In a continuation of my recap from Day 1 the 2nd day
of the Northeast Lean Conference Leveraging Lean to Thrive in Uncertain Times
did not disappoint. Andrea Haas, President at Summit Polymers, demonstrated how
they used Lean Practices to Succeed in automotive industry after Tariffs, COVID
labor shortages, microchip shortages, global supply chain disruptions, and inflation.
They specifically focused on Jidoka, building in quality with Poka Yoke and Andon,
standardized work, and kaizen to successfully navigate these uncertain times.
Cultivating a Lean Culture Through Individual Change
Management
Evan McCoy, Continuous Improvement Leader at Kone, shared
how to create awareness, desire, knowledge, action, and results around creating
a Culture of Continuous Improvement. What can we do about the fact the 70% of
change initiatives fail?
He promotes the ADKAR Framework for Change
Awareness – change begins with understanding why
Employees will want to know why? Why now? What’s Wrong?
Leaders must be ready to answer what’s changes and why,
risks of not changing, what’s not changing, why now
Desire – Change involves personal decisions
Build desire and momentum by showing not telling. Focus on
the small improvements. Celebrate and show recognition.
Knowledge – Change requires knowing how
Do and show rather than tell and teach. Formal training
(10%), learning through experience (70%), learning through socialization (20%)
Ability – Change requires action in the right
direction
People leaders must set the tone for the teams. Time is
constrained resource create space and culture for improvement. Allow for
experimentation and risk. Improvements must be visible and impactful.
Reinforcement – Chage must be reinforced to be
sustained
Meaningful link between improvement and daily work. Simpler, easier, more efficient improvement in process. Accountability systems to reinforce. Performance measures that connect and reward and recognize by leadership and peers.
Breaking the Buy-In Barrier: Getting Lasting Senior
Leadership Commitment
Melissa Lin, Associate Director Continuous Improvement at
Phillips, knows about the importance of senior leadership buy-in. To be
successful you need senior leadership commitment actively and visibly
participating throughout the journey, building a coalition of peers, and
communicating with employees.
Is the resistance directed at you or because of you or
something else?
These are the most common obstacles to senior leadership
buy-in, what they really mean, and how to overcome them.
Gimme the ROI – They want the facts, data,
quantifiable benefits and/or risk mitigation to buy-in so you can solve that
with a strong, clean A3.
I don’t
see the problem – They want the facts verified with their own eyes,
irrefutable evidence change is required to be convinced so bring them to the
Gemba and let the problems show themselves or bring it to them in the form of
spaghetti diagrams or VSMs.
This isn’t
a priority for us – They want to see connection to the big picture, need
help focusing on top priorities and fixing problems on their plate so use
Hoshin Kanri to connect to True North and use Root Cause & 5 Whys to solve
problems.
I don’t
think it’ll work
– They want results, proof of improvements, and one less thing to worry about
so have well scoped value stream for kaizen and show respect for people.
Developing a Company of Problem Solvers
Edge Coble, Director of Continuous Improvement at Gemline, shared
how they use Continuous Improvement Boards to develop, engage, and empower
everyone into problem solvers. Continuous improvement is about seeing the
problem not waste elimination. Waste is a byproduct of poor flow.
The CI Board is:
Way to
identify and resolve problems
Aligned
to corporate goals & dept KPIs
Diversity
of viewpoints, knowledge & experience
Cross-pollination
& rapid deployment of improvements
Source
of accomplishment and pride
The CI Management Model for Engagement has these leadership styles
Collaborative – CI Leadership – working
together
Leave Alone – Manager not around
Authoritarian – Tell what to do
Parental – Treat as part of
extended family
Continuous improvement is about spotting the disruptions in
your team’s workflow, understanding why it’s happening, and determining a speedy
correction.
Created an idea board in MS Planner (Teams) – see picture
Passing the Baton to a New Generation of Problem Solvers
Karl Wadensten, President of Vibco, was the final keynote of
the conference. As Vibco celebrates its 52nd anniversary, Karl shared how
embracing Lean has powered his company through challenging times and still
enables them to thrive today. I’ve been to their facility several times and it
is very impressive so I would recommend a visit.
The future of continuous improvement will be characterized
by a more balanced approach that prioritizes job satisfaction, social
responsibility, and sustainable practices alongside traditional metrics of
success. Organizations that embrace this paradigm will not only enhance
employee engagement and satisfaction but will also contribute positively to
society an the environment.
Gen Z has a distinctive perspective on the current
workplace, influenced by their upbringing, and educational experiences which is
different than other generations.
Emphasis on purpose – seeks work
that aligns with their personal values and contributes positively to society.
Focus on learning and growth
Importance of mental health
Comfort with Technology
Preference for collaborative Work
Skepticism Towards traditional
career paths
Job satisfaction over job security
Understanding these perspectives allow organizations to
create environments that attract and retain Gen Z talent.
When the rubber hits the road. The boss is the coach. The
boss is authentic. The boss shows vulnerability. The boss knows when to lead
and when to follow. The boss show’s purpose and passion for his people.
The 21st Annual Northeast Lean Conference will be October 27 & 28, 2025 at the Double Tree Hotel & Conference Center in Manchester, NH.
The 2025 Northeast Lean Conference

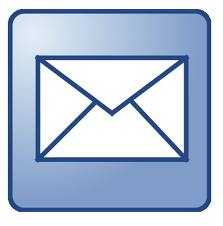





No comments:
Post a Comment