Luckily, there
is no shortage of literature on Lean Manufacturing over the last several
decades. I have been fortunate to read
many books from a great many authors on a number of aspects on Lean. A good book can be a great place for some to
learn about Lean and how to implement the concepts in their company. The following
is a list of books I recommend on learning Lean in no particular order.
The book that started it all! The Machine That Changed The World is an
excellent read to understand the foundations and history of Lean in the
automotive industry. Womack, Jones and
Roos thoroughly document the whole of the Toyota Production System, pinpoint
the advantages of Lean manufacturing over the prevailing mass-production system
used in the western world at the time, and correctly predicted the rise of Lean
manufacturing principles, not just in automobile manufacturing, but in any
value-creating endeavor.
Lean Thinking is a follow on from
The Machine That Changed The World, written by Daniel Jones & James
Womack. It is a more practical book in
that it explains the ‘how to’ of lean manufacturing. It does not necessarily delve deeply into the
step by step actions required to implement a specific lean tool. Rather it sets out the guiding principles
that should govern any lean implementation.
Learning to See is a spiral bound
workbook that is perfect for Lean practitioners. It takes the reader step-by-step through the
process of creating a value stream map.
It does this by way of a worked example in the book. Each section is clearly laid out and contains
clear diagrams and informative sidebars.
This book is produced in the same
format as Learning to See. The focus of
this book though is on creating flow throughout a process. This is a natural progression from Learning
to See. In a lean transformation, a
value stream map is used to identify opportunities for improvement. Once a process has been identified as a
constraint, this workbook can be used to improve the flow at a process level.
The Toyota Way (2003)
by Jeffrey Liker
Outlining the 14 principles of the
Toyota Production System, this is a must read for anyone interested in lean
manufacturing. Prior to the publication of the Toyota Way, the vast majority of
the Lean literature focused on describing the tangible, technical aspects of
the Toyota Production System. Without
understanding the accompanying business philosophies and management principles,
most organizations that attempted to mimic Toyota failed to generate the same –
if any – level of results.
The Toyota WayFieldbook (2005) by Jeffrey Liker and David Meier
Following on from the previous
recommendation, this fieldbook takes the 14 principles of the Toyota Production
System and provides a hands-on implementation guide. There are case studies, tips to help and
traps to avoid as well as reflection questions in each section.
Written by Pascal Dennis this
“leader’s guide to planning and execution” gives a clear walkthrough the
process of strategy deployment. The book
is designed to provide readers with a framework for understanding the key
components of strategy deployment: agreeing on the company's “True North,”
working within the PDCA cycle, getting consensus through “catchball,” the
deployment leader concept and A3 thinking. It links action to theory and
reminds us that lean tools - like value-stream maps, kaizen events, and 5S -
are only the means to an end, not ends in themselves. Highly recommended if you
need to clarify, align and focus on your major initiatives.
David Mann’s superb work on how to
sustain lean conversions. Learn about
the four key principles of lean management: leader standard work, visual
controls, daily accountability process and discipline. This book may not
contain all of the tools or knowledge you need to sustain Lean conversions, but
the practical examples and methods for engaging team leaders, supervisors and
managers in the daily maintenance of a Lean operating system through an
expanded definition of standard / standardized work, makes this highly
accessible book required reading for anyone attempting a serious Lean
deployment.
Very
few people on the planet can claim the level of real-world Lean success that
Art Byrne can. Perhaps, no other book
provides such a deep dive into the strategic nature of Lean or the role of
senior leaders in driving change.
Certainly, none that can back up the theory and discussion with such
dramatic and concrete results as Mr. Byrne and his time spent as CEO of
Wiremold. This book is a must-read for
any executive looking to create and sustain a successful Lean organization.
Gemba Kaizen
(1997) by Masaaki Imai
With
the publication of his book Kaizen in 1986, Masaaki Imai brought the Japanese
philosophy of continuous improvement to light.
In the sequel, Gemba Kaizen, Mr. Imai enlightens the world to another core
Lean concept: the gemba. By combining a
focus on incremental, small improvements with a thorough understanding of “the
real place”, the book has contributed significantly to the mindset of the
present-day Lean thinker. As a bonus,
the text includes several case studies from real-world application of the gemba
kaizen approach.
Toyota Kata
(2009) by Mike Rother
This
may not be the best book with which to start your Lean journey, but it is
certainly the direction you should head in which to finish. Only those who have struggled to find Lean
success will fully appreciate the power of the kata methodology. Of all the texts on Lean and continuous
improvement, Toyota Kata achieves what no other book before it has fully
accomplished: translating Lean into a set of simple, practical routines, organized
around improvement and coaching, that can be readily and effectively practiced
at all levels of an organization. Rother
cuts down many long-standing fallacies about the practice of Lean, such as the
misunderstanding of common Lean “tools” and the misconception of waste
elimination. In doing so, Mr. Rother
places the focus right where it should be: on the development every person in
the organization through a habit of problem solving and the achievement of continuous
improvement.
Now
here's a book for managers! Bob Emiliani provides an analysis into lean
management and the role managers play in developing a Lean culture. He explains
the purposes, advantages, myths, and misinformation surrounding Lean management
- the application of Lean principles to those management and leadership
positions. Real Lean is a practical guide to Lean management, complete with
interesting and informative linkages to historical events and long-forgotten
perspectives in Lean.
Have you read
any of these? What would you recommend
to others? What is your favorite Lean book?

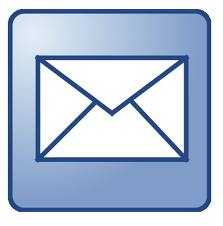




