Strategy is not about doing the important things but rather the process of choosing and deciding the plan forward.
![]() |
Image Source: Morsa Images / E+ / Getty Images Plus |
Traditional planning methodologies focus on steering an organization in the direction desired by top management, often referred to as management by objective (MBO). Unfortunately, as we know, you can’t achieve the desired results by just dictating individual targets.
Companies must determine ahead of time what the vision and direction will be. A proper strategy must assign clear responsibilities and show what resources are to be committed. Metrics and timelines must be defined. Management must decide what core elements are to be deployed and when.
Strategy deployment is the system for setting management’s compass toward True North. It is a tool to align people, activities, and performance metrics with strategic priorities. It enables members of the organization to work together in the most creative way to achieve the strategic intent.
Strategy is not about doing the important things but rather the process of choosing, the responsibility of leaders to grasp the situation and decide the plan forward. I always tell others that strategy deployment is a focusing mechanism. This is about sharpening your focus by selecting the vital few breakthrough objectives. The job of management is to steer towards those priorities that will bring the organization into alignment with customer demands.
To learn more about creating a strategic plan, aligning employees to execute, and how to check and adjust as needed head over to Quality Magazine's publication "Strategy Planning and Deployment: A Tool to Achieve Excellence."

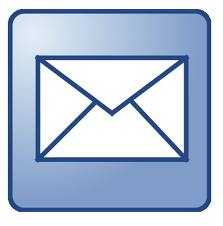




