For my Facebook fans you already know about this great feature. But for those of you that are not connected to A Lean Journey on Facebook or Twitter I post daily a feature I call Lean Tips. It is meant to be advice, things I learned from experience, and some knowledge tidbits about Lean to help you along your journey. Another great reason to like A Lean Journey on Facebook.

Click this link for A Lean Journey's Facebook Page Notes Feed.
Here is the next addition of tips from the Facebook page:
Lean Tip #391 – Don’t Expect Training to Make Lean Happen
You need to change the system. Recall Deming’s 94/6 rule whereby 94% of the problems stem from the system – that only management can fix, and only 6% from operators. Change cannot come purely from the bottom.
You need to change the system. Recall Deming’s 94/6 rule whereby 94% of the problems stem from the system – that only management can fix, and only 6% from operators. Change cannot come purely from the bottom.
Lean Tip #392 – Don’t Declare Victory Too Soon
After the first battles have been won, the results will come in, and there will be temptation to declare the war over. But remember, it takes seconds to change behavior, but it takes years to change attitude. The changes need to sink in deeply in the company’s culture in order to be sustained.
After the first battles have been won, the results will come in, and there will be temptation to declare the war over. But remember, it takes seconds to change behavior, but it takes years to change attitude. The changes need to sink in deeply in the company’s culture in order to be sustained.
Lean Tip #393 – Remove Obstacles to Create Transformation
Transformations frequently hit large obstacles that management must move out of the way. Make sure that there is a way for employees to communicate upwards that these obstacles need to be moved.
Transformations frequently hit large obstacles that management must move out of the way. Make sure that there is a way for employees to communicate upwards that these obstacles need to be moved.
Lean Tip #394 – Create Short Term Wins so You Don’t Lose Momentum
Transformations take time, so in order not to lose momentum make sure you put in place short term goals, and celebrate their achievement. People need to see compelling evidence of change that the new journey is producing results, otherwise they will lose in confidence.
Transformations take time, so in order not to lose momentum make sure you put in place short term goals, and celebrate their achievement. People need to see compelling evidence of change that the new journey is producing results, otherwise they will lose in confidence.
Lean Tip #395 – Successful Change Needs Facilitation
The lack of recognizing the need of full time facilitation is a common problem with poor Lean implementations. Most companies will need a Lean sensei to keep the momentum going.
The lack of recognizing the need of full time facilitation is a common problem with poor Lean implementations. Most companies will need a Lean sensei to keep the momentum going.
Lean Tip #396 – Culture is about “Current Behavior”
Culture is something that you learn day by day, not by going on an onward bound course or by reading a book about moving cheese. “Act into a new way of thinking” not “Think into a new way of acting.”
-Peter Scholtes, The Leaders Handbook
Culture is something that you learn day by day, not by going on an onward bound course or by reading a book about moving cheese. “Act into a new way of thinking” not “Think into a new way of acting.”
-Peter Scholtes, The Leaders Handbook
Lean Tip #397 – Lean may involve revolutionary change but culture change is evolutionary.
Although Lean often involves revolutionary change, culture change is evolutionary. Day by day. And because, inevitably, managers leave, coaching future managers on their attitudes to, and interactions with, subordinates needs to be continually done. Arguably, there is no more important a task.
Although Lean often involves revolutionary change, culture change is evolutionary. Day by day. And because, inevitably, managers leave, coaching future managers on their attitudes to, and interactions with, subordinates needs to be continually done. Arguably, there is no more important a task.
Lean Tip #398 – It is not about the tools but rather how they are applied.
A large number of organizations have failed to produce the desired results from the direct and prescriptive application of Lean tools. The tools themselves have been proven to work in many situations. The difference must then be in how the tools were applied, their appropriateness, but not the tools themselves.
A large number of organizations have failed to produce the desired results from the direct and prescriptive application of Lean tools. The tools themselves have been proven to work in many situations. The difference must then be in how the tools were applied, their appropriateness, but not the tools themselves.
Lean Tip #399 – Lean is a system of tools and people that need to work together.
Lean is a system of tools and people that need to work together. A single tool by itself, like 5s or value stream mapping, is likely to fail because its benefits are likely to be marginal or even negative.
Lean is a system of tools and people that need to work together. A single tool by itself, like 5s or value stream mapping, is likely to fail because its benefits are likely to be marginal or even negative.
Lean Tip #400 – Don’t underestimate the importance of a feeling of success.
People feel happier and perform better when there is a feeling of success. And vice versa. And attitude drives performance. There is a feedback loop. So managers must project confidence. War leaders know this well.
People feel happier and perform better when there is a feeling of success. And vice versa. And attitude drives performance. There is a feedback loop. So managers must project confidence. War leaders know this well.
Lean Tip #401 – When preparing for flow first consider the demand
Understanding demand should be the first, or at least a very early, too to use with Lean implementation. Listen to what customers are actually saying or requesting.
Understanding demand should be the first, or at least a very early, too to use with Lean implementation. Listen to what customers are actually saying or requesting.
Lean Tip #402 – Make a video of tasks.
When establishing activity timing and work elements make a video of the tasks. This is better than a live recording, because it allows backtracking, and slow motion. It also avoids the stress of several people with stopwatches standing over an operator.
When establishing activity timing and work elements make a video of the tasks. This is better than a live recording, because it allows backtracking, and slow motion. It also avoids the stress of several people with stopwatches standing over an operator.
Lean Tip #403 – Visual management is the ‘litmus test’ for Lean.
If you go into any operation and find that schedules, standard work, the problem solving process, quality and maintenance are not immediately apparent, and up to date, there is an excellent chance that the operation is far off Lean.
If you go into any operation and find that schedules, standard work, the problem solving process, quality and maintenance are not immediately apparent, and up to date, there is an excellent chance that the operation is far off Lean.
Lean Tip #404 – Use the smallest machines possible consistent with quality requirements.
Having several smaller machines instead of one bigger, faster ‘monument’ allows greater flexibility in layouts, easier scheduling, reduction in material handling, less vulnerability to breakdown, less vulnerability to bottleneck problems, possibly reduced cost, and through phasing of machine acquisition, improved cash flow and more frequent technology updates.
Having several smaller machines instead of one bigger, faster ‘monument’ allows greater flexibility in layouts, easier scheduling, reduction in material handling, less vulnerability to breakdown, less vulnerability to bottleneck problems, possibly reduced cost, and through phasing of machine acquisition, improved cash flow and more frequent technology updates.
Lean Tip #405 – The prime reason for automation in Lean is for quality.
The principle is not to automate waste. Ask whether a low cost solution is possible like a gravity-feed rather than a robot. Good reasons for automation are dull, dirty, dangerous and hot, heavy, hazardous work. Another good reason is reduction in variation. A bad reason is to reduce people. Remember, machines, don’t make improvement suggestions.
The principle is not to automate waste. Ask whether a low cost solution is possible like a gravity-feed rather than a robot. Good reasons for automation are dull, dirty, dangerous and hot, heavy, hazardous work. Another good reason is reduction in variation. A bad reason is to reduce people. Remember, machines, don’t make improvement suggestions.

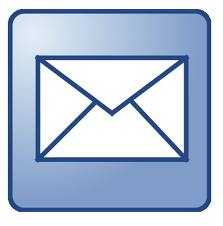




