Here is the next addition of tips from the Facebook page:
Lean Tip #3661
– Develop a Strategic Plan
Develop and
review your strategic plan on a regular basis. Analyze the environment, the
market, the competitors, and the available internal resources. Set goals and a
roadmap. Review the operation of your company from a global perspective and do
not get lost in one department. Visualize the short, medium, and long term.
Automate repetitive processes. Introduce the planning of your resources, means
of production, and materials. Consider technological evolution and investment
as key elements to achieve manufacturing cost reduction.
Lean Tip #3662
– Involve your Staff in the Life of the Company
Usually, your
staff knows more than anyone else where the operational wastes are. They know
the opportunities for improvement, and they often even know the solutions. It's
not necessary to make any large capital investments to tackle improvements.
Involving your
staff will improve their well-being and the performance of your business.
Make visible
the standards reached by the work teams. Share the goals with regular meetings
and internal publications: boards, magazines, mailings, etc.
Lean Tip #3663
– Create Indicators that Promote Improvement and Pursue Them
Your company
members need to know where to go and the performance indicators are the
trigger. Establish key performance indicators (KPIs) that have a direct impact
on your business. It will also drive all the members in the right direction.
Combine departmental with interdepartmental indicators. It will favor the
interaction of all the members of the organization.
Lean Tip #3664
– Eliminate Old Practices
The main part
of avoiding complacency is getting rid of old and tired traditions that are
obsolete. Because we live in a culture that continually makes changes and
improvements, it is important for businesses to keep up with this to stay
relevant for the company’s continuous improvement.
To get rid of
old practices throughout your life, find out about stepping up your day by
improving upon things that you already do. Let go of your former habits, even
if they give you some benefit at the time. As time goes on, you should progress
also.
Lean Tip #3665
– Don't Assume New Methods Will Work
Just because a
method is new does not mean that it is improved. It is the main thing to move
far beyond the status quo to be effective in business. This will probably
require trial and error until achievement is accomplished. When it comes to
your personal life, it might take some time to find a method that works for you
when it comes to achieving your goals. Just Because something worked for
another person does not imply that it will essentially work for you. Try a few
things before you focus on a new method.
Lean Tip #3666
– Empower All Employees to Speak Up
Everyone who is
associated with the success of the company—from the CEO to the line
workers—should be encouraged to offer suggestions and solutions for problems
that can be fixed or improvements that can be made. While you don’t have
employees dealing with your own life, you can still energize your friends and
family to make suggestions if they see things that you could work on.
Talk with
different people about your goals and get their feedback. Encourage your family
and friends to make suggestions if they see things that you could work on.
Lean Tip #3667
– Be Proactive For Continuous Improvement
Stop hesitating
because of possible hurdles that you predict, and move forward toward your goal
for continuous improvement. It is important to not take any chance in the way
of improvement, and for each person in the organization to take personal
responsibility for making improvements.
While it is one
thing to sit around and discuss the improvements that should be made, it is a
different thing to actually make an action plan to implement the changes.
Lean Tip #3668
– Maintain a Positive Attitude
Maintaining a
positive attitude is one of the most important rules of Kaizen. Only by keeping
a positive mind can you see new opportunities; opportunities to grow yourself
and your organization.
Only by keeping
a positive outlook can you also foster the motivation to implement change and
go after a better organizational environment.
Where there’s a
will, a way is always found. A positive attitude and strong hope is what fuels
a strong will. Without a positive attitude, you stop fighting, you stop
innovating, you become blind to opportunities, and you start wasting your life.
There’s always
a move you can make towards improvement, no matter how hard the situation is.
Never forget that. That’s how kaizen masters think.
Lean Tip #3669
– See Waste and Problems as an Opportunity
All the big
problems your company is facing are nothing but big opportunities. Problems are
opportunities to bring out solutions, to contribute value, to grow, to improve
yourself, to contribute ideas, develop your talents, and consequently become
better, more valuable, earn more, be more attractive, become stronger, and so
on.
If you want to
be valuable to your company, society, family and so on, you have to solve
problems, fix things, and create value. It’s that simple.
Problems are
your and your organization’s biggest opportunity. The more problems you see,
the more ideas you should have. You can always turn waste into gold.
Lean Tip #3670
– Learn by Taking Action, It’s Called Validated Learning
You learn the
most by doing things. It’s called “Genchi Gembutsu” in Japanese or “Leaving the
building” in English. You can read 100 books on how to swim, but it can never
compare to actually doing it.
You can’t
implement change based only on theoretical knowledge. You must become a master
of validated learning and superior insights into how things work.
Lean Tip #3671
– Choose a Simple Solution, Not the Perfect One
Simplicity is
always better than complexity. Implementing change is hard, and implementing
complex change is even harder, if not close to impossible.
Therefore,
choose a simple solution you can start implementing immediately. A successfully
implemented small change will motivate you to implement new and bigger changes.
By doing so,
you will increase your capacity and stamina for more complex change. Small
progress can always lead to bigger progress, but in the beginning, forget about
the big steps and start small.
Choose simple
solutions to start with. Never be afraid to progress slowly in the beginning,
only be afraid of stopping.
Lean Tip #3672
– Seek the Wisdom of Ten People Rather Than the Knowledge of One
In the
information age, there’s a rule that you have to go for the best knowledge
right away. We produce and duplicate so much information that you can easily
get lost in bad advice and useless info.
So, you have to
be extremely picky about what information you consume.
Nevertheless,
you should never seek the knowledge of only one person. Everyone has their own
interpretation of the world (subjective reality) and everyone sees the
situation from a different angle.
The more angles
you understand, the closer you can get to the objective reality (the truth).
Consequently, you better understand the problem and what needs to be done.
In addition,
the more ideas you receive, the easier you can integrate them and innovate
further.
Lean Tip #3673
– Accept No Excuses and Make Things Happen
Excuses don’t
make products and services better, innovations do. The Japanese Kaizen
philosophy illustrates the value in being proactive. In our technology driven
world, there are ample tools and products to interact with customers. These
customer interactions can be used to shape the products and services as per the
needs of the customers.
The idea is to
find a bunch of methods that work for your company to deliver the results. The
best companies find ways to make things happen, they build new features,
services and products to pleasantly surprise their customers. They make things
happen by constant experimentation and connecting the dots for their customers.
Lean Tip #3674
– Think Long Term and Foster a Culture of Improvement
The essence of
Kaizen lies in the principle of continuously improving. This means that
business processes must be constantly optimized and that every little
improvement counts.
Kaizen isn't
just about solving immediate problems; it's about the long term. Manufacturers
who adopt this method must be prepared to invest time and resources in
continuous improvements that will pay off over time.
Developing a
culture of continuous improvement requires more than just tools and techniques;
it demands a Kaizen mindset, where every team member is committed to
identifying opportunities for enhancement and driving positive change across
the entire organization.
Lean Tip #3675
– Go to the Gemba, Act Quickly, and Standardize Processes
Kaizen
emphasizes the importance of walking the shop floor, i.e., go to “Gemba,” to
observe processes in action directly. This enables managers and employees to
see the real problems and better understand operators' challenges.
Another Kaizen
characteristic is the emphasis on immediate action. When problems are
identified, corrective action is taken without delay to implement improvements
swiftly, transforming obstacles into opportunities and ensuring that the
workflow remains uninterrupted.
Once
improvements have been made, new practices must be standardized to maintain the
gains and facilitate future improvements. This includes documenting processes,
providing ongoing employee training, and monitoring key performance indicators
(KPIs) to ensure that the changes bring significant results.

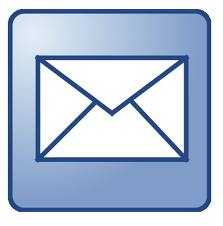





No comments:
Post a Comment