Many organizations
have begun the journey to make their businesses lean. Some have reported early successes
while others have struggled or fallen into the rut entitled "flavor of the
month." As is usually the case with this kind of organization change,
implementation precedes understanding. What follows are missteps, rework,
confusion, organizational angst, and the aforementioned "flavor of the
month" criticism.
As you continue
your Lean Journey here are 5 ways to accelerate your roadmap:
Start With
Lean Training for Everyone
The key to
implementing any new idea or concept is training. It must be top down training
so that everyone is on the same page. The more understanding of what lean
manufacturing is all about, why you are implementing it and the expected
benefits from it, the more likely you are to get buy-in.
It is very
important that everyone in the company become committed to lean culture. In
order to make the culture successful, managers and employees need to be aware
of waste within the company and be prepared to attack and eliminate it. Making
sure that the employees are empowered to do this, not just pushing the job off
on someone else, is imperative in the proper function of lean culture.
Ensuring
everyone is on the same page will help to avoid conflict. At the same time, it
is important to ensure people have the space in which to think about what
improvements they think need making.
Use Daily
Management to Engage Employee in the Gemba
Lean
organizations make use of Daily Management systems, a structured process to
focus employee’s actions to continuously improve their day-to-day work. Daily
Management empowers employees to identify potential process concerns, recommend
potential solutions, and learn by implementing process changes. Daily
Management, if done right, can be a critical tool in any organization’s toolbox
to engage frontline staff in problem-solving and to deliver customer value.
Lean Daily
Management includes three components: (1) alignment of goals and effort; (2)
visual data management, daily huddles, and problem-solving; and (3) leader
standard work.
Focus on
Problem Solving
One of the most
common mistakes that companies make when embarking on a Lean transformation is
trying to do too much at once. These “boil-the-ocean” initiatives are long,
costly and often end up stalling under the weight of their own ambition.
The PDCA cycle
(Plan-Do-Check-Act) is a simple and effective framework for lean
problem-solving. It guides your employees through four steps: defining the
problem and its scope, implementing a solution and testing its results,
evaluating the outcome and identifying any gaps, and standardizing the solution
and making further adjustments.
Empower
Improvement with Kaizen
Kaizen events
are a powerful improvement tool because people are empowered to come up with
new ideas to help the business. Employees are isolated from their day-to-day
responsibilities and allowed to concentrate all their creativity and time on
problem-solving and improvement.
The purpose of
kaizen is to involve everyone, everywhere, every day in making simple
improvements. These small improvements add up overtime and result in an
extraordinary and never-ending transformation of processes. Companies which use
Kaizens have found they generate energy among those who work in the area being
improved, and produce immediate gains in productivity and quality.
Seek Expert
Help from Lean Sensei
A Lean coach or
sensei provides the necessary guidance, support, and expertise to help
organizations navigate their journey successfully. They guide teams in adapting
to new ways of working and help them overcome any challenges encountered in the
process based on their extensive experience and knowledge of Lean. They help
organizations identify inefficiencies in their processes and implement
effective solutions.
The challenge
with lean is that, despite its attraction to many executives who want to cut
costs and increase productivity, a lean process doesn’t happen overnight. There
are plenty of obstacles to overcome.

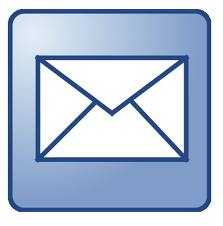




