Effective meetings require careful planning and management. Preparing for a meeting involves more than reserving a room, setting up a few chairs and plugging in the coffee. Thinking through the basics of the meeting will help cement a successful effort when the simple acronym O.A.R.R.’s is employed.
O. Desired Outcomes: If a meeting is needed start by
defining specific desired outcomes. Think about what would be created or
accomplished as a result of the meeting. A desired outcome is a clear concise
statement of the end product in 25 words or less. Describe what will be
produced such as “a list”, “a plan”, “an agreement”, etc. Desired outcomes
promote clear, focused thinking and work towards a common goal. Take the time
to develop desired outcomes and get the group’s agreement to work on them.
These outcomes need to be in writing, agreed upon at the meeting and visible
for all to see. They address such things as products, such as a list, or
knowledge, such as awareness or understanding.
Remember useful desired outcomes are clear concise
statements that are brief, specific and measurable, using nouns not verbs, and
are written from the perspective of the participant.
A. Agenda: The meeting “road map” that includes what will be
discussed, time frame and who is responsible for each item on the agenda. It
covers all the topics to address the desired outcomes, plus a section for
evaluation. List the topics to be covered during the meeting and process you
will use. Estimate the time you need for each topic. Prioritize the agenda
items and allocate quality-meeting time to the most important items - not at
the very beginning or end of the meeting. Be sure to get the group’s agreement
to follow the agenda or change as needed.
R. Roles: Each person at the meeting has a specific function
or Role. Someone will serve as a facilitator or guide for the meeting, a
recorder captures the content or essence of what each person has to say on the
“group memory”—large sheets of newsprint paper or easel pads are used for this
purpose, a time keeper keeps track of the time and alerts the group when time
is running out in each agenda item, and the remainder of the group serve as the
content “drivers” of the meeting and participate fully.
R. Rules: A list of 5-7 group-agreed-upon Rules helps
maintain focus of the meeting. These meeting agreements are behavioral guides
for the meeting session framed in positive terms, whenever possible. They may
include:
- Start and end on time,
- One person speaks at a time,
- Listen with respect,
- Be open to other ideas and perspectives,
- Make decisions by consensus.
If you want to experience team alignment in a meeting, don’t
forget your OARRs. Start every meeting by briefly confirming your Outcomes,
Agenda, Roles and Rules to get everyone rowing in the same direction.

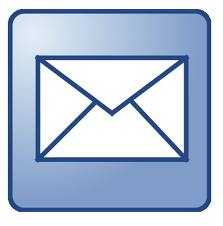




