Drew Dudley investigates everyday leadership in this compelling talk. So many times, people celebrate leadership for things that nobody else has done — groundbreaking, life-changing actions. Unfortunately, this tends to devalue everyday instances of leadership. Dudley encourages listeners to redefine leadership to when they change somebody's understanding of how powerful and important they are.
I hope you enjoyed Drew’s video as much as I did. Drew and I think alike about leadership and making a difference – and he explains it well.
How did you answer the questions Drew asked in this video?
- Are you completely comfortable with calling yourself a leader?
- Do you have to change the world to be called a leader?
- What is it that you must do, be, or have to be called a leader?
Everyone!
Why do I say everyone is a leader? Because each of us influence/lead people every day. Our actions impact/lead other people whether we think so or not. Our actions affect the people around us for better or worse. Just by being you, you are leading someone by example.

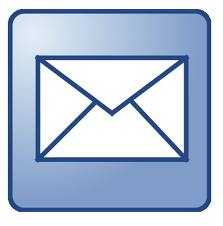




