Accountability in the workplace can mean that all employees are accountable for their own actions, behaviors, performance and decisions. It's also linked to increased commitment to work and employee motivation, which leads to higher productivity. Employees who feel they are being held accountable for their actions, behaviors and decisions are motivated to perform better because they know they will get feedback.
Creating a culture of accountability is an essential tool used by high-performing teams to develop better work relationships, eliminate surprises, and improve overall job happiness. Here are 3 ways to create more accountability in the workplace:
1. Model accountability on your team
When it comes to building a culture of accountability, change starts with you.
Team accountability is impossible without strong personal accountability in place first, so it’s important to first work on yourself before approaching an accountability conversation with co-workers or direct reports.
2. Set clear expectations for team members
It may sound obvious, but doing what your teammates expect of you requires clarity around what’s expected in the first place.
Unclear expectations and lack of specificity create accountability gaps. To fill these gaps and reduce ambiguity, try to be as specific as possible.
Strategies for stronger expectation-setting:
- Define project ownership: Work with your team to clearly define who owns what. Many teams like to use a RACI chart for each project — clarifying who should be responsible, accountable, consulted, and informed on the work.
- Use a detailed project spec template: Project specs and one-pagers help teams create alignment, clearly define expectations, and eliminate accountability gaps. Each one should specify the project timeline, ownership, and specifics on the deliverables.
- Get more intentional with meeting action items: Action items are valuable for a variety of purposes – building accountability is a big one. When action items come up in team meetings, it’s all too easy for them to slip through the cracks or lack enough specificity to drive follow-through. To keep action items top-of-mind, assign a notetaker to document them as you go and share them out immediately after the meeting ends.
- Publicize roles and responsibilities: When people know their role, they’re more likely to feel a sense of ownership and take charge of their work. Likewise, when teammates understand each other’s roles, it strengthens collaboration, communication, and trust because they know who to turn to for what and what is (and isn’t) expected. As a manager, make it a point to publicize everyone’s role and revisit expectations on a regular basis.
3. Create a “safe space” environment
Trust and psychological safety are foundational to building a culture of accountability. Without them, folks on your team won’t feel comfortable opening up, sharing transparently, and taking ownership if things don’t go as planned.
When you build up psychological safety on your team, people feel safer taking risks, asking for feedback, and being vulnerable in front of each other through the ups and downs that inherently come with any job.
Building systems for accountability into your team’s workflow can help employees feel more empowered and help managers support them, without micromanagement.
You can have better performance discussions, build healthy habits around planning and goal-setting, and achieve better results. If you want your team to be more effective, invest in team and individual accountability.

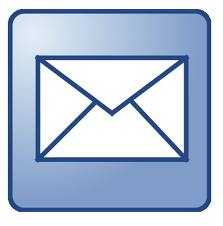




