A Lean journey
is full of steps not all of which are forward. Failure will occur. It’s ok, the
purpose is learning, and we learn through experimentation. Trying new
approaches, exploring new methods and testing new ideas for improving the
various processes is exercise for the mind.
Lean grew out
of years of practice and experimentation at Toyota. No matter how much better
they are than their competition, they continue to find more and more
opportunities to improve each and every year. Lean involves the creation and
implementation of continuous experiments to improve your strategies over time.
This means experimenting with every process every day to get it right. We learn
problem solving through hands-on improvement experiments. In Toyota and in lean
thinking, the idea is to repeat cycles of improvement experiments forever.
So leaders must
create a culture that puts failure in its proper place: a useful tool for
learning, and a natural part of iterative experimentation. Management must
avoid the temptation to harshly judge unsuccessful ideas. A leader who allows
for experimentation sends a clear signal that personnel are encouraged to find
better methods and products.
Organizations embarking on a Lean journey should follow a disciplined process of systematic exploration and controlled experimentation. Kaizen is the process which determines whether processes resulted in improvements. It refers to an on-going activity by all people (including managers) to relentlessly and incrementally change and improve practices in small experiments.

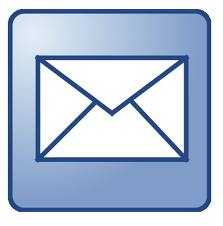





No comments:
Post a Comment