Last week I
spent a couple days at The 11th
Annual Northeast Shingo Prize Conference in Springfield, MA. The wonderful conference hosted by GBMP was
an exhilarating learning experience for me so I thought I would share some of
those nuggets with you.
The first
presentation was from my friend Dan Markovitz about his new
book Building
a Fit Organization. Everyone knows that in order to reach optimum levels of
health, you have to exercise―and that you have to keep at it, day after day
after day. No big secret here. It’s the same with process improvement,
and, specifically, lean processes.
Key
principles include of improving your organization along the fitness analogy:
1)
Committing
to Fitness/ Improvement
a. The coach/leader needs to how to drive
out fear
b. Spirit – i.e. Paul Akers 2 second lean,
Improve yourself every day
2)
Don’t
focus on weight loss (waste) focus on strength/power/ fitness (value creation).
a. Don’t focus on cost cutting
3)
Think
Horizontal not vertical (training for a specific event) (focus on end goal)
a. Think of the end result, what does your
customer need
b. The value stream map is the tool that
gets you there
4)
The
Right way to do things (Standard work)
a. There is a right way to train for the
event, don’t get caught up in the chaos.
b. Focus on what is important and not in adminastrivity
of business.
5)
Real
Time feedback (Visual Management)
a. Fitness facilities have mirrors
everywhere
b. How can you see ahead or behind and when
do you react
6)
Coaching
a. The coach/trainer is always there.
b. Coach must be involved, know what the
team is doing
c. It is vitally important for management
to be present.
d.
Another
presentation on developing cultural habits for success by Tim Crocker was
particularly interesting. Frequently well-executed process improvement rollouts
are unsuccessful. Often this result is due to required skills and habits
missing from the culture – not faults in the methodology of the implementation.
The specific cultural habits are coaching, communication, service orientation,
personal accountability, results orientation, and simplification.
·
Communication
o Core competency, meeting structures,
relationships & emotional intelligence
o Determine cultural norms for communication
– face to face, phones before email, meetings with agendas, silence cell phone,
never reply all
o Use a Tier meeting system – daily to monthly
at specific levels of business – map out your structure
·
Coaching
o Routine (1on1), mentoring, focus on
habits and behaviors not results, foster a mindset that craves feedback, use
worksheet
o Understand the change denial curve,
·
Service
Orientation
o Servant leadership, doing more than
required, a belief that you can make a difference, do better for the team.
o Share power and empower your team, be goals
focused, people development, not results focused
·
Personal
Accountability
o Defined responsibilities, clear
expectations, and clear ownership
·
Results
Orientated
o Practice and recognize habits, develop shared
mental models, reward the right habits
·
Simplification
o Habit or practice to use, visualize
information
Changing
your organizations culture and implementing a major project concurrently makes
the difficult nearly impossible. Developing these habits in advance of the roll
out, or any major effort, increases the chance of success. The habits can be
developed and codified through drafting community of practice guide that sets
methods and expectations. There are specific techniques, training, and
workshops to improve and align each of these foundational cultural habits.
These are all skills that can be learned and developed at all levels of the
organization.
The last
presentation of the first day was from Ariens
President and CEO Dan Ariens. Dan
shared his experience and lean journey over the last 15 years leading the
company’s Lean transformation. He believes Lean initiatives are the heart of
American business and the core of its future. The Ariens Company opened it’s
doors to Thedacare to start the Lean Healthcare revolution.
A Lean
journey at its best represents disciplined chaos and those who work at
implementing long-term change understand this contradiction well. But Dan
Ariens credits this chaos for providing an opportunity for everyone in an
organization to become a Lean leader.
The 7 behaviors
of a Lean Leader from Ariens perspective:
1)
Servant
Leaders – are you masters of people or a person of masters
a. Be honest
b. Be fair
c. Keep our commitments
d. Respect the individual
e. Encourage intellectual curiosity
2)
Relentless
Change
a. Leaders must be comfortable in
environment of relentless change
3)
Disciplined
Chaos – You must be disciplined in the chaos
4)
Benevolent
Dictator
a. Be very disciplined about how things are
dealt with in company, rules
5)
Fearless
Anxiety
a. Lots of pressure on a leader – you have
to face the anxiety, be fearless
6)
Cultural
Revolution
a. Leadership commitment – need to have
great leadership to transform
7)
Confident
Humility
a. When you start to feel good about
yourself you lose passion – you lose steam
b. Continuous drive for improvement, it’s a
journey, that’s what is important
c. “Constant pursuit for perfection but
along the way knowing you never reach it but finding success along the way” –
Vince Lombardi.
Stay tuned tomorrow
I’ll share some highlights from the second day of the conference.

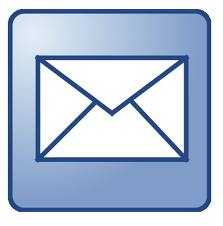




