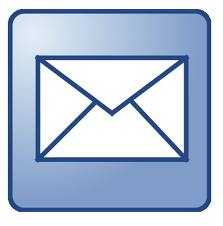





No comments:
Post a Comment