Some may say that it’s impossible to eliminate mistakes. And they are right; it is, most of the time. But, to be honest, they are missing the point.
Poka yoke, or
mistake proofing, describes any behavior changing constraint that is built into
a process to prevent an incorrect operation or act occurring. The three aims of mistake proofing are:
- To reduce the risk of mistakes or errors arising.
- To minimize the effort required to perform activities.
- To detect errors prior to them impacting on people, materials, or equipment.
Ideally,
poka-yoke ensures that proper conditions exist before actually executing a
process step, preventing defects from occurring in the first place. Where this
is not possible, poka-yoke performs a detective function, eliminating defects
in the process as early as possible.
This can be
achieved by following the 6 principles or methods of mistake proofing. These
are listed in order of priority in fundamentally addressing mistakes:
1. Elimination seeks to eliminate an error-prone
process step by redesigning the product or process so that the task or part is
no longer necessary. This may require redesigning a new process or product
simplification or part consolidation that avoids a part defect or assembly
error in the first place.
Example:
An example of elimination is the use of ambient-light sensors to turn
outside lighting on and off.
2. Prevention modifies the product or process so that
it is impossible to make a mistake or that a mistake becomes a defect. This
includes Limit switches to assure that a part is correctly placed or fixtured
before process is performed; part features that only allow assembly the correct
way, unique connectors to avoid misconnecting wire harnesses or cables, part
symmetry that avoids incorrect insertion.
Example: An example would be a camera
that will not function when there is not enough light to take a picture. Also
some clothes dryers shut down when they detect an overheating situation.
3. Replacement substitutes a more reliable process to
improve repeatability. This includes use of robotics or automation that
prevents a manual assembly error.
Example: An example would be the
implementation of an automatic dispenser to insure the correct amount of
adhesive is applied during an assembly process or the coin dispenser in food
stores preventing that customers are getting short changed.
4. Facilitation is the most used principle and employs
techniques and combining steps to make a process step easier to perform or less
error-prone. This includes visual controls including color coding, marking or
labeling parts to facilitate correct assembly; checklists that list all tasks
that need to be performed; exaggerated asymmetry to facilitate correct
orientation of parts.
Example: An example would be to color
code parts that are similar in shape. This would make it easier to identify the
correct part for assembly. Another example would be the use of a slipping-type
torque wrench to prevent over tightening. When gas stations introduced unleaded
gasoline, the nozzle on the leaded pump was designed to be too big to fit into
an unleaded tank, thereby preventing mistakes. Electrical outlets have been
mistake proofed to assure proper polarity. It is impossible to put a plug in an
outlet incorrectly.
5. Detection involves identifying a mistake before
further processing occurs so that the operator can quickly correct the defect.
This includes sensors in the production process to identify when parts are
incorrectly assembled; scales to measure and control the weight of a package;
built-in self-test capabilities in products.
Example: Examples would include a weld
counter to ensure the correct number of welds or a software modification that
will not allow incorrect entries. Also warning device, using sound and light, like
the seat belt buzzers, can be used to predict when something is about to go
wrong.
6. Mitigation seeks to minimize the effects or the
mistake. This includes mechanisms that reduce the impact of a error and defect;
products designed with low-cost, simple rework procedures when an error is
discovered; extra design margin or redundancy in products to compensate for the
effects of errors.
Example: An example would be a smoke or
heat detector detecting a hazardous situation. Also fuses to prevent overloading
circuits resulting from shorts are mitigation techniques.
Ideally,
mistake-proofing should be considered during the development of a new product to
maximize opportunities to mistake-proof through design of the product and the
process (elimination, replacement, prevention and facilitation). Once the
product is designed and the process is selected, mistake proofing opportunities
are more limited (prevention, facilitation, detection and mitigation).
Eradicating human
errors is crucial to any business. Errors cost money and impact customer
satisfaction. By introducing simple measures to trap and stop errors
organizations can not only save costs but also become more efficient.

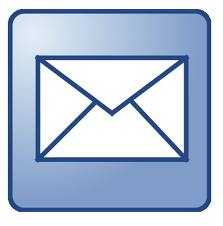




