In May 2024
A Lean Journey Blog turned 15 and as I look back on how I got started and who
influenced my journey I wanted to revisit a previous series I started in 2012
called the Meet-up. One of the things I am so fond of in the Lean community is
the general wiliness to share with each other.
I have learned so much from my very experienced colleagues since I have
been an active contributor. Every month
I roundup the best Lean related posts and articles I found particularly
valuable from these fellow bloggers and contributors. Each one has their own
story and opinions to share.
The goal of Meet-up is provide you an opportunity to meet some influential voices in the Lean community. I will ask these authors a series of questions to learn about them, their lessons, and get their perspective on trends in industry.
Here are his answers so you can learn more:
1. Who are
you, what organization are you with, and what are your current lean-oriented
activities?
I am John
Knotts, a personal and professional business coach and consultant.
I own my own
business, Crosscutter Enterprises,
where I provide coaching, consulting, training, and professional speaking. I’m
also an author of six booms, with two more on the way this year. My wife and I
own Fine Print Farms, which is one of the largest equestrian businesses in all
of South Texas. We operate on 100 acres and have upwards of 40 horses on
property at all times. I’m also a Senior Coach with Gemba Academy.
As a coach and consultant and Fractional Chief Operating Officer, I help business owners start, grow, scale, and improve their business. In Gemba Academy, I am evolving their Lean and Six Sigma training and certification programs.
2. How,
when, and why did you get introduced to lean and what fueled and fuels the
passion?
In 1990, the
United States Air Force started to roll out their Total Quality Management
(TQM) training – the called it, Quality Air Force. I was a Security Policeman
at the time, but found the courses very interesting and exciting. In 1996, I
was stationed at a remote assignment in Turkey, and the Air Force dictated that
100% of Air Force personnel would be trained on the Quality Air Force Awareness
course. I was the only person assigned to the location that had any formal
training, so I became the local instructor for the program. In 1998, while
stationed at my next assignment in Germany, I had the opportunity to retrain
into the Manpower and Quality career field. There, I was formally trained and
employed as an industrial engineer, process improvement practitioner, and
strategic planner. My first job at Ramstein Air Base was to run their 17
quality training programs for the 10,000 military stationed there.
I couldn’t
learn enough, quick enough back then. Lean and Six Sigma were brand new
concepts and barely discussed at that time. The military taught us whatever we
needed to know, so certification back then wasn’t a concern. When I retired
from the military in 2008, I almost immediately went to work for Booz | Allen |
Hamilton, a top ten management consulting firm in the nation. I was a Lead
Associate in the Strategy and Organization functional department of Booz Allen.
This was a evolutionary opportunity, and in three years I learned a great deal
about all things operational excellence.
From there, I
moved to United Services Automobile Association (USAA). Over seven years, I led
the engineering of four enterprise programs (document management, process
excellence, banking, and human resources). In 2019, I left USAA and went to
work full-time in my own business. This eventually led me to a Chief Operating
Officer position and then Gemba Academy.
My passion is fueled
by success – I’ve adopted the moniker, “Success Incubator.” Lean, and all
things Operational Excellence, fuels success for people and businesses. I’m a
student of not knowing what I don’t know, which fuels my curiosity for
continual learning and application of everything there is to know about this
wonderfully-deep subject.
3. In your
opinion what is the most powerful aspect of lean?
Lean, and
process improvement itself, provides a no nonsense approach to improving
anything. Conceptually, data-driven decision making, respect for people, and
going to where the work is done are basic concepts of success in anything. If
you own a business and you delegate these activities to others, you will fail.
4. In your
opinion what is the most misunderstood or unrecognized aspect of lean?
The biggest
problem is trying to solve everything at once. The whole emphasis of process
improvement is to sift through all the noise of the symptoms and causes to get
to the root cause – that Red Thread, which if you pull will make a major impact
on your process. Instead, we brainstorm and diagram our way to a list of causes
and fail to narrow them down to a singular focus – fix one thing at a time. The
inherent basis of Lean is to standardize, measure, and then take a single step
up, improving one thing. Then, we standardize and measure again. This is what
continuous improvement is all about.
The problem
with trying to chase all the symptoms and causes at once is that process
improvement efforts take way too long! Business owners, expecting immediate and
measurable returns do not see results. The effort is seen as a waste, and the
entire effort is killed before it’s finished.
5. In your
opinion what is the biggest opportunity for lean in today's world? How can that
be accomplished?
I recently saw
an article where Toyota is teaching young kids how to work on automobiles. I
watched a video of young girls taking apart an engine. We need to evolve our
education system to teach problem solving, process improvement, and process
management in schools. Lean and Six Sigma certifications shouldn’t be a coveted
designation, it should be the foundation of business existence. These are
business transferable skills that should be taught to everyone in school.
Through
their answers to these questions hopefully you will get a sense of the thinking
behind those who are shaping the Lean landscape. I continue to keep
learning and thankfully with the willingness of these practitioners to share I
am positive you will, too.

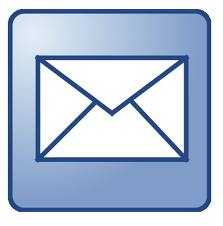




