If you want to continuously improve your skills you need to close the learning loop with feedback. James Ottaway, a passionate software developer for ThoughtWorks, has a strong desire to continuously improve his skills. In the following video he shares his personal continuous improvement process and experience.
This is a good lesson for all those who coach employees in the Gemba. I think it is good to be able to give and receive feedback. Remember the two important aspects of feedback is strengthen confidence and improve effectiveness. Be curious, continuously improve, and look for support are key lessons to apply in anything you do.
Feedback?
Stay connect to A Lean Journey on our Facebook page or LinkedIn group.
Follow me on Twitter or connect with me on Linkedin.
You can also subscribe to this feed or email to stay updated on all posts.
Thursday, July 28, 2011
Wednesday, July 27, 2011
Daily Lean Tips Edition #17
For my Facebook fans you already know about this great feature. But for those of you that are not connected to A Lean Journey on Facebook or Twitter I post daily a feature I call Lean Tips. It is meant to be advice, things I learned from experience, and some knowledge tidbits about Lean to help you along your journey. Another great reason to like A Lean Journey on Facebook.
Stay connect to A Lean Journey on our Facebook page or LinkedIn group.
Follow me on Twitter or connect with me on Linkedin.
You can also subscribe to this feed or email to stay updated on all posts.
Click this link for A Lean Journey's Facebook Page Notes Feed.
Here is the next addition of tips from the Facebook page:
Lean Tip #241 – Leaders must teach by example to transform a culture.
To get people across an organization to systematically work on improvement every day requires teaching the skills behind the solution. And for that to happen, their leaders and mangers also need to practice and learn those skills.
To get people across an organization to systematically work on improvement every day requires teaching the skills behind the solution. And for that to happen, their leaders and mangers also need to practice and learn those skills.
Lean Tip #242 – Developing people means going beyond challenging people.
Developing people means challenging people. But just issuing challenges isn’t enough. It would be disrespectful to not also teach a systematic, common means of developing solutions and meeting those challenges.
Developing people means challenging people. But just issuing challenges isn’t enough. It would be disrespectful to not also teach a systematic, common means of developing solutions and meeting those challenges.
Lean Tip #243 – The purpose of coaching is an interaction not an audit.
The learner should know when the coach is coming and what he/she will ask. They can prepare the information in advance of the coaching cycle. The purpose is not to control or get people to do what they say. There should be a genuine interest in both parties in what you are trying to achieve, what you are learning, and what will be the next experiment.
The learner should know when the coach is coming and what he/she will ask. They can prepare the information in advance of the coaching cycle. The purpose is not to control or get people to do what they say. There should be a genuine interest in both parties in what you are trying to achieve, what you are learning, and what will be the next experiment.
Lean Tip #244 – Once you have a target condition don’t think too far ahead.
One you have a target condition, relax and focus on the next step. Put your emphasis on the next step, because what you learn there may influence the step after that. You’ll only see the full path in hindsight. And you’re probably not going to be taking the most direct route to the target condition either.
One you have a target condition, relax and focus on the next step. Put your emphasis on the next step, because what you learn there may influence the step after that. You’ll only see the full path in hindsight. And you’re probably not going to be taking the most direct route to the target condition either.
Lean Tip #245 – A Target is not the same as a Target Condition.
A target is an outcome, while a target condition is a description of a process operating in a way, in a pattern, that we predict will result in the desired outcome. A target condition enables teamwork. It’s not so much my idea vs your idea. It’s more about what we need to work on to get there.
A target is an outcome, while a target condition is a description of a process operating in a way, in a pattern, that we predict will result in the desired outcome. A target condition enables teamwork. It’s not so much my idea vs your idea. It’s more about what we need to work on to get there.
Lean Tip #246 - Mapping your processes will help you understand the actual condition.
To gain control over your processes, you must understand the “three actuals”:
- The actual place or location in which a process occurs
- The actual employees working in that location
- The actual process in that location
Mapping the processes will help you understand all three actuals.
To gain control over your processes, you must understand the “three actuals”:
- The actual place or location in which a process occurs
- The actual employees working in that location
- The actual process in that location
Mapping the processes will help you understand all three actuals.
Lean Tip #247 – When creating a value stream map take a tour from end-to-end of the flow with out prejudice.
Conduct a quick tour of the value stream to view end-to-end material and information flows, making sure that you have identified all the component flows. Remember to record exactly what you see without making any judgments. Don’t waste time debating the merits of an activity or its proper sequence; just record what is happening.
Conduct a quick tour of the value stream to view end-to-end material and information flows, making sure that you have identified all the component flows. Remember to record exactly what you see without making any judgments. Don’t waste time debating the merits of an activity or its proper sequence; just record what is happening.
Lean Tip #248 – Use quick-changeover methods to reduce your set-up costs and batch sizes.
By reducing changeover times, you company will be able to run smaller batch sizes and free up production capacity. If being able to offer a mix of products and services is important, then quick changeover will reduce the number of operations you need to run every day, week, or month.
By reducing changeover times, you company will be able to run smaller batch sizes and free up production capacity. If being able to offer a mix of products and services is important, then quick changeover will reduce the number of operations you need to run every day, week, or month.
Lean Tip #249 – Use error-proofing techniques to ensure that no product defects are being passed on to downstream operations.
The goal of error proofing is to create an error-free production environment. A Lean enterprise strives for quality at the source. This means that any defects that occur during one operation in a manufacturing or business process should never be passed on to the next operation. This ensures that your customers will receive only defect-free product or services.
The goal of error proofing is to create an error-free production environment. A Lean enterprise strives for quality at the source. This means that any defects that occur during one operation in a manufacturing or business process should never be passed on to the next operation. This ensures that your customers will receive only defect-free product or services.
Lean Tip #250 – Zero defects is an achievable goal!
Many organizations have attained this level of error proofing, One of the largest barriers to achieving it is the belief that it can’t be done. By changing this belief among your employees, you can make zero defects a reality in your organization.
Many organizations have attained this level of error proofing, One of the largest barriers to achieving it is the belief that it can’t be done. By changing this belief among your employees, you can make zero defects a reality in your organization.
Lean Tip #251 – Effective problem solving requires good understanding of the problem and the current situation.
The first step in problem solving is to be certain you have a good understanding of the current situation. To ensure your solutions get to the root cause, you must understand the process where the problem initially occurred. When starting to diagnose a problem, don’t rely on verbal reports to provide the details. Go to the work area, observe the situation, solicit help from the people in the area, and collect hard evidence for yourself. Gathering the facts first hand will help you gain a better understanding of the problem which, in turn, will allow you to better focus your solutions.
The first step in problem solving is to be certain you have a good understanding of the current situation. To ensure your solutions get to the root cause, you must understand the process where the problem initially occurred. When starting to diagnose a problem, don’t rely on verbal reports to provide the details. Go to the work area, observe the situation, solicit help from the people in the area, and collect hard evidence for yourself. Gathering the facts first hand will help you gain a better understanding of the problem which, in turn, will allow you to better focus your solutions.
Lean Tip #252 – Source inspection and mistake proofing are needed to achieve zero defects.
To achieve zero defects, both source inspection and mistake proofing are needed. Remember that, although it is necessary to have efficient inspection operations, they are of little value to the process. Even the most efficient inspection operations are merely efficient forms of waste.
To achieve zero defects, both source inspection and mistake proofing are needed. Remember that, although it is necessary to have efficient inspection operations, they are of little value to the process. Even the most efficient inspection operations are merely efficient forms of waste.
Lean Tip #253 – Empower operators to stop the production line whenever a defect is detected.
Wherever practical, empower operators to stop the production line whenever a defect is detected. This creates a sense of urgency that focuses employees’ energy on prevention of the defect’s recurrence. It also creates the need for the effective source inspections and self-inspections.
Wherever practical, empower operators to stop the production line whenever a defect is detected. This creates a sense of urgency that focuses employees’ energy on prevention of the defect’s recurrence. It also creates the need for the effective source inspections and self-inspections.
Lean Tip #254 – Don’t let and error-proofing device sit idle.
This happens all too often when people override sensors, disconnect them, or ignore them. If your employees are tempted to disconnect an error-proofing device, then install an error-proofing device for the error-proofing device. It is likely that the device needs some improvement to make it effective.
This happens all too often when people override sensors, disconnect them, or ignore them. If your employees are tempted to disconnect an error-proofing device, then install an error-proofing device for the error-proofing device. It is likely that the device needs some improvement to make it effective.
Lean Tip #255 – Always use data as the basis for making adjustments in your processes.
Always use data as the basis for making adjustments in your processes. Using subjective opinion or intuition to make adjustments can result in errors – and eventually defects. Data also ensures that the adjustment was effective or not.
Always use data as the basis for making adjustments in your processes. Using subjective opinion or intuition to make adjustments can result in errors – and eventually defects. Data also ensures that the adjustment was effective or not.
Stay connect to A Lean Journey on our Facebook page or LinkedIn group.
Follow me on Twitter or connect with me on Linkedin.
You can also subscribe to this feed or email to stay updated on all posts.
Tuesday, July 26, 2011
Lean is the Means to be Green
Last week I had the pleasure of writing an article for Enna's newsletter. Enna is a developer and manufacturer of innovative, action-oriented training / workshop training packages developed for internally led process improvement initiatives. If you don't subscribe to their newsletter you can read it below.
Many manufacturers know the benefits of lean manufacturing: higher productivity, better quality, reduced cycle time, plus enhanced employee engagement. Lean is excellent at marshaling different groups and individuals into a high performing team focused on rooting out waste.
A Lean organization is commonly characterized by the elimination of the following seven wastes (Ohno’s wastes):
In recent years many companies have established a fundamental goal to minimize the environmental impact while maintaining high quality and service for all business processes and products. This is commonly referred to as sustainability or green manufacturing. According to the Department of Commerce, “Sustainable manufacturing is the creation of manufactured products that use processes that minimize negative environmental impacts, conserve energy and natural resources, are safe for employees, communities, and consumers and are economically sound.”
As most manufacturers are starting to realize, the quest to become green takes them right back to Lean. Applying ‘Lean Principles’ – a systematic approach to identifying and eliminating waste through continuous improvement - is one of the key ways to enhance environmental performance.
Lean and sustainability are conceptually similar. Both seek to maximize the efficiency of a system. This is accomplished through waste and time minimization. The difference lies in where this system (or process) boundary is drawn and how, and in how waste is defined. Lean sees waste as non-value added to the customer; green sees waste as extraction and consequential disposal of resources at rates or in forms beyond that which nature can absorb.
When companies expand the definition of waste to include not only product and process waste, but also the business consequences of unsustainable practices, Ohno’s list of wastes takes a different form:
Many manufacturers know the benefits of lean manufacturing: higher productivity, better quality, reduced cycle time, plus enhanced employee engagement. Lean is excellent at marshaling different groups and individuals into a high performing team focused on rooting out waste.
A Lean organization is commonly characterized by the elimination of the following seven wastes (Ohno’s wastes):
- Waste of overproduction (waste from faster than necessary pace);
- Waste of waiting;
- Waste of transport (conveyance);
- Waste from inappropriate processing;
- Waste due to unnecessary inventory (excess inventory);
- Waste due to unnecessary motion; and
- Waste due to defects.
In recent years many companies have established a fundamental goal to minimize the environmental impact while maintaining high quality and service for all business processes and products. This is commonly referred to as sustainability or green manufacturing. According to the Department of Commerce, “Sustainable manufacturing is the creation of manufactured products that use processes that minimize negative environmental impacts, conserve energy and natural resources, are safe for employees, communities, and consumers and are economically sound.”
As most manufacturers are starting to realize, the quest to become green takes them right back to Lean. Applying ‘Lean Principles’ – a systematic approach to identifying and eliminating waste through continuous improvement - is one of the key ways to enhance environmental performance.
Lean and sustainability are conceptually similar. Both seek to maximize the efficiency of a system. This is accomplished through waste and time minimization. The difference lies in where this system (or process) boundary is drawn and how, and in how waste is defined. Lean sees waste as non-value added to the customer; green sees waste as extraction and consequential disposal of resources at rates or in forms beyond that which nature can absorb.
When companies expand the definition of waste to include not only product and process waste, but also the business consequences of unsustainable practices, Ohno’s list of wastes takes a different form:
- Waste of natural resources
- Waste of human potential
- Waste due to emissions
- Waste from byproducts (reuse potential)
- Terminal waste, waste from by-products that have not further usefulness
- Energy waste
- Waste of the unneeded (e.g., packaging)
When the definition of waste is expanded and when it’s understood that the consequences of corporate decisions extend past the company parking lot, Lean can indeed be green. Less waste is good for the environment — and the company’s bottom line — and reducing waste in both products and processes is what Lean is all about. So it makes perfect sense that in order to achieve higher levels of environmental performance, your organization must first adopt the principles and practices of lean manufacturing.
Lean manufacturing practices, which are at the very core of sustainability, save time and money — an absolutely necessity in today’s competitive global marketplace. While the pursuit of Green and Lean is not a destination but a journey it is clear that organizations that stretch themselves to build a culture around the values of Sustainability, Excellence, and Equity will ultimately have a big advantage those who do not. Isn’t the ultimate definition of “sustainable manufacturing” to be able to compete and not only survive, but thrive?

Lean manufacturing practices, which are at the very core of sustainability, save time and money — an absolutely necessity in today’s competitive global marketplace. While the pursuit of Green and Lean is not a destination but a journey it is clear that organizations that stretch themselves to build a culture around the values of Sustainability, Excellence, and Equity will ultimately have a big advantage those who do not. Isn’t the ultimate definition of “sustainable manufacturing” to be able to compete and not only survive, but thrive?

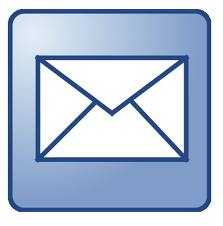





Monday, July 25, 2011
The Top Ten Reasons to Like A Lean Journey Facebook Page
I have had a Facebook fan page since May of 2010 and the number of fans continues to grow each month. In a sort of self-fulfilling plug, I thought I would talk about the value of A Lean Journey Facebook Page. Here are the top 10 reasons to be a fan of this page:
10. There are over 500 million active Facebook users and over 50% of the user’s login every day. This means you are already likely where all the information is.
9. Facebook is a great place to distribute information including events, photographs, videos, articles, and of course blog posts.
8. Facebook makes it very easy to share information with your network that you find valuable furthering the discussion.
7. The use of question, polls, and discussion sections in Facebook make it a great place to interact with like-minded thinkers.
6. I frequently posts articles of interest regarding Lean, productivity, management, and continuous improvement. This helps contribute to our need for continuous learning.
5. All my Slide Share presentations are linked to the Facebook page for easy access. As new presentations are updated like that of webinars that Jeff Hajek and I do you can stay informed.
4. If you’re not on Twitter (or if you are) and you still want to stay part of the conversation you can access all the tweets on the Facebook page.
3. In a new series I post the Photo of the Week which is meant to highlight a Lean principle or share a best practice. When it comes to learning a picture is worth a 1000 words.
2. All the blog posts feeds are picked up in Facebook so you can be aware of new posts are they occur.
And the #1 reason
1. Every week day I post a series called Daily Lean Tips. It consists of a thought followed by some brief explanation. The point of the tip is to stimulate some thinking around the topic. This has become a very popular series on Facebook.
So if you are not a fan of A Lean Journey Facebook Page yet then you are certainly missing out on lots of great content. Get connected today.
Stay connect to A Lean Journey on our Facebook page or LinkedIn group.
Follow me on Twitter or connect with me on Linkedin.
You can also subscribe to this feed or email to stay updated on all posts.
Friday, July 22, 2011
Lean Quote: It's About The Journey and Sometimes It Starts With Failure
On Fridays I will post a Lean related Quote. Throughout our lifetimes many people touch our lives and leave us with words of wisdom. These can both be a source of new learning and also a point to pause and reflect upon lessons we have learned. Within Lean active learning is an important aspect on this journey because without learning we can not improve.
Ever hear of Erik Weihenmyer? Despite losing his vision at the age of 13, Erik Weihenmayer has become one of the celebrated and accomplished athletes in the world. On May 25, 2001, Erik reached the top of Everest and stood at 29,035 feet. He was the first blind person to summit Everest. At the age of 34, Erik became one of less than 100 individuals to climb all of the Seven Summits - the highest peaks on each of the seven continents. He completed this incredible accomplishment on September 5, 2002 when he stood on top of Mt. Kosciusko in Australia. Pretty amazing, don’t you think? We know for a fact that Erik “saw” the goal in his mind and in his heart – we know this because he is blind!
Erik is an example of not accepting failure or letting his challenges get the best of him. Failure is not shameful. On the contrary, it is part of the learning process. It helps us discover things we couldn’t discover otherwise. For instance, we set a goal and we take steps to achieve the goal. If we reach the goal, we’ve succeeded. If we stopped taking the steps we needed to take to achieve the goal then we failed because we’re quitters, something to be ashamed of. If we take all of the necessary steps and still don’t achieve the goal then we failed because we couldn’t make it happen, and we feel ashamed. Most successes will be preceded by a series attempts that didn’t quite produce the results we were hoping for.
Here are some other examples of people who stayed the course and never gave up:
If we allow ourselves to become discouraged during the learning process we may give up right before we reach our goal. Anytime we learn from our efforts we are in the process of succeeding. Each lesson brings us closer to our intended result.
Stay connect to A Lean Journey on our Facebook page or LinkedIn group.
Follow me on Twitter or connect with me on Linkedin.
You can also subscribe to this feed or email to stay updated on all posts.
"Success is not just the crowning moment, the spiking of the ball in the end zone or the raising of the flag on the summit. It is the whole process of reaching for a goal and, sometimes, it begins with failure." — Erik Weihenmayer; blind climber, motivational speaker, author
Ever hear of Erik Weihenmyer? Despite losing his vision at the age of 13, Erik Weihenmayer has become one of the celebrated and accomplished athletes in the world. On May 25, 2001, Erik reached the top of Everest and stood at 29,035 feet. He was the first blind person to summit Everest. At the age of 34, Erik became one of less than 100 individuals to climb all of the Seven Summits - the highest peaks on each of the seven continents. He completed this incredible accomplishment on September 5, 2002 when he stood on top of Mt. Kosciusko in Australia. Pretty amazing, don’t you think? We know for a fact that Erik “saw” the goal in his mind and in his heart – we know this because he is blind!
Erik is an example of not accepting failure or letting his challenges get the best of him. Failure is not shameful. On the contrary, it is part of the learning process. It helps us discover things we couldn’t discover otherwise. For instance, we set a goal and we take steps to achieve the goal. If we reach the goal, we’ve succeeded. If we stopped taking the steps we needed to take to achieve the goal then we failed because we’re quitters, something to be ashamed of. If we take all of the necessary steps and still don’t achieve the goal then we failed because we couldn’t make it happen, and we feel ashamed. Most successes will be preceded by a series attempts that didn’t quite produce the results we were hoping for.
Here are some other examples of people who stayed the course and never gave up:
If we allow ourselves to become discouraged during the learning process we may give up right before we reach our goal. Anytime we learn from our efforts we are in the process of succeeding. Each lesson brings us closer to our intended result.
Stay connect to A Lean Journey on our Facebook page or LinkedIn group.
Follow me on Twitter or connect with me on Linkedin.
You can also subscribe to this feed or email to stay updated on all posts.
Thursday, July 21, 2011
Lean, What's in a Name From Those Who Label It
The Willington Companies is a local company that I interact with in our Lean Network. They are a family owned business in Connecticut using Lean manufacturing to stay competitive and grow their business. The Willington Companies have been a great example of Lean manufacturing in the last few years. They recently published a video from the employees at the company that I feel really defines Lean very well.
Do you think the Willington Companies get the true meaning of Lean?
Do you think the Willington Companies get the true meaning of Lean?

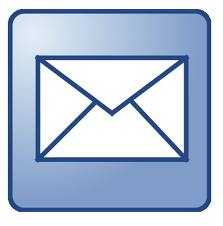





Tuesday, July 19, 2011
Guest Post: What Could Be Easier? The 4 Step Deming Cycle

Plan - Do - Check - Act
That's not asking a lot, is it? You have just implemented a big change that should save your company a lot of time and money. A little follow-up to make sure everything is going as planned is common sense. What could be easier than to check to see how it's going, right?
Then why is it that so many leaders get caught in the Silly Cycle?
We have all been there. It seems that there are more and more demands placed on manufacturing plants every day. The same is true for other work places. Not only are today's leaders expected to do more with less. They are also expected to do it better, faster, and cheaper than last year. Sound familiar? It's no wonder that it's difficult to find time to properly plan and even harder to follow through on everything that crosses a leader's desk. But if you don't plan and you don't follow-up, all you do is Do, Do, and Do.
This really is not a new problem. While I believe that these are particularly tough times, leaders have always been challenged to do it better, faster, and cheaper.
In fact, the Plan - Do - Check - Act cycle goes back to the 1930's when Walter Shewhart developed PDCA. Dr. Edwards Deming made it famous with his work in the 1950's. While the PDCA is often called the Deming Cycle, he referred to it as the Shewhart cycle.
While it isn't easy to find the time, following the PDCA cycle will yield better results and sustained improvements. The basic steps are:
Plan: Define, measure, and analyze. Define the scope of the project. Assess the current state. Measure and benchmark so you know where you are starting. Analyze the root causes and consider your options.
Do: Implement your plan. Over communicate. Start with a pilot or test area. That way you can learn lessons from the implementation on a small-scale. No matter how easy your idea sounds, there will probably be some unexpected issues.
Check: Follow up on the results. See if the plan is being implemented as you expected. Get feedback to see how the plan can be improved.
Act: Standardize your improvements. Plan for Continuous Improvement. Build systems so that the improvements can be sustained.
Taking the time to plan, check, and act will pay dividends. You have already seen where skipping those steps takes you. You don't have time to solve everything today. Pick one and start there. What issues are you dealing with today that warrant a PDCA?
Stay connect to A Lean Journey on our Facebook page or LinkedIn group.
Follow me on Twitter or connect with me on Linkedin.
You can also subscribe to this feed or email to stay updated on all posts.
Subscribe to:
Posts (Atom)