A few weeks ago
I sat down with Michelle Bangert, Managing Editor, for a podcast to
introduce the article.
Michelle:
So much has changed with lean and Kaizen, but is there anything you think today
that quality professionals should know about Kaizen?
Tim: Yeah, I
think it's a really valuable tool. Probably not enough companies do that. I
think it's kind of a concept that maybe is foreign to a lot of people, but it's
really just an improvement idea that allows us to get a group of people
together, continually look at opportunities for improvement. So if you want to
be able to look at your process, if you want to uncover what maybe is, it pains
you, if you want to be able to do that, these are the kinds of things that
Kaizen allows you to do. So it allows us to challenge the status quo, things
that we take for granted, get the right people in the right room and come up
with a new process to do things better, more efficiently in the future.
Michelle:
I love that you said, if it ain't broke, don't fix it policy. It's still, let's
keep fixing things and make it better because someone's doing that. And so we
have to keep up. So that was very smart. That's probably the better way.
Definitely. So can you remember the first time you were involved in a Kaizen
event or one of the early ones you did?
Tim: Yeah, one
of the earliest ones I probably did was on the shop floor. You know, I think
there's a difference between doing it in the office and doing it on the shop
floor. And certainly on the shop floor, you can do things that are physically
transformational, you can pick up the machinery of the cell and move it around.
So those are very exciting. So I did a Kaizen event that was around changing
the physical layout. So we did things that were very, I guess, traditional
where you might pass the product along to an area. And we wanted to do a change
where we would consolidate the footprint of the cell and do more U-shaped
manufacturing cell and parts would be provided from the back of the cell and
you would do a certain amount of the work content and you would pass it to the
next operation instead of what was more traditional manufacturing. So that was
the first Kaizen I ever did and I think you know you probably can read lots of
stories online about the U-shaped cells and doing that kind of configuration.
But for small piece parts, that's a very common approach to do that. But
different than you might tackle in the office, first office guys than I ever
did was a value stream mapping activity. Typically in the office, you can't see
the waste, the same that you might see in a factory. So you have to map out the
processes and you might walk it visually. You pick a process and try to walk
that from a customer standpoint and understand all the processes that occur
there. So typically a value stream map might be a way to do that technique.
Michelle:
Definitely a lot of value, regardless of which approach you're doing. Makes
sense. Can you think of any that were especially memorable, whether in a good
way or a bad way where one worked really well or maybe didn't work the way you
wanted?
Tim: I think
the ones that are most memorable are the ones that I think people say that
something couldn't occur there or somebody might be challenging. So certainly
when I was at wire mold, we had that Kaizen area that They said the group
leader was really resistant to change and you know this couldn't be done and I
took it as a personal challenge to see what we could do there. So I think
people felt that somebody was adversarial there. The group leader was somebody
that was against change and it really wasn't the case. It was trying to get to
understand like, where they came from. And it wasn't that they were against
continuous improvement. They actually had suggested lots of ideas for
improvement. They didn't want to be changed. They wanted to be heard. So I went
in there with the tact of, well, why don't you just try it, you know. If I
prove me wrong kind of mentality, right? You know, let's just try it this way.
If I'm wrong, then, you know, but then, you know, so be it. We'll try it your
way. So I always took that mentality, like try to listen to what they have to
say, because they're making the product. I'm certainly not the expert in making
the product. And so if you can get them to listen to what you have to say, and
you can listen to what they have to say, generally that compromise will get you
a solution in the long run. But I was able to get their ideas incorporated in
the design. Obviously, it's a much better Kaizen that way. That one success led
to three or four different Kaizens in that area, and we were able to make
significant change that way. But I like it when someone says that we can't do
it, or that they're really against continuous improvement. Those are the
challenges.
Listen to the
rest of the interview here:

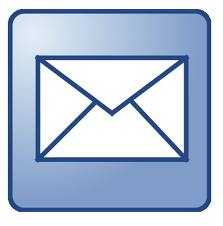




