One of the
greatest and most important challenges of project management is communicating
clearly with your team about both the details and the big picture of your
project. After all, it’s unlikely people will work on the right things in the
right order if they don’t understand how each task– and its timely completion–
contributes to the success of the project. One of the best ways to communicate with your team is via
visual project management.
Visual project
management is a method by which you can organize and visualize process over
traditional projects and utilizing tools to help everyone involved visualize
the status and needs of the project.
There are many
benefits of visual management:
- Save time by simplifying the
complex – Visual management helps people understand complex
information at a glance, like what work items should be prioritized and
who should be working on them.
- Reduce waste by communicating
effectively – Take the guesswork out of teamwork by having a shared,
common view of all work being done across the team.
- Overcome impediments to flow –
See where work has slowed or stopped by creating a Lean visual management
board that enables you to see bottlenecks and blockers.
- Collaborate and improve –
Instead of pushing work blindly into team members’ queues, you can move
work through our team process with a better understanding of capacity.
This enables teams to collaborate in a healthier, more productive way.
Visual project
management tools help bring the information to life, connecting the dots and
painting a clear picture of the desired outcome, the current status, and any
roadblocks that may be in the way. Visual management becomes a language that
everyone can understand and explain.
A visual
management board can help see the big picture, structure project activities,
monitor and improve a team’s performance. Having a project board showing all
the project tasks, their stage in the project life at any given moment can help
significantly improve communication between team members.
More
specifically, it enables the team to visualize the system, become aware of any
constraints or roadblocks that might result, and begin a dialog on how to solve
those problems. In this way, the challenges are directed to the system and how
to solve versus focusing on the person as the issue. While there are many
methods for collaborative communications, several common tools to foster the
collaboration include consensus decision-making, A3s, Daily Huddles and similar
problem solving activities.
Managing your
tasks and overall projects require more than placing them in a sequence and
attaching specific timelines to them. You need to adopt a better way to make
your workflow transparent so you can continuously optimize your process and
evolve it to create superior value for your customers.

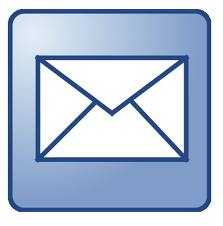




